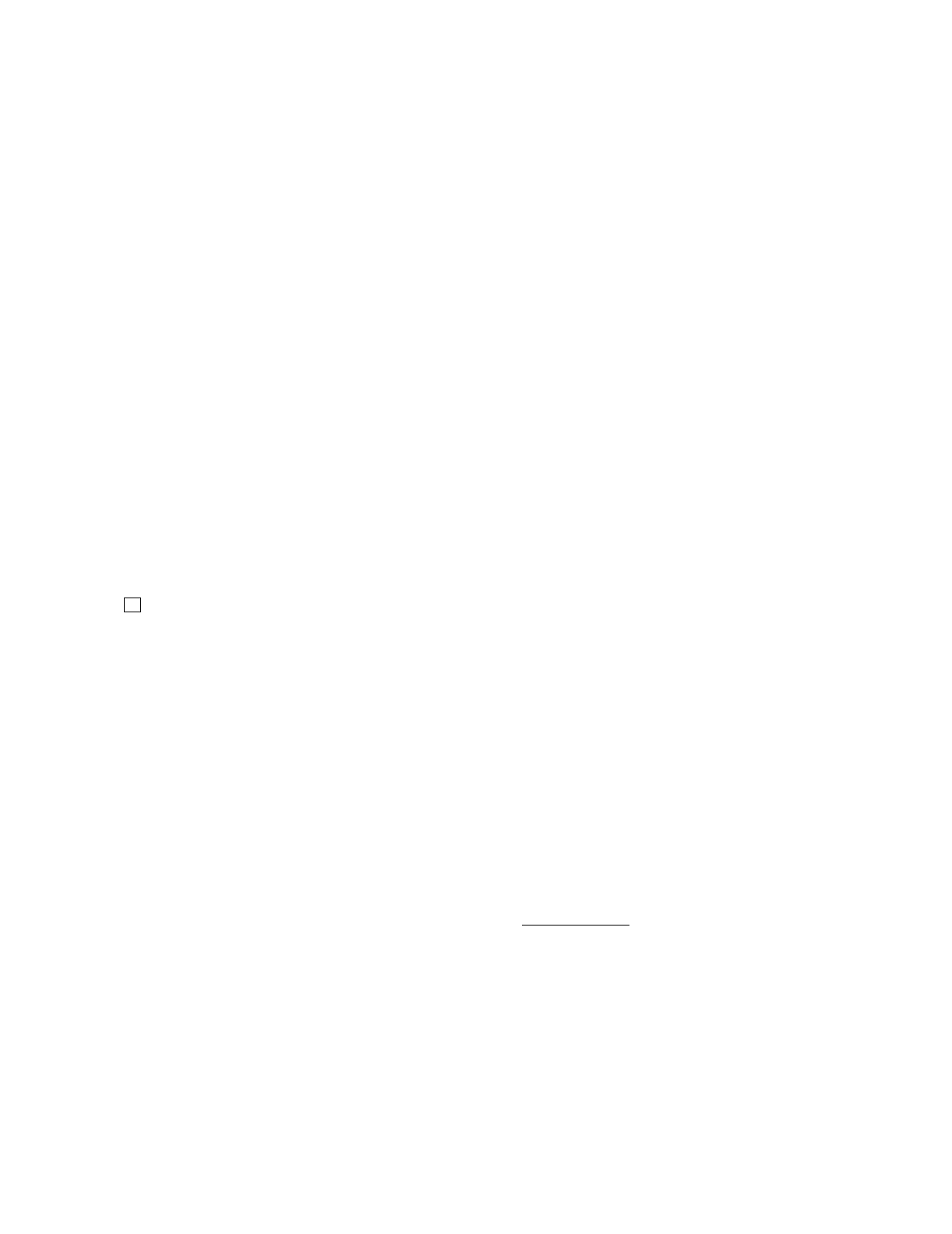
13
A separate service manual for the factory installed PE VFD
is supplied with each unit. Refer to PE VFD manual for more
information on the PE VFD.
Temperature Reset —
Accessory temperature reset al-
lows the unit to automatically adjust (‘‘reset’’) the supply-air
temperature set point to a higher value once most of the space
cooling load has been met. When the space conditions are sat-
isfied, the VAV terminals will close to the minimum position.
All VAV units will sense the decrease in actual supply-air tem-
perature and the unit controls respond by reducing capacity
stages to maintain user-established supply-air set point temper-
ature. When VAV units are also equipped with optional supply
duct pressure controls (either inlet guide vanes [IGV] or vari-
able frequency drive package), the unit also senses an increase
in duct static pressure and responds by closing IGV dampers or
slowing fan wheel speed to maintain user-configured set points
for supply duct pressure. Allowing the supply-air temperature
to be reset to a higher value maintains air circulation in the
space without costly overcooling.
The accessory package is required for temperature reset.
The accessory includes:
• thermistor T10, to monitor space temperature
• reset temperature potentiometer P7, to establish start
temperature for reset operation
• reset limit potentiometer P3, to establish maximum level
of modified supply-air temperature
More than one space sensor may be used if an average
space temperature is desired for initiating temperature reset.
Refer to installation section for sensor part number and wiring
schematic.
Temperature reset will start when space temperature (at
T10) drops to the set point at P7. When Temperature Reset
is active, the LED (light-emitting diode) display will show
code 21 . Automatic adjustment of supply-air temperature set
point will end when modified SASP equals reset limit set point
at P3. (See formula for automatic modification of SASP in
Controls Installation, Space Temperature Reset section on this
page.)
CONTROLS INSTALLATION
The VAV units may be used in applications with additional
control features, options, or accessories. Refer to the appropri-
ate accessory installation instructions for more information on
installing that accessory. Unit control box component arrange-
ment is shown in Fig. 20-22. Control options and accessories
available for VAV units are:
• smoke control modes
• differential enthalpy sensor
• electric heaters (sizes 034-074 only)
• modulating power exhaust
• Motormaster
®
I control
• space temperature reset
• night setback thermostat (field-supplied)
• single step demand limit
• two-step demand limit
• inlet guide vanes
• variable frequency drive
• variable frequency drive remote display kit
Control Wiring —
A switch or timeclock (field supplied)
must be wired in to control when unit will go into and out of
Occupied mode. Connect switch or timeclock between termi-
nals 1 and 2 on terminal block 3 (sizes 034-048) or terminal
block 4 (sizes 054-104) in unit control box. See Fig. 23. The
circuit potential is 24 v.
Variable air volume units equipped with warm-up heat re-
quire that room terminals be controlled to go fully open when
unit goes into the Heating mode. Heating interlock relay (HIR)
is provided for this function. The relay is located in the unit
control box. When unit goes into Heating mode, interlock relay
is energized providing switch closure or opening (depending
on how field power source is set up) to open the room termi-
nals. Field connections for interlock relays are terminals 3 and
4 (for normally open contacts) and terminals 3 and 7 (for nor-
mally closed contacts) on terminal block 3 (sizes 034-048) or
terminal block 4 (sizes 054-104). See Fig. 24. Note that a field-
supplied power source is required.
There are no required 115-volt field wiring connections,
therefore no provisions have been made in the unit for running
115-volt wiring. If any of the field-installed options requiring
115-volt connections are desired, the unit must be modified in
the field for 115-volt wiring.
NIGHT SETBACK THERMOSTAT — Wire field-supplied
thermostat (suitable for 24-v circuit) between terminals 1 and 2
on terminal block 3 (sizes 034-048) or terminal block 4
(sizes 054-104). This thermostat is used to bypass the time-
clock occupied/unoccupied switch and is used to operate unit
during unoccupied times at more economical temperatures.
(See Fig. 23.)
SPACE TEMPERATURE RESET ACCESSORY (50DJ900021)
— Consists of a thermistor (T10) and a reset board with a potenti-
ometer (P7) that is used to set space temperature at which reset
starts. Mount reset board in unit control box or other convenient
place. Wire thermistor in series with P7 and connect to terminals
12 and 15 on terminal block 3 (sizes 034-048) or terminal block 4
(sizes 054-104) in unit control box. If there is a long run to condi-
tioned space, it is necessary to splice additional wire to thermistor.
The reset board has 2 pressure connectors for field wiring. (See
Fig. 25.)
Space Temperature Reset
INSTALLATION — Install the accessory temperature reset
package in accordance with instructions provided with the
accessory kit.
Mount the reset board in the unit control box (or other suit-
able location) per instructions.
Locate the thermistor T10 in a suitable location in the occu-
pied space per instructions.
Wire T10 to the reset board and to the unit control terminal
block per Fig. 25. Wire the other terminal on the reset board to
the unit control terminal block per Fig. 25.
If multiple sensors are required to average the space temper-
ature, see Fig. 26. Use only Carrier Part Number HH79NZ014
sensor, in arrangements of 4 or 9 sensors, with total wiring not
to exceed 1000 ft.
To enable reset function, change DIP (dual in-line package)
switch 2 to position ON. (Disconnect control power before
changing DIP switch positions; reconnect power after all
changes have been made.)
CONFIGURATION — Set points for reset operation are
established at potentiometers P7 and P3 (on the reset board).
Potentiometer P7
— Reset temperature set point (temperature
at which reset function will start). Maximum of 80 F, mini-
mum 0° F. Set below normal room cooling set point level to
sense overcooling in the occupied space.
NOTE: It is difficult to accurately set the P7 potentiometer to
the desired set point. Use the procedure below.
Proper setting of the P7 potentiometer may be made on a re-
sistance basis. The microprocessor initiates reset when it de-
tects a resistance of the thermistor plus the potentiometer of
13,084 ohm. The potentiometer set point may be calculated us-
ing the following formula:
P7
R
= 13,084 – T10
R
Where:
P7
R
= the desired set point of the P7 potentiometer in ohms
T10
R
= the resistance of the T10 thermistor for the desired
set point