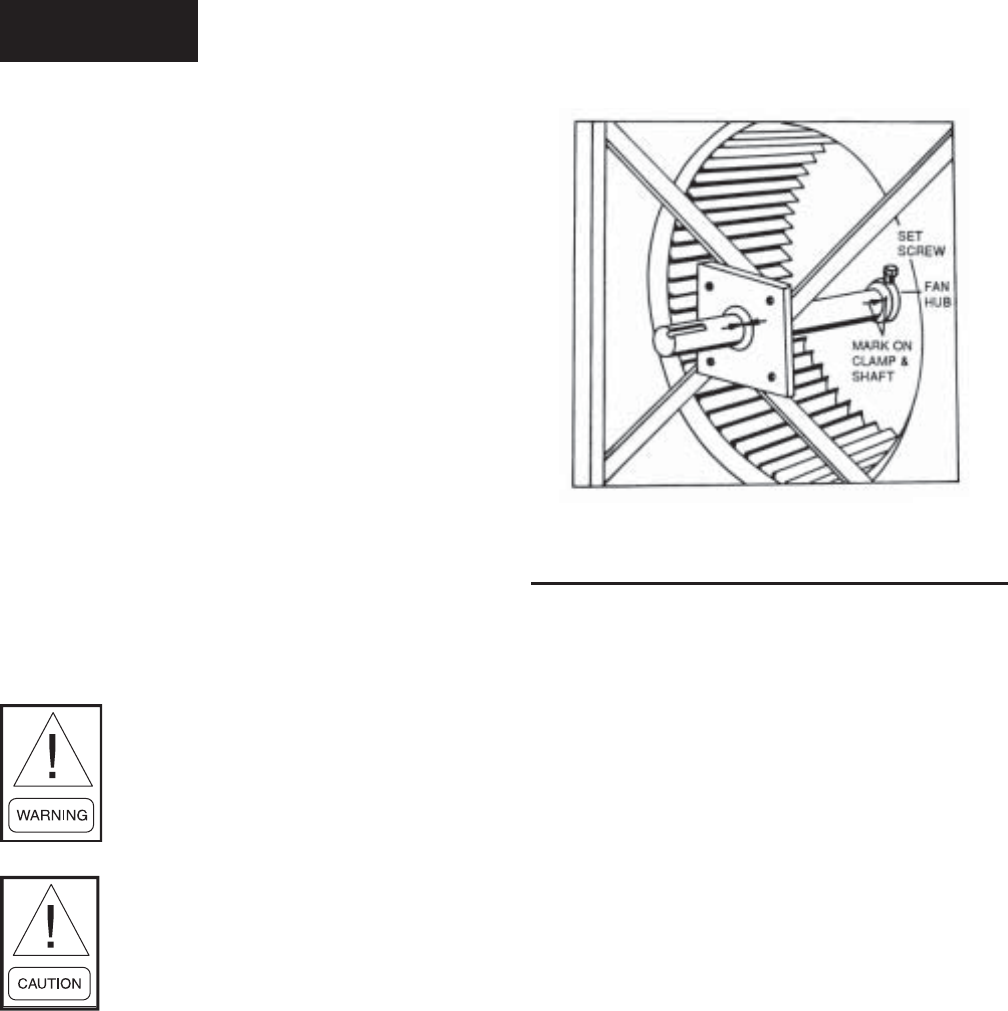
58
Maintenance
JOHNSON CONTROLS
FORM 100.50-NOM6 (1207)
Filter Drier Replacement
The fi lter/drier should be replaced any time work is
per formed on the refrigerant circuit. The rooftop unit
comes with sealed type (non-replaceable) cores as
stan dard. If the unit is not equipped with the op tion al
valve package (suction, discharge, & liquid line valves),
the refrigerant will need to be recovered with a recovery
ma chine to replace the fi lter/drier.
If the unit is equipped with a valve pack age, the unit
can be pumped down by clos ing the liquid line ball
valve (prior to the fi lter/drier) while the unit is running,
ini ti at ing a unit pump-down. The unit will shut off when
the mechanical low-pres sure switch opens. When the
unit shuts down, close the ball valve located after the
fi lter/drier and remove power from the unit to prevent
the unit from running. Once the fi lter/drier core has been
replaced, the fi lter/drier section should be evacuated via
the Schrader ac cess valve located next to the fi lter/drier
prior to open ing the ball valves and restoring the unit
to normal op er a tion.
Never shut the dis charge valve while
the unit is run ning. Doing so could
cause a rup ture in the dis charge line
or com po nents, re sult ing in death or
se ri ous injury.
Never close the suction line ball valve
with the com pres sor running. Doing
so will cause the com pres sor to pump-
down into a vac u um and dam age the
com pres sor due to in ter nal arcing.
Forward Curved Fans
The forward curved fan wheel must be re moved through
the fan discharge open ing. The lo ca tion of other clamps,
fan wheel, and shaft must be marked so each of these
com po nents can be re as sem bled in the same location
- see Figure 4-4. This will preserve the bal ance of the
ro tat ing as sem bly. Pro ceed with the fol low ing steps:
1. Disconnect all duct work or guards at tached to the
blower housing to permit unobstructed ac cess.
2. Remove the cut off plate at tached at the dis charge
or blast area of the blower housing.
3. Thoroughly clean the shaft of all grease and rust
inhibitor. Be careful not to con tam i nate the bear ing
grease. Use emery cloth to re move all rust or the
wheel may become “locked” to the shaft.
4. Loosen and remove set screws on both bear ing
lock ing collars. In spect and, if necessary, re-
place.
5. Loosen and remove set screws from both sides of
the wheel hub. Inspect and, if necessary, re place.
6. Using a rubber mallet or brass bar, slow ly drive
the shaft in one direction until the set screw marks
on the shaft are fully ex posed. File the marks
com plete ly smooth. Drive the shaft in the opposite
di rec tion and fi le smooth the set screw marks. Con-
tin ue to clean the shaft of all dirt and residuals.
7. To remove the key, use a rub ber mal let or brass bar
to drive the shaft and wheel in one di rec tion. Drive
the key in the op po site di rec tion us ing a nail set or
small er size key stock until the key is com plete ly
free of the wheel. Be sure that key does not get
bent by al low ing it to ride up the key way edge.
The slightest bend will prevent quick as sem bly.
Should this occur, re place the key stock.
8. Remove the shaft, supporting the weight of the
wheel, particularly for larger di am e ter wheels. Do
not al low the weight of the shaft to be sup port ed
by one bearing as you dis as sem ble.
9. Remove the wheel through the dis charge or outlet
area of the blower hous ing.
10. Reassemble in reverse order, cen ter ing the wheel
between the edges of the inlet ven turi. If bearings
were removed or re placed, be sure to re use any
shim stock found be tween the mount ing support/
plate and bearing hous ings.
11. Torque all hardware.
FIG. 4-4 – EXAMPLE OF FC FAN SHAFT/WHEEL
MARKING
LD06355
LD06355