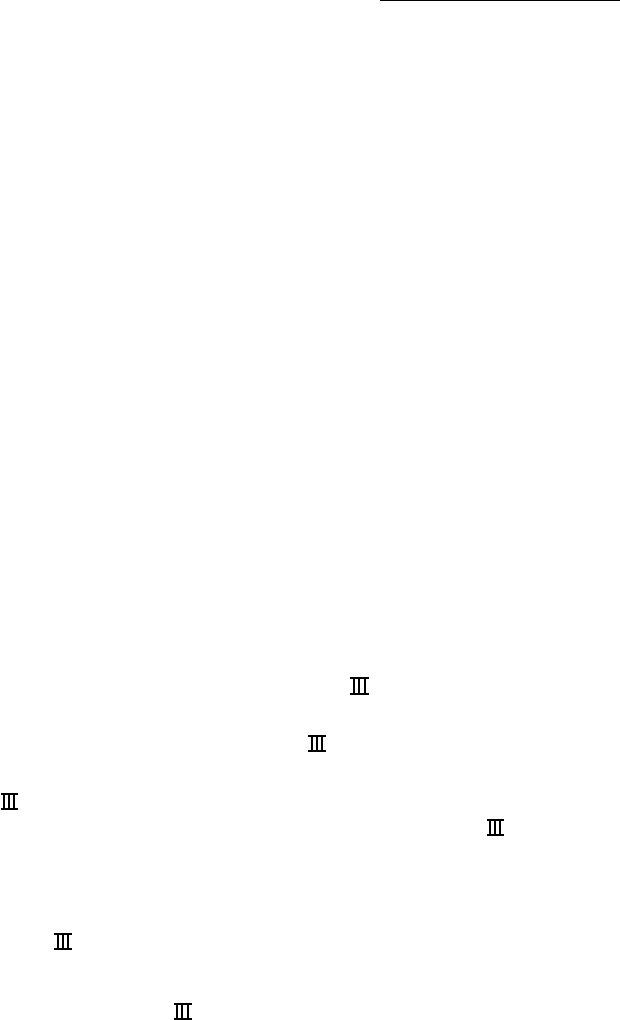
1 - 4
Chapter 1 Product Outline
(7) Setting, monitoring, and testing through GX Works2
Parameters and positioning data for the QD77MS can be set using GX Works2
(Simple Motion Module Setting).
Moreover, using the test function of GX Works2 (Simple Motion Module Setting),
users can check the wiring status and the validity of the preset parameters and
positioning data by performing test operation before creating a program for
positioning control.
The control monitor function of GX Works2 allows user to debug programs
efficiently.
The servo parameters can be set easily by using the GX Works2 in combination
with the MR Configurator2.
(8) Compatibility with the LD77MH/QD75MH
The proven programs in LD77MH/QD75MH can be used because the QD77MS
is compatible with the LD77MH/QD75MH.
(9) Forced stop function
The batch forced stop is available for all axes of servo amplifier by the forced
stop input signal of the external input.
"Valid/Invalid" of the forced stop input signal can be selected by the parameters.
(10) Connection between the QD77MS and servo amplifier with high
speed synchronous network by SSCNET (/H)
The QD77MS can be directly connected to the Mitsubishi servo amplifiers of
MR-J4-B/MR-J3-B series using the SSCNET
(/H)
. Also, it can be directly
connected to the Mitsubishi servo amplifiers of MR-JE-B series using the
SSCNET
/H.
(a) Because the high speed synchronous network by SSCNET
(/H)
is used
to connect the QD77MS and the servo amplifier, or servo amplifiers,
saving wiring can be realized. The maximum distance between the
QD77MS and servo amplifier, servo amplifier and servo amplifier of the
SSCNET
cable on the same bus was set to 50(164.04)[m(ft.)], and the
flexibility will improve at the system design.
(b) By the use of SSCNET
cable (Optical communication), influence of
electromagnetic noise and others from servo amplifier, etc. are reduced.
(c) The servo parameters can be set on the QD77MS side to write or read
them to/from the servo amplifier using the SSCNET communication.
(d) The actual current value and error description contained in the servo can
be checked by the buffer memory of the QD77MS.
(e) The communication between the MR Configurator2 and servo amplifiers is
possible via the PLC CPU.