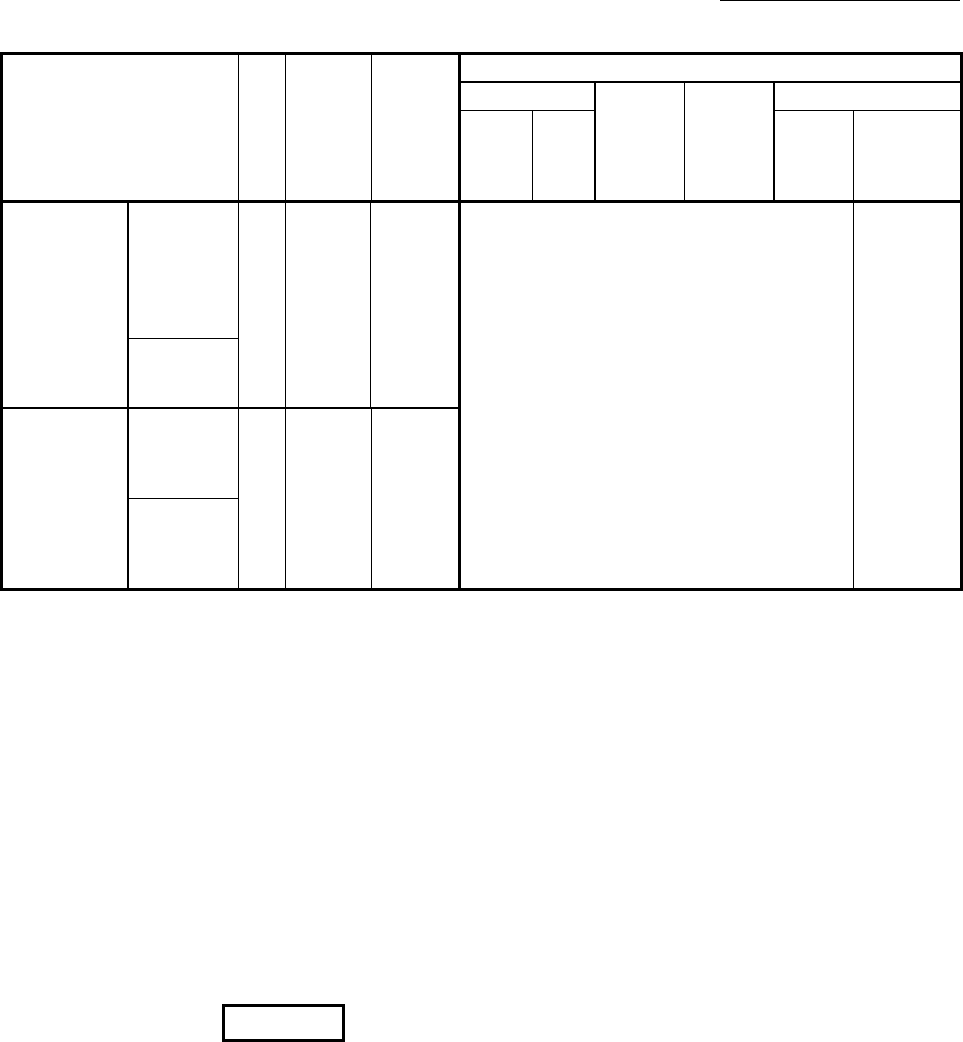
1 - 29
Chapter 1 Product Outline
Stop cause
Stop
axis
M code
ON signal
after stop
Axis
operation
status
after
stopping
([Md.26])
Stop process
OPR control
Major
positioning
control
High-level
positioning
control
Manual control
Machine
OPR
control
Fast
OPR
control
JOG/
Inching
operation
Manual
pulse
generator
operation
Relatively safe
stop
(Stop group 3)
Axis error
detection
(Error other
than stop
group 1 or 2)
(Note-1)
Each
axis
No
change
Error
Deceleration stop/sudden stop
(Select with "[Pr.39] Stop group 3 sudden stop
selection".)
Deceleration
stop
"Stop" input
from
GX Works2
Intentional stop
(Stop group 3)
"Axis stop
signal" ON
from PLC
CPU
Each
axis
No
change
Stopped
(Standby)
"Stop signal"
of external
input signal
ON
(Note-1): If an error occurs in a positioning data due to an invalid setting value, when the continuous positioning control uses multiple
positioning data successively, it automatically decelerates at the previous positioning data. It does not stop suddenly even the
setting value is sudden stop in stop group 3. If any of the following error occurs, the operation is performed up to the positioning
data immediately before the positioning data where an error occurred, and then stops immediately.
• No command speed (Error code: 503)
• Outside linear movement amount range (Error code: 504)
• Large arc error deviation (Error code: 506)
• Software stroke limit + (Error code: 507)
• Software stroke limit - (Error code: 508)
• Sub point setting error (Error code: 525)
• End point setting error (Error code: 526)
• Center point setting error (Error code: 527)
• Outside radius range (Error code: 544)
• Illegal setting of ABS direction in unit of degree (Error code: 546)
REMARK
Provide the emergency stop circuits outside the servo system to prevent cases
where danger may result from abnormal operation of the overall system in the event
of an external power supply fault or servo system failure.