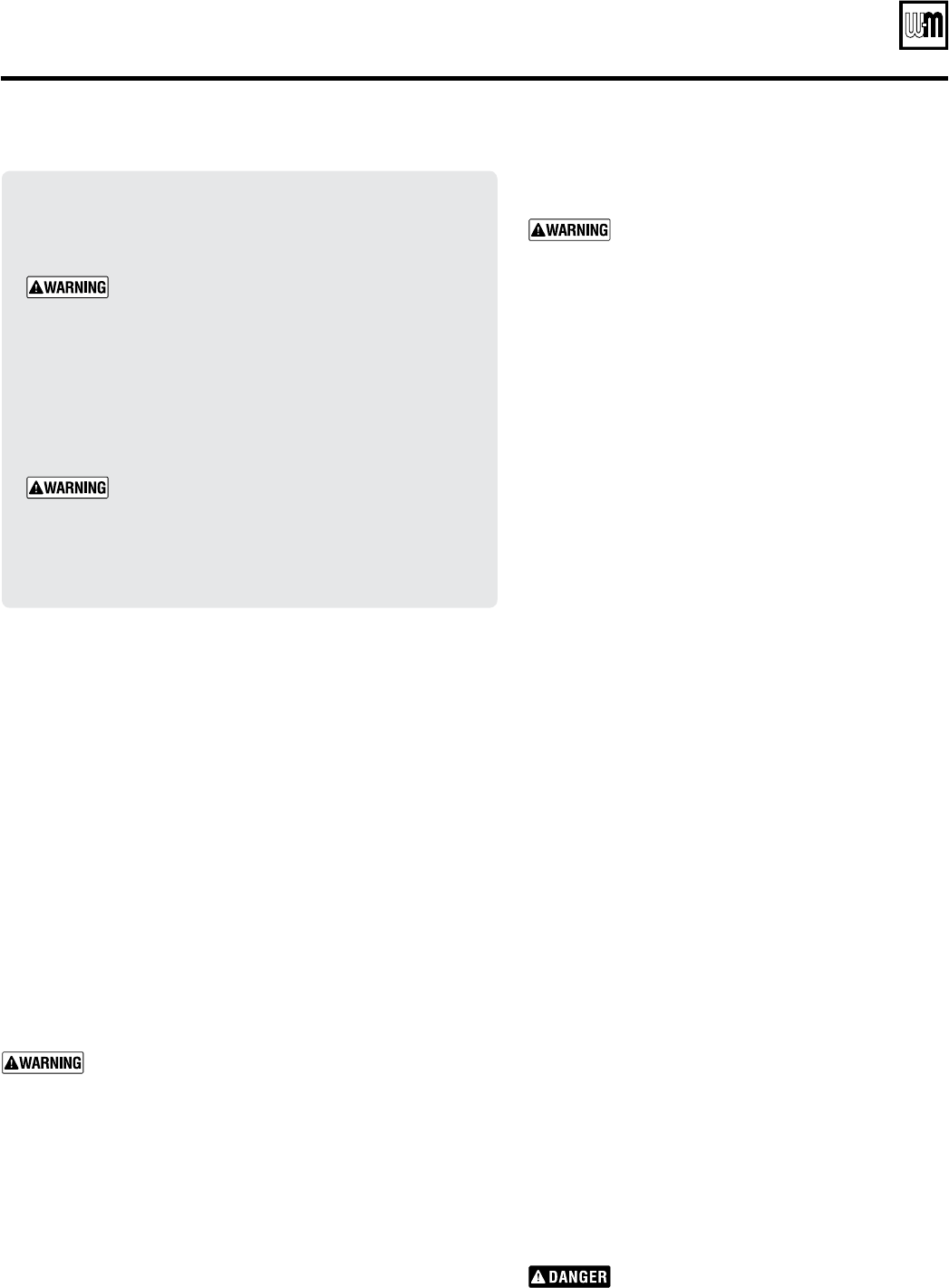
Part number 550-142-054/0411
GV90+ gas-fired water boiler — Boiler Manual
68
Annual start-up
Address reported problems
1. Inspect any problems reported by owner and correct before pro-
ceeding.
Inspect boiler area
1. Verify that boiler area is free of any combustible materials, gasoline
and other flammable vapors and liquids.
2. Verify that air intake area is free of any of the contaminants listed
in Figure 36, page 30. If any of these are present in the boiler intake
air vicinity, they must be removed. If they cannot be removed,
reinstall the air and vent lines per this manual.
Inspect boiler interior
1. Remove jacket top and front door to inspect interior of boiler.
2. Vacuum any sediment and components.
Do not use solvents to clean any of the boiler compo-
nents. The components could be damaged, resulting in
unreliable or unsafe operation.
Inspect condensate drain system
1. Inspect the condensate trap hose for deterioration.
2. Check for any obstructions in the trap hose by squeezing the
tubing.
3. If there is any doubt the condensate drain system is flowing freely,
remove the clamp and hose from the bottom of the recuperator.
Slide a funnel outlet into the trap hose and pour water through. It
should exit at the termination of the condensate drain line.
Inspect all piping for leaks
Eliminate all system or boiler leaks. Continual
fresh make-up water will reduce boiler life.
Minerals can build up in sections, reducing
heat transfer, overheating heat exchanger, and
causing heat exchanger failure. Leaking water
may also cause severe property damage.
1. Inspect all water and gas piping and verify to be leak
free.
2. Look for signs of leaking lines and correct any problems
found.
3. Check gas line using procedure on page 54.
Inspect gas piping
1. Sniff near floor and around boiler area for any indica-
tion of a gas leak.
2. Test gas piping using bubble test, per page 54, if
there is any indication of a leak.
Inspect the water system
1. Verify all system components are correctly installed and
operational.
2. Check the cold fill pressure for the system. Verify it is
correct (usually around 12 PSIG).
3. Watch the system pressure as the boiler heats up (dur-
ing testing) to ensure pressure doesn’t rise too high.
Excessive pressure rise indicates expansion tank sizing
or performance problem.
4. Inspect automatic air vents and air separators. Remove
air vent caps and briefly press push valve to flush vent.
Reinstall caps. Make sure vents do not leak. Replace any
leaking vents.
Check water system chemistry
1. Check system water chemistry (pH and hardness). See
instructions beginning on page 59.
2. Check glycol and glycol inhibitor levels if using glycol/
water mixture. See instructions beginning on page 59.
3. Check Sentinel X100 inhibitor level in the water using
the Sentinel X100 Inhibitor Test Kit. Follow instructions
supplied with the kit. Add X100 inhibitor if needed to
bring to the correct level. (See Figure 96, page 89 for
part numbers.)
Do not use petroleum-based cleaning or
sealing compounds in boiler system
. Se-
vere damage to boiler will occur, resulting in
substantial property damage.
Annual start-up only by qualified
service technician
The boiler should be inspected and started annu-
ally, at the beginning of the heating season, only
by a qualified service technician. In addition, the
maintenance and care of the boiler designated in
Figure 77, page 67 and explained on the follow-
ing pages must be performed to assure maximum
boiler efficiency and reliability. Failure to service
and maintain the boiler and system could result
in equipment failure.
Electrical shock hazard — Turn off power to
the boiler before any service operation on the
boiler except as noted otherwise in this instruction
manual. Failure to turn off electrical power could
result in electrical shock, causing severe personal
injury or death.