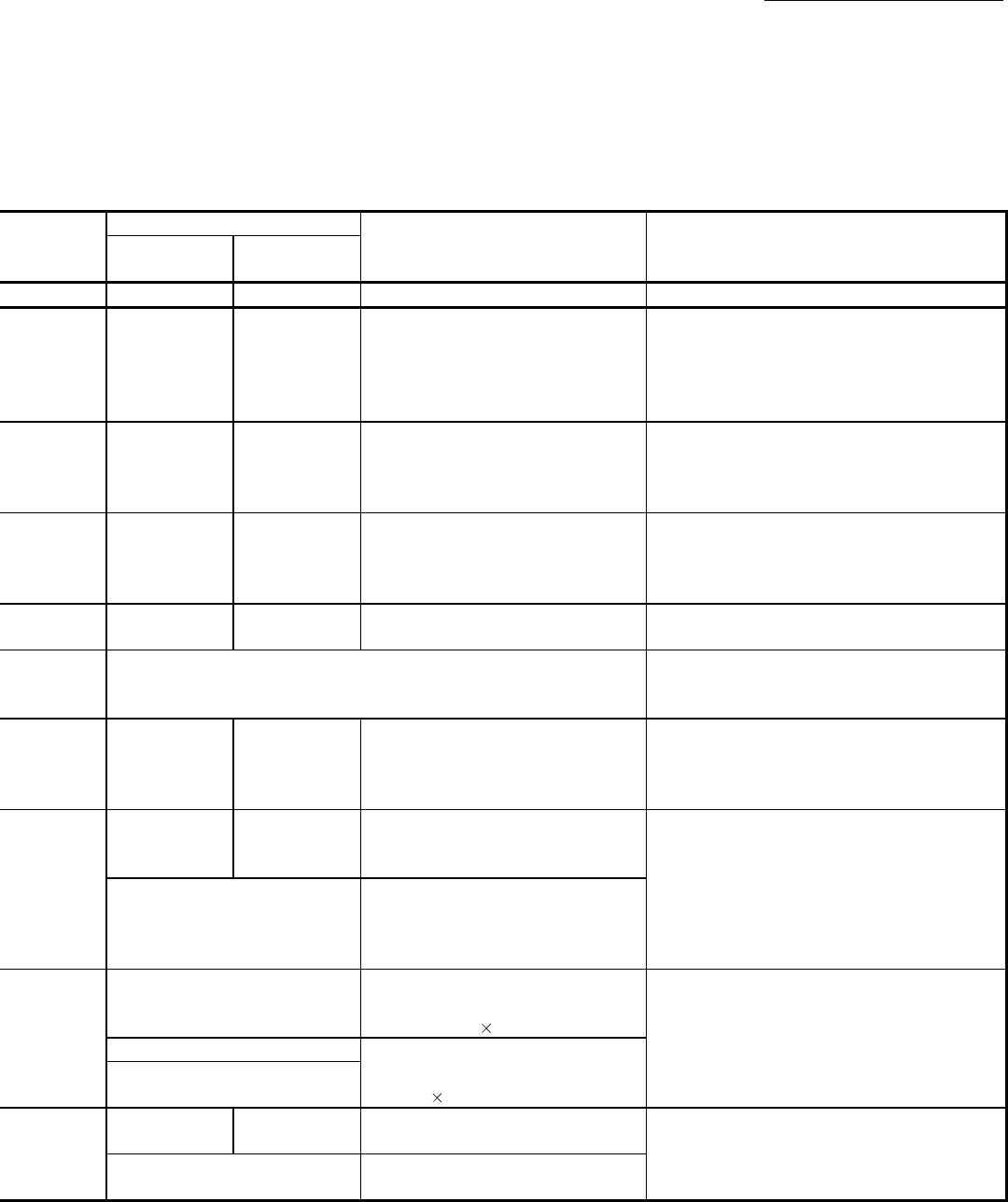
16 - 55
Chapter 16 Troubleshooting
Related buffer memory address
Set range
(Setting with sequence program)
Remedy
QD77MS2
QD77MS4
QD77MS16
— — — —
— — —
• Normalize the start request ON timing.
• When in speed control mode/torque control mode,
start positioning after switching to the position control
mode.
1503+100n 4303+100n
<Restart command>
1: Restart
Normalize the start request ON timing.
(Refer to Section 6.5.5)
(Do not issue the restart command when the axis
operation is not stopped.)
1548+100n
1549+100n
4348+100n
4349+100n
<Teaching data selection>
0, 1
<Teaching positioning data No.>
1 to 600
Carry out the teaching request when the axis is not
BUSY. (Refer to Section 13.7.4)
1513+100n 4313+100n
<Positioning operation speed override>
1 to 300
Prevent the overridden speed from being reduced to 0.
(Refer to Section 13.5.2)
Same as warning code 109
Request to write when the PLC READY signal [Y0] is
OFF.
1513+100n 4313+100n
<Positioning operation speed override>
1 to 300
Set a value within the setting range.
1525+100n 4325+100n
<New torque value/forward new torque
value >
0 to
[
Torque limit setting value
]
Set a new torque value or a forward new torque value
less than the limit value.
26+150n
<Torque limit setting value>
1 to 1000
Refer to Section 5.3
"List of positioning data"
for command speed
<Command speed>
1 to 1000000000 [PLS/s]
1 to 2000000000 [
10
-2
mm/min or another]
Re-set the command speed/bias speed at start so that
the command speed is equal to or larger than the bias
speed at start.
Bias speed at start
<Bias speed at start>
0 [PLS/s]
0 [
10
-2
mm/min or another]
6+150n
7+150n
1564+100n 4364+100n
<Reverse new torque value>
0 to
[
Torque limit setting value
]
Set a value which does not exceed the torque limit
setting value as the reverse new torque value.
26+150n
<Torque limit setting value>
1 to 1000
n: Axis No.-1