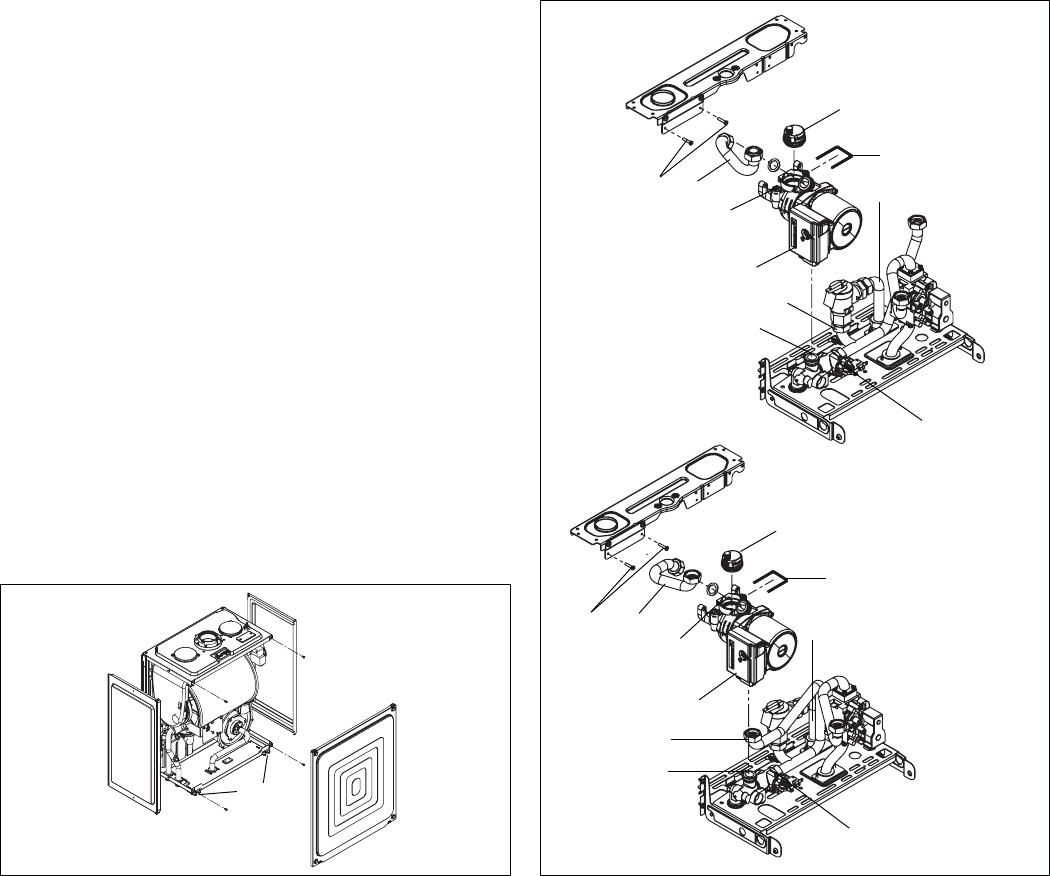
52
PUMP ASSEMBLY (Fig. 69)
Locate and remove the 2 securing screws (A) at the rear of the
pump assembly. Disconnect the flow pipe (B, only for XPak 120)
from the combustion chamber connection, slacken the pipe at the
hydraulic assembly and swing/rotate clear of the pump assembly.
Disconnect and remove the pump outlet pipe (C) from the pump
assembly/combustion chamber connection. Locate and remove
the pressure gauge securing pin (D) and disconnect the
pressure gauge from the pump assembly.
Disconnect the electrical wiring from the pump’s electrical
connection point (E). Remove locking pin (F) from pump base
and lift pump assembly clear of the hydraulic manifold. The
pump assembly can now be removed from the appliance.
Replace carefully in the reverse order.
PRESSURE RELIEF VALVE (Fig. 69)
Disconnect the outlet pipe (L) and the flow pipe (M) from the
safety valve, remove pressure release valve. Replace in the
reverse order.
LOWER AUTOMATIC AIR RELEASE VALVE (Fig. 69)
Locate and remove the AAV locking pin (G) from the pump
assembly and remove the AAV assembly (H). Replace in the
reverse order.
TOP AUTOMATIC AIR RELEASE VALVE (Fig. 70)
Remove the drain pipe (A). Unscrew the top AAV (B). Replace
in the reverse order. Loctite or similar should be used as a thread
sealant for the AAV.
Fig. 68
12 - SERVICING INSTRUCTIONS
1. GENERAL
To ensure the continued safe and efficient operation of the boiler,
it is recommended that it is checked and serviced at regular
intervals. It is essential that any worn or failed component be
replaced only with a genuine XPak spare parts. It should be
remembered that although certain generic components may look
similar, they will be specific to an individual appliance or product
range. Use of non-genuine XPak spare parts could invalidate your
warranty and may pose a potential safety hazard. The frequency of
servicing will depend upon the particular installation conditions,
but in general, once per year should be sufficient. It is the law that
any servicing work is carried out by competent person such as a
Raypak Technician, an approved service agent, or other suitably
qualified personnel. The following instructions apply to the
appliance and its controls, but it should be remembered that the
central heating and the domestic hot water systems would also
require attention from time to time.
2. ROUTINE ANNUAL SERVICING
- Check the operation of the boiler and ensure it functions as
described in Section “11. Checks, adjustments and fault
finding”.
- Thoroughly inspect the boiler for signs of damage or
deterioration especially the flue system and the electrical
apparatus.
- Check and adjust – if necessary – the system design pressure
(see pg. 63 ref. 10).
- Carry out an analysis of the flue gases (pg. 73), and visually
check the condition of the entire flue assembly.
- Check that the burner and main heat exchanger are clean and
free from any debris or obstruction.
- Check and clean – if necessary – the condense trap to ensure
correct operation.
- Compare the performance of the appliance with its design
specification. The cause of any noticeable deterioration should
be identified and fixed without delay.
- The combustion blower motor does not require lubrication for
proper operation. DO NOT attempt to oil the motor or damage
may occur.
3. REPLACEMENT OF COMPONENTS
Although it is anticipated that this appliance will give years of
reliable, trouble free service, the life span of components will be
determined by factors such as operating conditions and usage.
Should the appliance develop a fault, the troubleshooting section
will assist in determining which component is malfunctioning.
4. COMPONENT REMOVAL PROCEDURE
To remove a component, access to the interior of the boiler is
essential. Isolate the appliance from the electrical supply. And
when necessary, close all service valves on the boiler, remove
the casing and drain the water content from the boiler via the
drain valve. Ensure some water absorbent cloths are available
to catch any residual water that may drip from the boiler or
removed component. Undertake a complete commissioning
check, after replacing any component.
ALWAYS TEST FOR GAS TIGHTNESS IF ANY GAS CARRYING
COMPONENTS HAVE BEEN REMOVED OR DISTURBED.
AIR BOX FRONT COVER REMOVAL (Fig. 68)
Locate the two clips and remove air box front cover. If it’s necessary
to remove the air box side cover, locate and remove the 4 securing
screws.
clips
A
B
C
E
D
F
G
H
L
I
A
C
D
E
F
G
H
L
I
XPak 85
M
XPak 120
Fig. 69