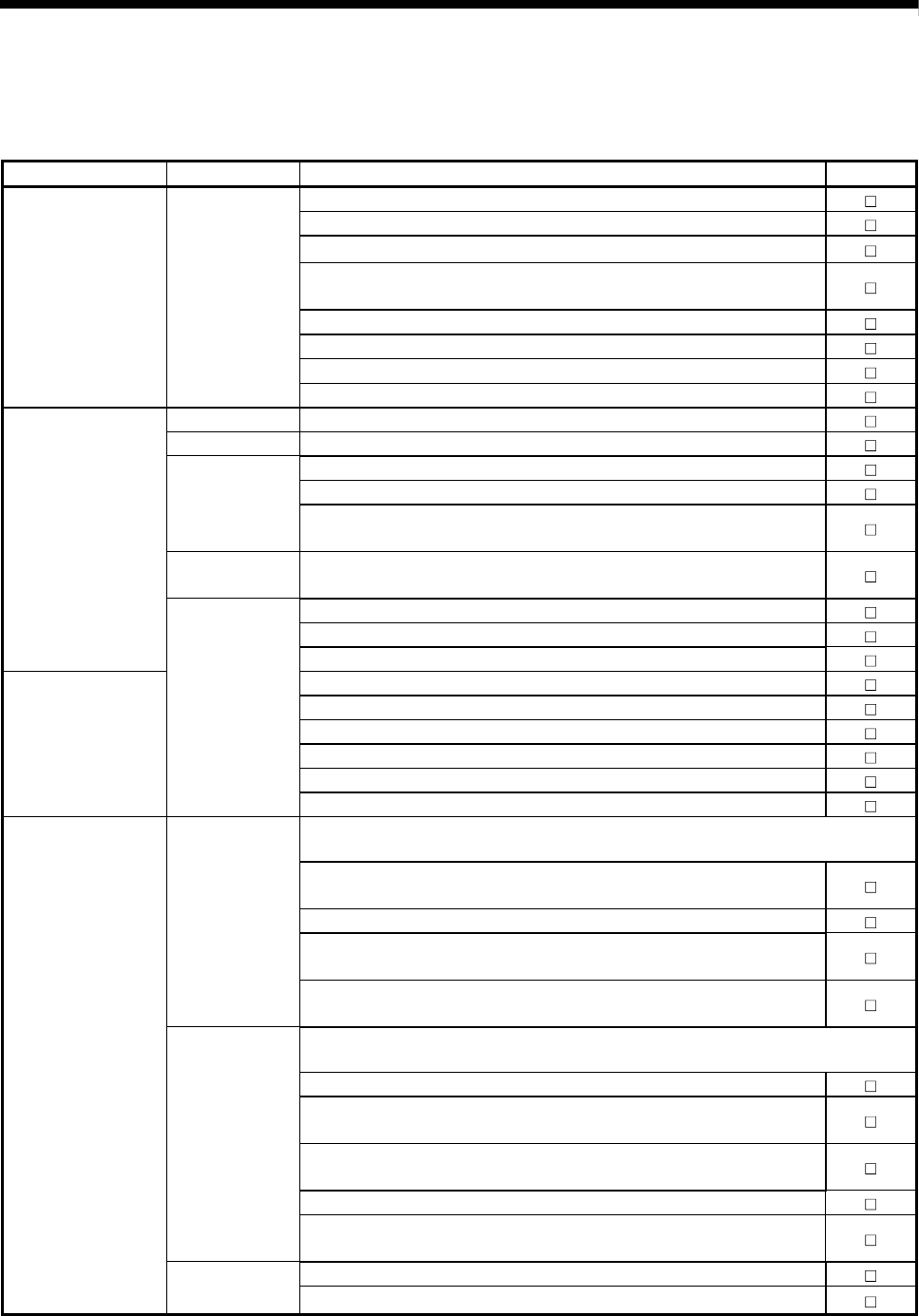
5 - 8
5 TRIAL OPERATION AND ADJUSTMENT
5.4 Trial Operation and Adjustment Checklist
At the worksite, copy the following table for use as a check sheet.
Work Step Item Trial Operation and Adjustment Confirmation
Check
Check that the each module is installed correctly.
Check that the each connector is connected correctly.
Check the each terminal screw for looseness.
Check that the earth wires of power supply module or servo amplifiers, etc.
are correct.
Check that the servomotor wiring is correct.
Check that the regenerative option wiring are correct.
Check that the circuit of emergency stop and forced stop are correct.
Before power supply
ON
Installation of
unit/module
and basic wiring
Check that the wiring of each power supply and I/O are correct.
OS installation Check that the operating system software is compatible.
System setting Check that the system setting is correct.
Check that the upper/lower stroke limit inputs are correct.
Check that the STOP signal input is correct.
Q172LX external
signals
Check that the proximity dog and speed/position switching signal inputs are
correct.
Program/positioni
ng data
Check that the Motion program, PLC program and positioning data are stored
in the PLC/Motion CPU module correctly.
Check the communications with servo amplifiers.
Check that the rotation direction for JOG operation is correct.
Power supply ON/
Motion CPU module
in STOP status/
PLC CPU module in
STOP status
Check that the upper/lower limit switches operate correctly.
Check that the rotation at maximum command speed is motor rating or less.
Check that the machine operates correctly by the JOG operation.
Check that the machine stops by the upper/lower stroke limit.
Check that the machine stops by the emergency stop or forced stop.
Check that the home position return is executed correctly.
Motion CPU module in
RUN status/
PLC CPU module in
STOP status
Basic axis
operations
(Check each axis)
Check that each positioning control of Motion program is operates correctly.
Check the each operation in manual operation mode of system during Motion program
execution.
Check that the machine operation stops immediately by the emergency stop
or forced stop.
Check the operation of each actuator and confirmation limit switch.
Check that the emergency stop, forced stop and equipment alarm signals are
correct.
Manual operation
Checks in compliance with control specifications specific to system and
equipment.
Check the each operation in manual operation mode of system during Motion program
execution.
Check that the automatic operation motions.
Check that the machine operation stops immediately by the emergency stop
or forced stop.
Check that the module or equipment alarm causes an immediate stop or cycle
stop.
Check that the restoring operation can be performed after an alarm stop.
Automatic
operation
Make other checks in compliance with control specifications specific to system
and equipment.
Check that the acceleration/deceleration torque is maximum torque or less.
Motion CPU module in
RUN status/
PLC CPU module in
RUN status
Torque check
Check that the continuous effective load torque is rated torque or less.