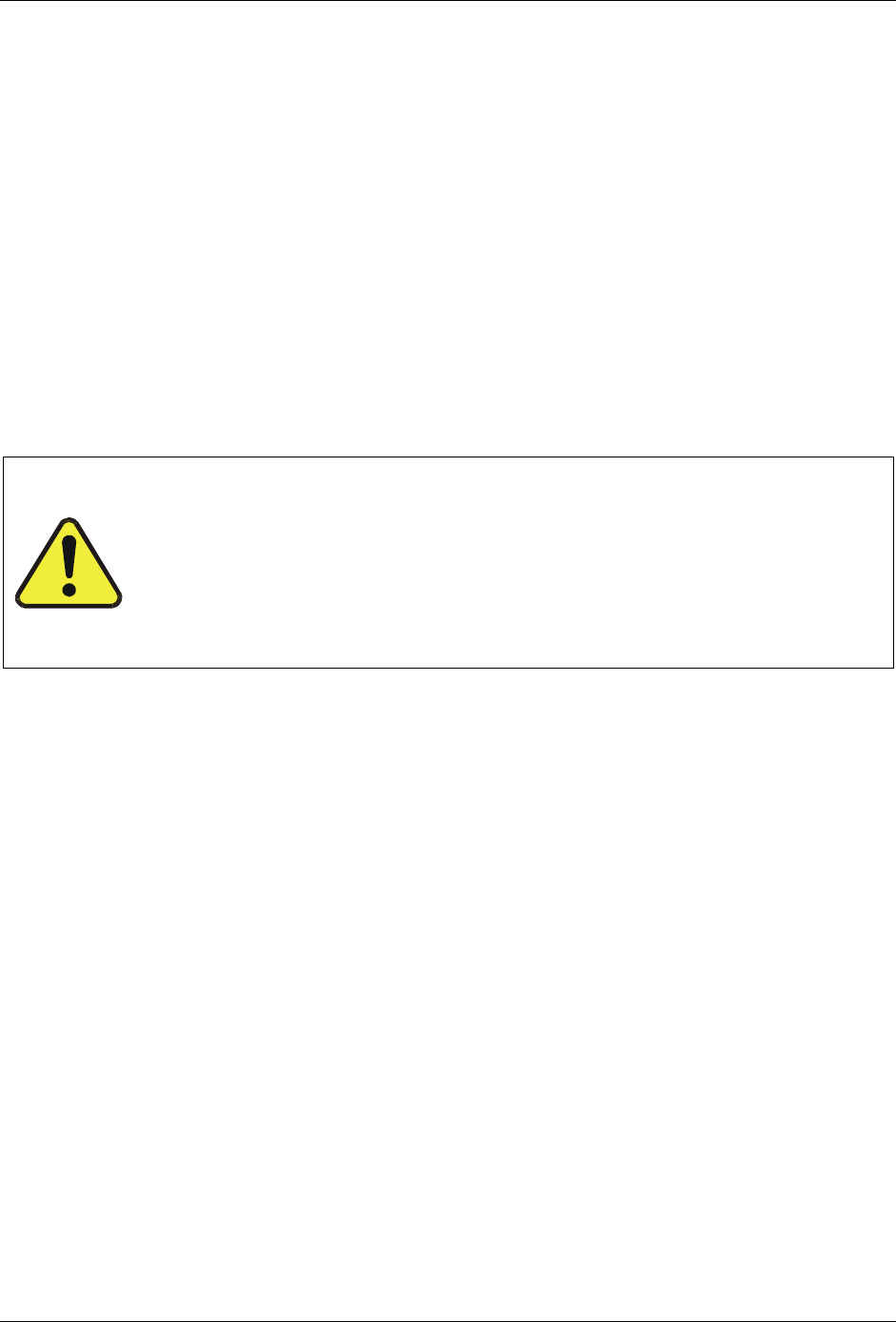
Maintenance Schedule and Procedures Teledyne API Model T360/T360M Operation Manual
192
4. Pressurize the instrument with the leak checker, allowing enough time to fully
pressurize the instrument through the critical flow orifice. Check each fitting
with soap bubble solution, looking for bubbles. Once the fittings have been
wetted with soap solution, do not re-apply vacuum, as it will suck soap
solution into the instrument and contaminate it. Do not exceed 15 psi
pressure.
5. If the instrument has one of the zero and span valve options, the normally
closed ports on each valve should also be separately checked. Connect the
leak checker to the normally closed ports and check with soap bubble
solution.
6. Once the leak has been located and repaired, use a clean, absorbent, and
lint-free material to remove any residual soap solution from the instrument
interior. The leak-down rate should be < 1 in-Hg (0.4 psi) in 5 minutes after
the pressure is shut off.
6.3.4. Performing a Sample Flow Check
CAUTION
Always use a separate calibrated flow meter capable of measuring flows
in the 0 – 1000 cc/min range to measure the gas flow rate though the
analyzer.
DO NOT use the built in flow measurement viewable from the Front Panel
of the instrument. This measurement is only for detecting major flow
interruptions such as clogged or plugged gas lines.
See Figure 3-4 for SAMPLE port location.
1. Attach the Flow Meter to the sample inlet port on the rear panel. Ensure that
the inlet to the Flow Meter is at atmospheric f.
2. Sample flow should be 800 cc/min 10%.
3. Once an accurate measurement has been recorded by the method described
above, adjust the analyzer’s internal flow sensors (see Section 4.13.8)
Low flows indicate blockage somewhere in the pneumatic pathway, typically a
plugged sintered filter or critical flow orifice in one of the analyzer’s flow control
assemblies. High flows indicate leaks downstream of the Flow Control
Assembly.
6.3.5. Cleaning the Optical Bench
The T360 sensor assembly and optical bench is complex and delicate.
Disassembly and cleaning is not recommended. Please check with the factory
before disassembling the optical bench.
6.3.6. Cleaning the Chassis
If necessary, the exterior surfaces of the T360 can be cleaned with a clean damp
cloth. Do not submerge any part of the instrument in water or cleaning solution.
07272B DCN6552