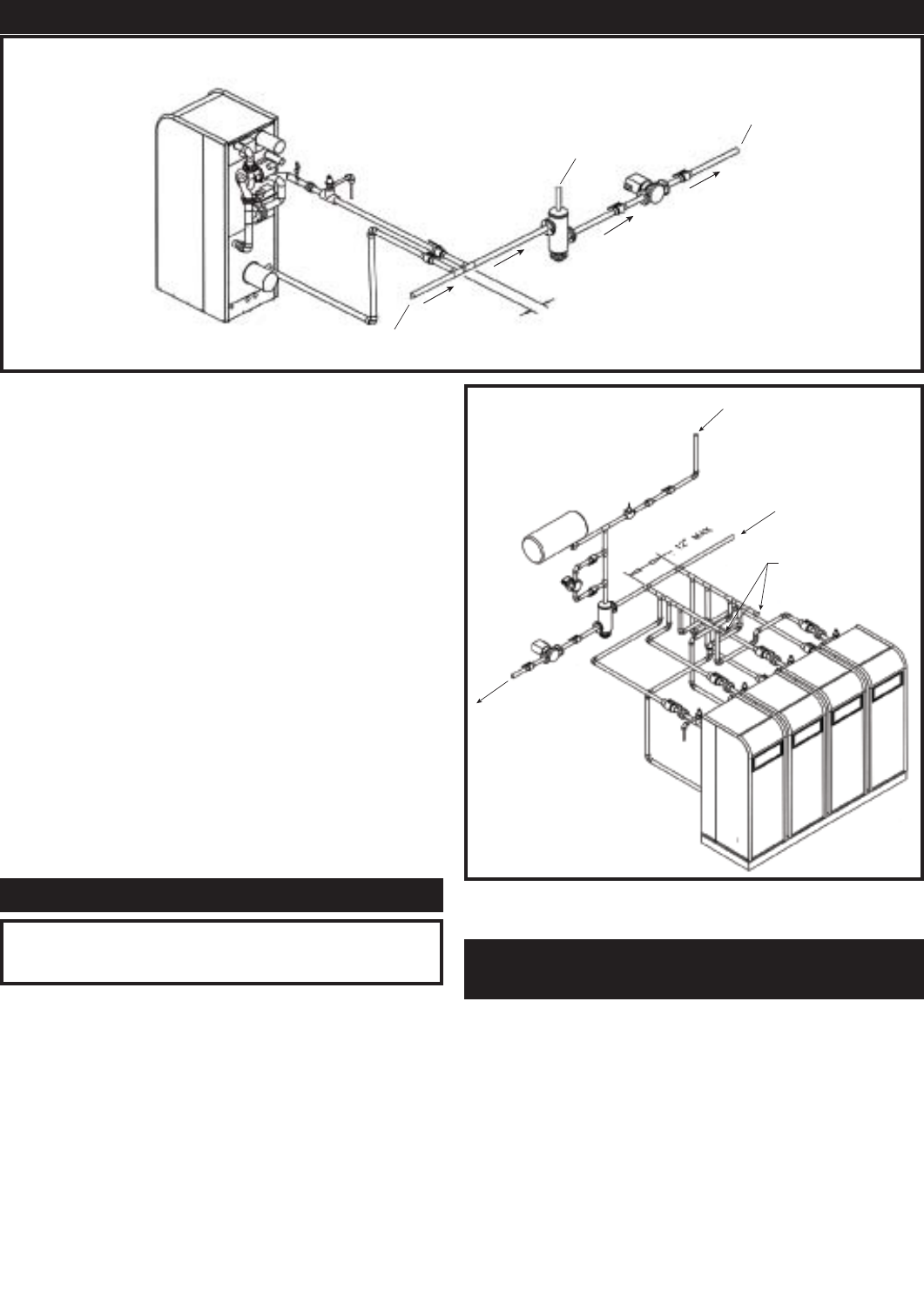
66
PRIMARY/SECONDARY BOILER PIPING
TO EXPANSION TANK
AND MAKEUP WATER SYSTEM
TO SYSTEM
12” MAX.
FROM SYSTEM
FIG. 80 Primary/Secondary Piping of a Single Boiler
CAUTIONƽ
At no time should the system pressure be less than
12 PSIG.
MAKE-UP WATER
FROM SYSTEM
CAP EACH MANIFOLD
TO SYSTEM
MINIMUM BOILER WATER
TEMPERATURES
Inlet water temperatures below the specified minimum
recommendations can excessively cool the products of combustion
resulting in condensation on the primary heat exchanger. The boiler
is designed to condense only on the secondary heat exchanger.
Conden sa tion on the primary heat exchanger can cause operational
problems, bad combustion, sooting, flue gas spillage and reduced
service life of the related components.
FIG. 81 Primary/Secondary Piping of Multiple Boilers
A properly sized primary system pump provides adequate flow to
carry the heated boiler water to radiation, air over coils, etc. The
fittings that connect the boiler to the primary sys tem should be a
maximum of 12" (0.30 m) (or 4 pipe diameters) apart to ensure
connec tion at a point of zero pressure drop in the primary system.
There should be 10 pipe diameters of straight pipe before and after
the boiler secondary loop connections to prevent turbulent flow at
the secondary loop connections. Multiple boilers may also be
installed with a primary/secondary manifold system. Multiple
boilers should be connected to the common manifold in reverse
return to assist in balancing flow to multiple boilers.
The installer must ensure that the boiler has adequate flow
without ex ces sive temperature rise. Low system flow can result
in overheating of the boiler water which can cause short burner
cycles, system noise relief valve discharge and in extreme cases,
a knocking flash to steam. These conditions indicate the need to
increase boiler flow to and from the boiler. This is generally
accomplished by increasing the diameter of the piping that
connects the boiler to the primary system. A larger di am e ter pipe
reduces head loss and in creas es flow.