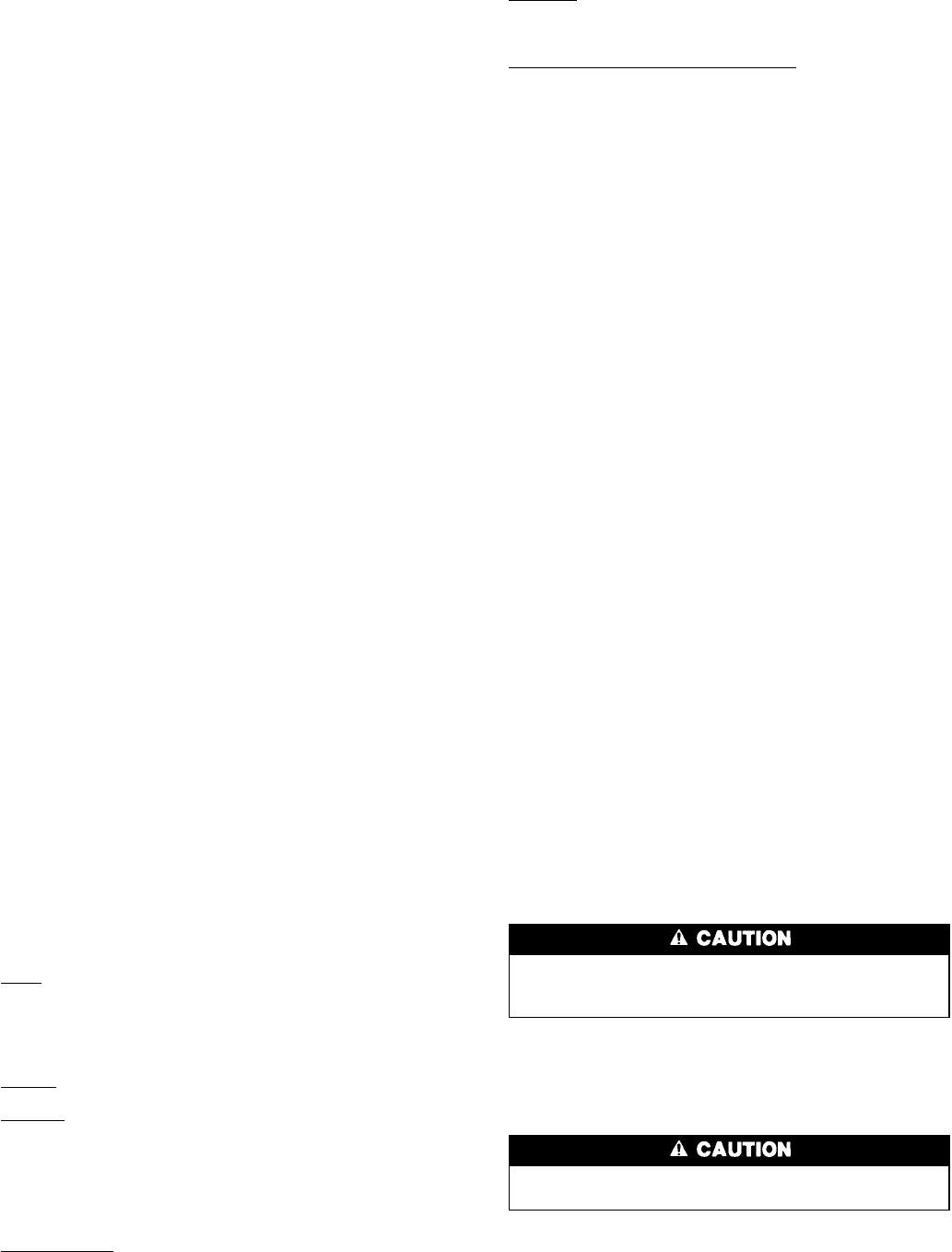
Fill the gear drive to the recommended oil level with heated
Shell VSI grade 68 oil or its equivalent, heated between
110 and 120 F (43 and 49 C). Do not overfill. Immediately
close the openings to keep the vapors in the housing.
Inspect the unit every 30 days and spray or add rust in-
hibitor suitable for anticipated storage conditions, as
required.
Drain and replace the oil with the recommended oil type
prior to start-up.
• Remove the breather and replace it with a pipe plug. Pack
the entire seal area with grease to form a vapor barrier and
seal it with tape.
A vapor-phase rust inhibitor, such as Daubert Chemical,
Non-Rust Motorstor VCi-10 or its equivalent, may be added
to the recommended oil type in the amount of 2% of the
total sump capacity. Fill the unit to the recommended level.
Do not overfill.
Inspect the unit every 30 days and spray or add rust in-
hibitor suitable for anticipated storage conditions, as
required.
The unit may run without changing this oil mixture.
EXTENDED DOWNTIME — Consider the length of down-
time the unit will undergo. The lubricating oil used in the
unit should protect the interior parts for up to 30 days of
shutdown. If the unit will be shut down longer than 30 days,
it must be operated a minimum of 30 minutes every 30 days
to distribute the lubricant to all interior parts.
If it is impractical to operate the unit every 30 days, the
long-term storage instructions described above must be fol-
lowed. All seals applied for this storage condition must be
removed before operating the unit.
Compressor Bearing Maintenance — The key to
good bearing maintenance is proper lubrication. Use the proper
grade of oil, maintained at recommended level, temperature,
and pressure. Inspect the lubrication system regularly and
thoroughly.
Only a trained service technician should remove and
examine the bearings. The bearings should be examined on
a scheduled basis for signs of wear. The frequency of ex-
amination is determined by the hours of chiller operation,
load conditions during operation, and the condition of the
oil and the lubrication system. Excessive bearing wear can
sometimes be detected through increased vibration or in-
creased bearing temperature. If either symptom appears, con-
tact an experienced and responsible service organization for
assistance.
External Gear Maintenance — Perform the re-
quired maintenance and recommended intervals. Good pre-
ventive maintenance prolongs the life of the unit.
Daily
• Inspect for leaks and loose connections.
• Check the oil level.
• Check the oil temperature and pressure.
• Check for unusual noise and/or vibration.
Weekly — Check the oil filter.
Monthly
• Obtain oil sample analysis.
• Clean or replace oil filters.
• Check the foundation mounting bolts for tightness.
• Clean the air filter.
• Check the operation of all auxiliary equipment.
Semi-Annually
• Check gear tooth wear.
• Check the oil and replace it if necessary.
• Check the coupling alignment.
Annually
• Check the heat exchanger for corrosion and clogged tubes.
• Check the bearing clearance and end play.
Disassembly and Assembly Instructions — The following in-
structions apply to standard high speed gear units.
• Required Equipment: In addition to standard mechanic’s
tools, have the following equipment on hand: hoist, sling,
torque wrench, feeler gages, and dial indicator.
• General Instructions: Clean external surfaces of the gear
unit before removing the cover to prevent contaminants
from falling into it. Record the mounting dimensions and
the location of accessories for reference when reassem-
bling. To remove the gear from its operating area, discon-
nect all connected equipment and lift the gear from its
foundation using 4 lifting lugs.
Inspect the Heat Exchanger Tubes
COOLER — Inspect and clean the cooler tubes at the end of
the first operating season. Because these tubes have internal
ridges, a rotary-type tube cleaning system is necessary to fully
clean the tubes. Upon inspection, the tube condition deter-
mines the scheduled frequency for cleaning and indicates
whether water treatment is adequate in the chilled water/
brine circuit. Inspect the entering and leaving chilled water
temperature sensors for signs of slime, corrosion, or scale.
Replace the sensor if corroded or remove any scale if found.
CONDENSER — Since this water circuit is usually an open-
type system, the tubes may be subject to contamination and
scale. Clean the condenser tubes with a rotary tube cleaning
system at least once per year and more often if the water is
contaminated. Inspect the entering and leaving condenser wa-
ter sensors for signs of slime, corrosion, or scale. Replace
the sensor if corroded or remove any scale if found.
Higher than normal condenser pressures, together with the
inability to reach full refrigeration load, usually indicate dirty
tubes or air in the chiller. If the refrigeration log indicates a
rise above normal condenser pressures, check the condenser
refrigerant temperature against the leaving condenser water
temperature. If this reading is more than what the design dif-
ference is supposed to be, then the condenser tubes may be
dirty, or water flow may be incorrect. Because HFC 134a is
a high-pressure refrigerant, air usually does not enter the chiller;
rather, the refrigerant leaks out.
During the tube cleaning process, use brushes especially
designed to avoid scraping and scratching the tube wall. Con-
tact your Carrier representative to obtain these brushes. Do
not use wire brushes.
Hard scale may require chemical treatment for its pre-
vention or removal. Consult a water treatment specialist
for proper treatment.
Water Leaks — Water in the refrigerant is indicated dur-
ing chiller operation by the refrigerant moisture indicator on
the refrigerant motor cooling line. Water leaks should be re-
paired immediately.
The chiller must be dehydrated after repair of water leaks.
See Chiller Dehydration section, page 49.
Water Treatment — Untreated or improperly treated wa-
ter may result in corrosion, scaling, erosion, or algae. The
services of a qualified water treatment specialist should be
obtained to develop and monitor a treatment program.
82