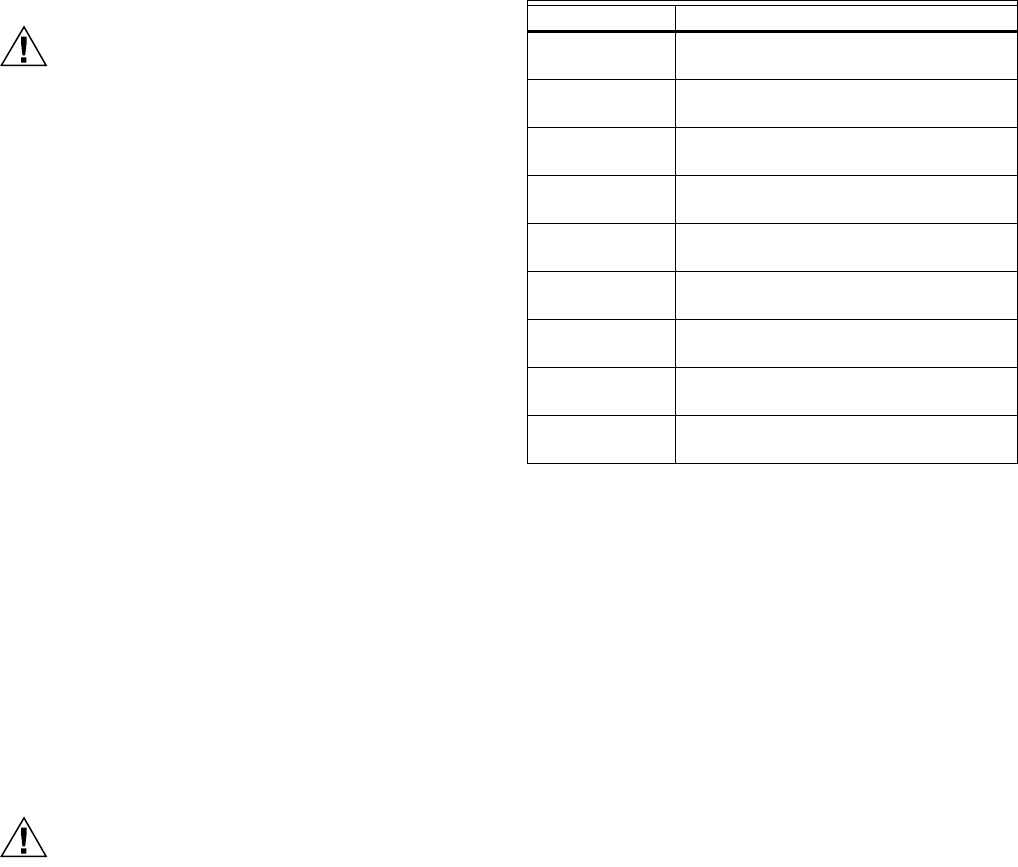
WEBVISION™
95-7769—01 52
CVAHU PID
Purpose
Adjust PID (Proportional Integral Derivative) control
parameters for the CVAHU.
Mode
Configuration can be performed with the wizard Off-line or
On-line.
CAUTION
Equipment Damage Possible.
Can cause short cycling of compressors or wide
swings in space temperature and excessive
overdriving of modulating outputs.
If large or frequent change to PID control parameters
is made, it is possible to cause equipment problems
such as short cycling compressors (if the stage
minimum run times were disabled). Other problems
that can occur include wide swings in space
temperature and excessive overdriving of modulating
outputs.
The default values provide proper control for most
applications. If the PID parameters require adjustment away
from these values, use caution to ensure that equipment
problems do not arise. If any change to PID control
parameters is made, the adjustments should be gradual. After
each change, allow the system to stabilize so the effects are
accurately observed. Make further refinements as needed
until the system is operating as desired.
If the default values are changed and you want to reset them,
add a second CVAHU Controller to the subnet, record then re-
enter the default PID values to the first CVAHU.
Procedure
1. Click the PID button on the left pane to open the PID
Configuration page.
2. Enter information into available fields.
3. Click Commit to save the settings or Reset to revert to
the last saved settings.
4. Click Next to display the Custom Wiring page or Back
to display the Miscellaneous Parameters
Configuration page.
CAUTION
Equipment Damage Possible.
Setting Control Band too low may cause large over or
undershooting of setpoint.
The smaller the Control Band, the more responsive the control
output. Be careful not to set the Control Band (heating,
cooling, or econ) too low. This can happen if the space or
discharge sensors or wiring are in noisy environments and the
value reported to the controller is not stable (such that it
bounces). The Control Band is used only in modulating
control, and has no purpose when staged control is
configured.
CVAHU PID fields
Table 26 lists the CVAHU PID fields.
NOTE: Throttling Range or Proportional Gain determines
what impact the error has on the output signal.
Decreasing the Throttling Range amplifies the effect
on the error, that is, for a given error (the difference
between the measured space temperature and the
current actual space temperature setpoint), a small
Throttling Range causes a higher output signal
value.
Integral Time
Determines what impact the error-over-time has on the output
signal. Error-over-time has two components that make up its
value: the amount of time the error exists and the size of the
error. The higher the integral time, the slower the control
response. In other words, a decrease in Integral Time causes
a more rapid response in the output signal.
Derivative Time or Gain
Determines what impact the error rate has on the output
signal. The error rate is how fast the error value is changing. It
can also be the direction space temperature is going, either
towards or away from the setpoint and its speed - quickly or
slowly. A decrease in Derivative Time causes a given error
rate to have a larger effect on the output signal.
Table 26. CVAHU PID Fields.
Name Definition
Cooling
Proportional Gain
Enter the range in degrees 2 to 30 DDF
(1.1 to 16.7 DDK).
Cooling
Integral Gain
Enter the range in seconds (0 to 5,000).
Cooling
Derivative Time
Enter the range in seconds (0 to 9,000).
Heating
Proportional Gain
Enter the range in degrees 2 to 30 DDF
(1.1 to 16.7 DDK).
Heating
Integral Gain
Enter the range in seconds (0 to 5,000).
Heating
Derivative Gain
Enter the range in seconds (0 to 9,000).
DA Heating
Control Band
Enter the range in degrees 5 to 30 DDF
(2.8 to 16.7 DDK).
DA Cooling
Control Band
Enter the range in degrees 5 to 30 DDF
(2.8 to 16.7 DDK)
Econ
Control Band
Enter the range in degrees 5 to 30 DDF
(2.8 to 16.7 DDK).