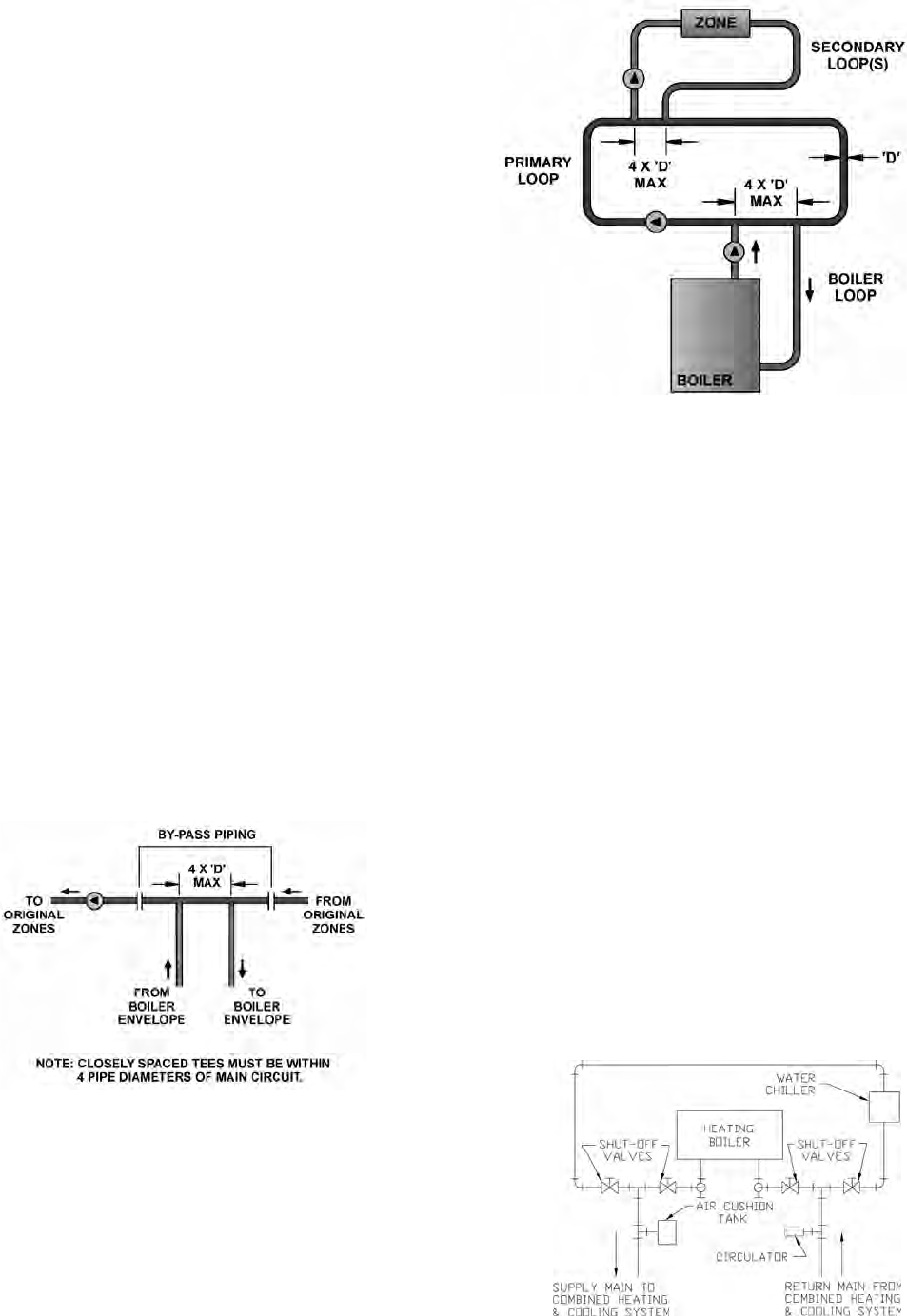
63
a. Temperature and Flow Requirements – An
existing parallel piping system may be used,
provided the return water is not below 80°F and
the return water temperature is not more than
80°F less than the boiler outlet temperature. A
ow analysis should be performed to determine
the ow through the boiler when the minimum
(and smallest) and maximum number of zones
are activated.
Sufcient ow through the boiler must be
maintained. The recommended maximum
temperature difference between the boiler supply
and return water is 40°F. However, a maximum
delta T of 80°F across the boiler is allowable.
A minimum boiler supply water temperature of
130°F must be maintained to avoid sustained
condensing within the combustion chamber.
b. Primary/Secondary Piping - If the conditions
above cannot be met, then parallel piping
systems must be converted to an arrangement
that will provide the proper water ow through
the
boiler at the proper temperatures. Primary/
Secondary piping is a common method for
isolating the boiler from the system. The
concept must be for the boiler loop to inject
heat into a primary loop, provided the return
water into the boiler is at least 80°F. A by-pass
containing two closely spaced tees must be
installed to de-couple the boiler loop from the
primary loop (see Figure 51). The converted
system should resemble Figure 52. Care must
be taken to avoid dead heading the system pump.
Conversions should be reviewed and approved
by a Consulting Engineer or other qualied
professional to avoid system deciencies.
Figure 51: Parallel Piping Conversion
c.
Alternate Piping Arrangements - Piping
arrangements other than Parallel and Primary/
Secondary, such as System Bypass, are
acceptable as long as they ensure that the ow
and
temperature requirements of the boiler are
met.
d. Glycol Antifreeze Solutions - Many systems
today use ethylene or propylene glycol antifreeze
solutions as a measure for freeze protection, as
well as a pump lubricator and corrosion inhibitor.
The properties of the glycol mixture have an
impact on valve and pump sizing. All glycol
solutions have a lower specic heat than water.
This means that the glycol solution cannot
transfer heat as well as pure water, resulting in
the need for higher ow rates. In addition, the
viscosity of the glycol solution is usually higher
than water, requiring a higher pump head for the
same given ow. Consult factory for specic
applications, pump selection and ow rate.
e. If this boiler is used in connection with refriger-
ation systems, the boiler must be installed so that
the chilled medium is piped in parallel with the
heating boiler using appropriate valves to prevent
the chilled medium from entering the boiler. See
Figure 53.
Figure 52: Typical Burnham Boiler -
Primary - Secondary Loop System
Figure 53: Recommended Piping for Combination
Heating & Cooling (Refrigeration) Systems
Multiple boilers are installed the same as single
boiler installations. Each boiler loop will contain
its own boiler circulator (see Figure 49b).
The boiler circulator selection will maintain a
constant and minimum ow through the boiler
during every heat demand. The circulator
must be properly selected, based on the design
temperature between the boiler supply and boiler
return. A boiler circulator must be used with a
primary/secondary piping arrangement.