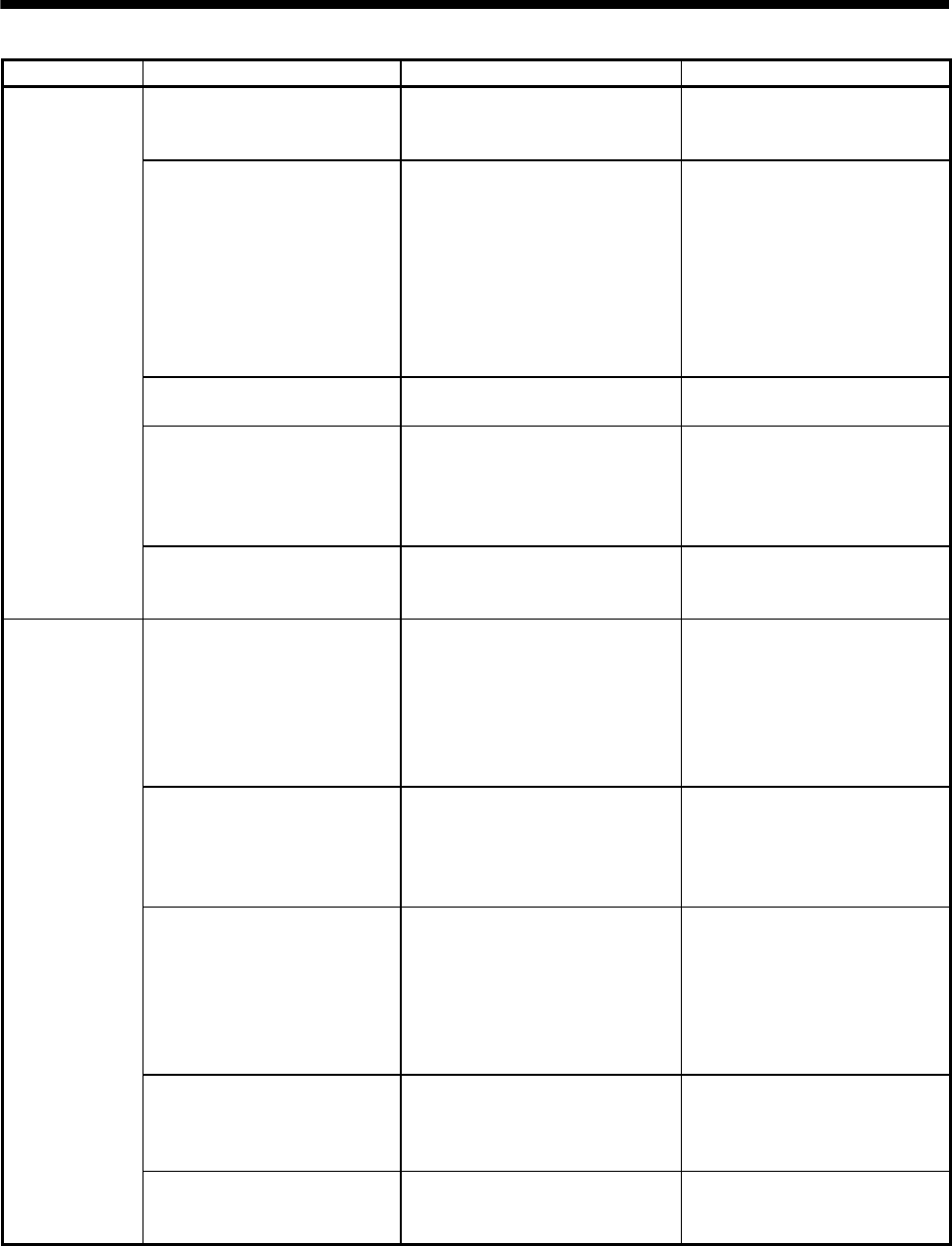
9 - 19
9. TROUBLESHOOTING
Phenomena Checkpoint Estimated cause Action
The servo motor
speed is not
accelerated. Or
too fast.
Check the settings of the speed
command, the speed limit and the
electronic gear.
The setting of the speed command,
the speed limit or the electronic gear
is incorrect.
Review the settings of the speed
command, the speed limit and the
electronic gear is incorrect.
Check the external input signal is
on or off.
1. Check with the external I/O
signal display in the diagnostic
mode.
2. Check the I/O signal status on
the "I/O interface display"
command on the "Monitor"
menu on MR Configurator.
<Speed control mode/torque control
mode>
The setting of the speed selection 1
(SP1), the speed selection 2 (SP2) or
the speed selection 3 (SP3) is
incorrect.
1. Review the wiring.
2. Check the setting of the speed
selection 1 (SP1), the speed
selection 2 (SP2) and the speed
selection 3 (SP3).
Check the power supply cable of
the servo motor.
An output circuit is open. Review the wiring of the servo
motor power supply cable.
Check that the main circuit power
voltage is not low.
The main circuit power voltage
decreased.
1. Set the main circuit power supply
within the specified range of the
permissible voltage fluctuation.
2. Review the wiring of the main
circuit power supply.
Check the power supply for the
servo motor with an
electromagnetic brake.
The electromagnetic brake is not
released.
Turn the electromagnetic brake
power on to release the brake.
The servo motor
vibrates due to
low frequency.
If the safe operation is possible,
repeat acceleration/deceleration 4
times or more to complete the auto
tuning.
The load to motor inertia moment
ratio by the auto tuning is not
estimated correctly.
The load to motor inertia moment
ratio setting (parameter No.PB06) is
incorrect when the auto tuning mode
2 or the manual mode is used.
Adjust the gains.
(Refer to chapter 7.)
Review the load to motor inertia
moment ratio (parameter No.PB06)
when the auto tuning mode 2 or the
manual mode is used.
Check commands from the
controller.
Commands from the controller are
unstable.
1. Review the commands from the
controller.
2. Check the command cable if
errors do not occur such as
breaking.
Check the mechanical part if
errors do not occur.
(Examples)
1. Check that the timing belt is not
loose.
2. Check that the machine is not
worn.
The load of the mechanical part is
changed.
1. Adjust the gains again.
(Refer to chapter 7.)
2. Maintain the mechanical part.
Check the machine required
torque does not exceed the
maximum torque of the servo
motor.
The acceleration/deceleration torque
overshot at stop due to exceed its
servo motor performance.
Reduce loads by setting the
acceleration/deceleration longer or
making the work mass lighter, etc.
Increase the auto tuning response
(parameter No.PA09). (except the
manual mode)
1. The servo gain is low.
2. The auto tuning response is low.
Increase the auto tuning response
and then adjust the gains again.
(Refer to chapter 7.)