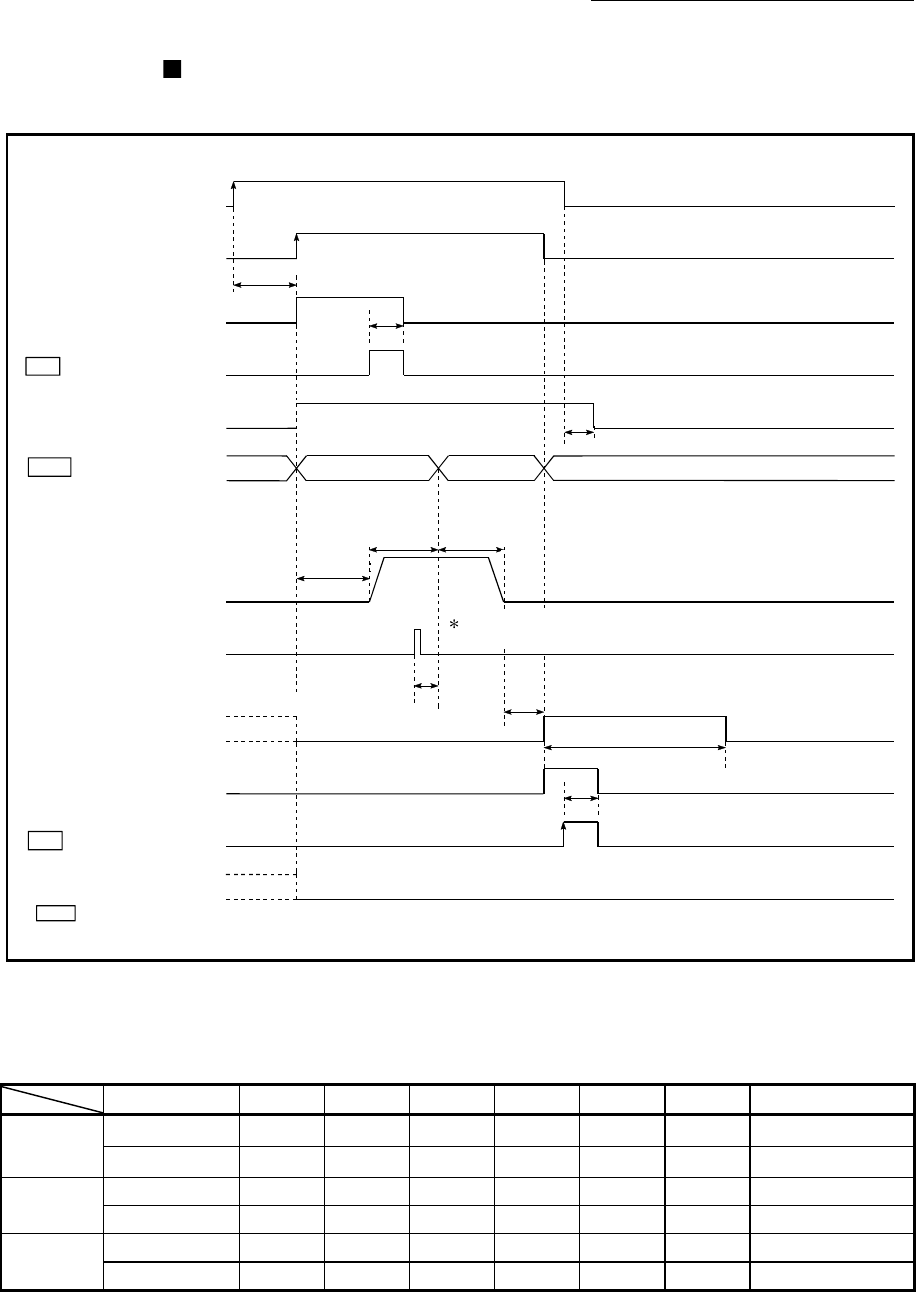
9 - 107
Chapter 9 Major Positioning Control
Operation timing and processing time during speed-position switching
control (ABS mode)
[QD77MS4 operation example]
Positioning start signal
BUSY signal
M code ON signal
[X4, X5, X6, X7](WITH mode)
Standby
Speed control
Start complete signal
Positioning operation
Positioning complete signal
M code ON signal (AFTER mode)
t1
t2
t3
t5
t2
t7
Position control
Speed
control
Position
control
Speed-position switching
command
t6
Speed control carried out until speed-position switching
signal turns ON
Md.26 Axis operation status
OPR complete flag
( Md.31 Status: b4)
Cd.7 M code OFF request
Cd.7 M code OFF request
Standby
[XC, XD, XE, XF]
[X10, X11, X12, X13]
[X14, X15, X16, X17]
[X4, X5, X6, X7]
t4
[Y10, Y11, Y12, Y13]
(Note): Refer to Section 3.3 for input/output signal of QD77MS16.
Fig. 9.17 Operation timing and processing time during speed-position switching control (ABS mode)
Normal timing time Unit: [ms]
Operation cycle t1 t2 t3 t4 t5 t6 t7
QD77MS2
0.88 0.2 to 0.3 0 to 0.9 0 to 0.9 1.8 to 2.7 0 to 0.9 0.2 Follows parameters
1.77 0.2 to 0.3 0 to 1.8 0 to 1.8 2.5 to 3.9 0 to 1.8 0.2 Follows parameters
QD77MS4
0.88 0.2 to 0.3 0 to 0.9 0 to 0.9 1.8 to 2.7 0 to 0.9 0.2 Follows parameters
1.77 0.2 to 0.3 0 to 1.8 0 to 1.8 2.5 to 3.9 0 to 1.8 0.2 Follows parameters
QD77MS16
0.88 0.3 to 1.4 0 to 0.9 0 to 0.9 1.8 to 2.7 0 to 0.9 0.2 Follows parameters
1.77 0.3 to 1.4 0 to 1.8 0 to 1.8 3.2 to 3.9 0 to 1.8 0.2 Follows parameters
The t1 timing time could be delayed by the operation state of other axes.
When using the near-point dog signal and "[Cd.46] Speed-position switching command", the
t6 timing time could be delayed or vary influenced by the PLC scan time or communication
with servo amplifier.