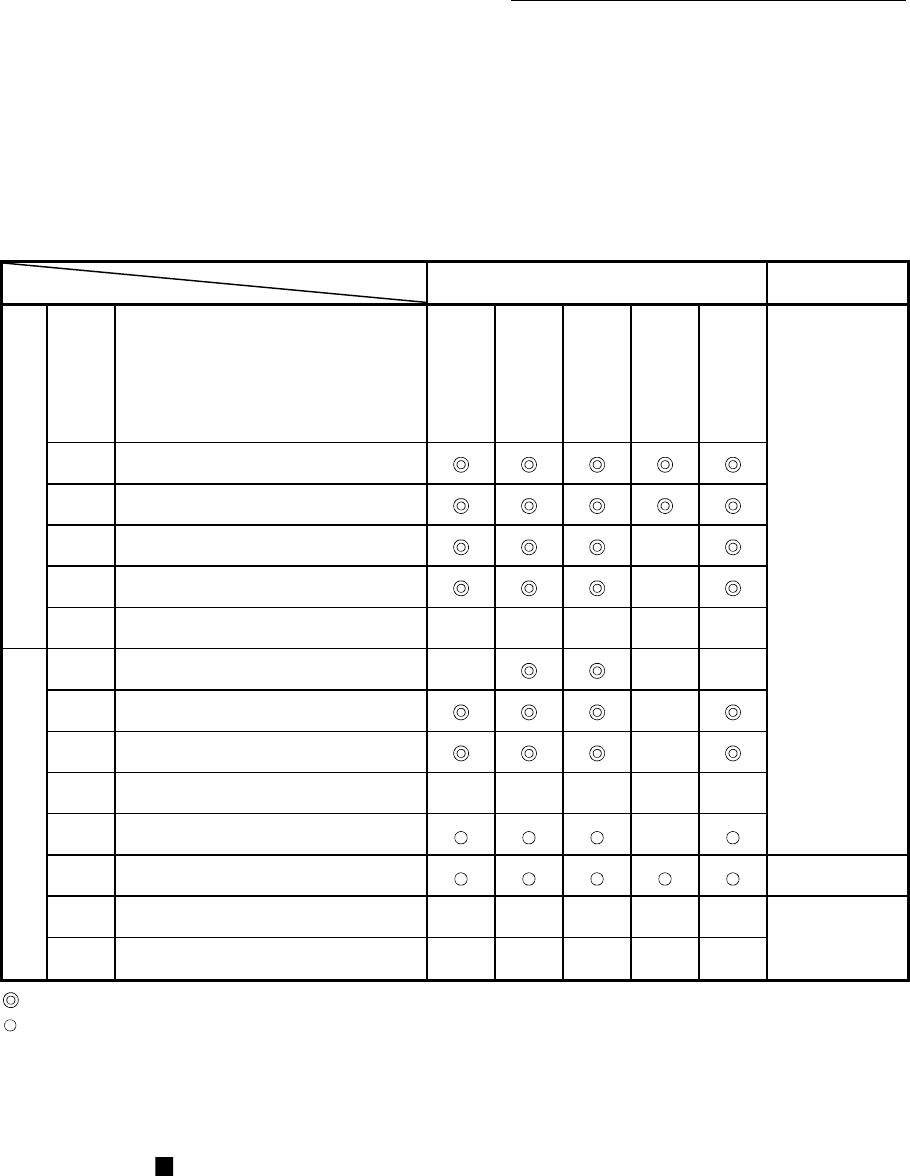
5 - 7
Chapter 5 Data Used for Positioning Control
5.1.3 Setting items for OPR parameters
When carrying out "OPR control", the "OPR parameters" must be set. The setting
items for the "OPR parameters" are shown below.
The "OPR parameters" are set for each axis.
Refer to Chapter 8 "OPR control" for details on the "OPR control", and refer to Section
5.2 "List of parameters" for details on each setting item.
OPR control
OPR parameters
Machine OPR control
Fast
OPR control
OPR basic parameters
[Pr.43] OPR method
Near-point dog
method
Count method 1)
Count method 2)
Data set method
Scale origin signal
detection method
Preset parameters
are used for
machine OPR
control.
[Pr.44] OPR direction
[Pr.45] OP address
[Pr.46] OPR speed
–
[Pr.47] Creep speed
–
[Pr.48] OPR retry R R R – –
OPR detailed parameters
[Pr.50]
Setting for the movement amount after
near-point dog ON
–
– –
[Pr.51] OPR acceleration time selection
–
[Pr.52] OPR deceleration time selection
–
[Pr.53] OP shift amount
S S S
–
S
[Pr.54] OPR torque limit value
–
[Pr.55] Operation setting for incompletion of OPR
–
[Pr.56] Speed designation during OP shift S S S – S
Preset parameters
are used for
machine OPR
control.
[Pr.57] Dwell time during OPR retry R R R – –
: Always set
: Set as required
– : Setting not required (The setting value is invalid. When the value is the default value or within the setting range,
there is no problem.)
R : Set when using the "13.2.1 OPR retry function" ("–" when not set)
S : Set when using the "13.2.2 OP shift function" ("–" when not set)
Checking the OPR parameters
[Pr.43] to [Pr.57] are checked with the following timing.
When the "PLC READY signal [Y0]" output from the PLC CPU to the Simple
Motion module changes from OFF to ON.
When the positioning test of GX Works2 is executed.