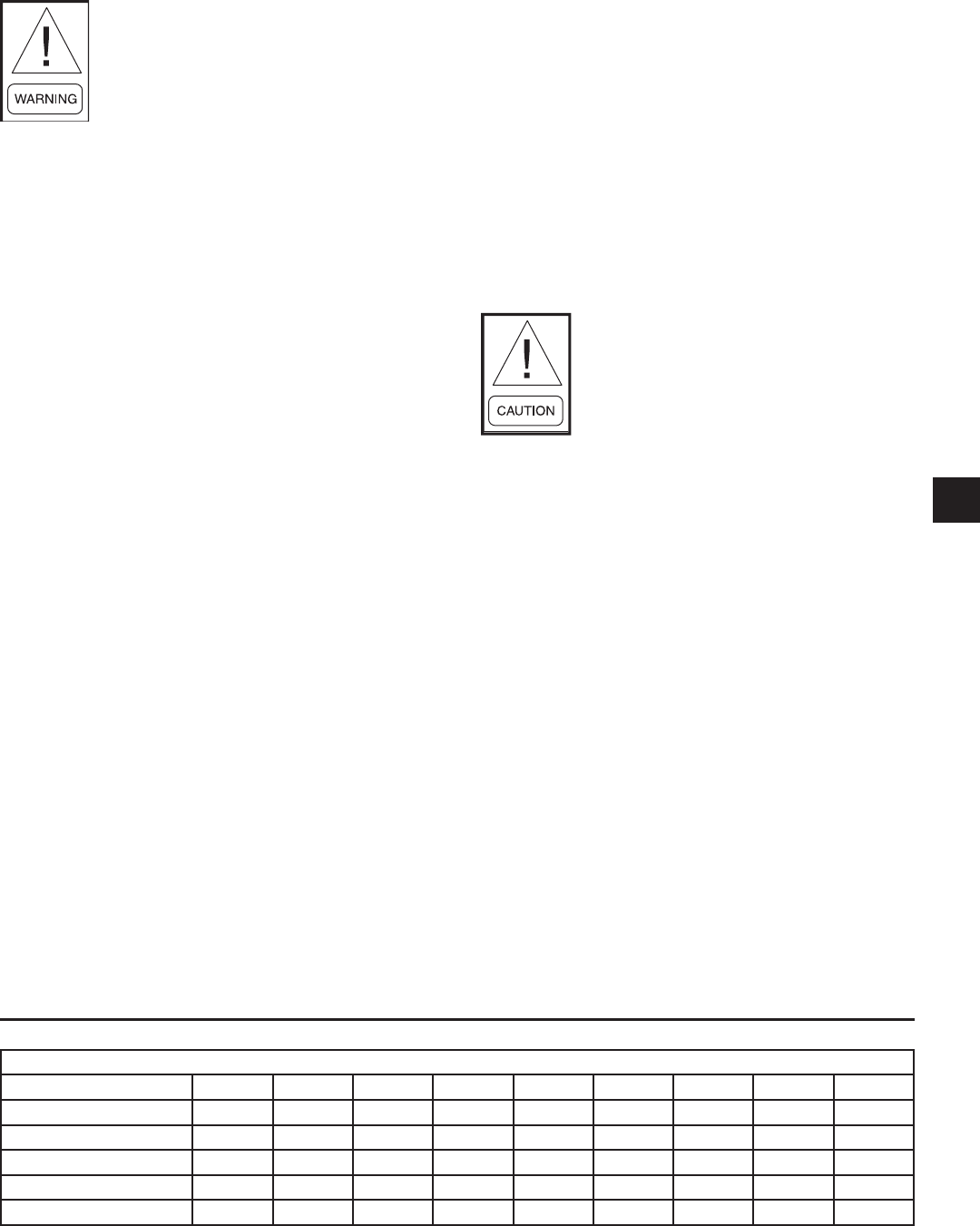
55
4
JOHNSON CONTROLS
FORM 100.50-NOM6 (1207)
SECTION 4 – MAINTENANCE
Make sure power is removed from
the unit before performing the main-
tenance items contained in this sec-
tion.
GENERAL
A planned program of regularly sched uled main te nance
will return div i dends by avert ing possible costly and
un ex pect ed pe ri ods of down time. It is the responsibility
of the owner to pro vide the necessary main te nance
for the air handling units and coils. If a system failure
oc curs due to improper main te nance during the warranty
pe ri od, JOHNSON CONTROLS will not be liable
for costs in curred to return the unit to sat is fac to ry
operation.
PERIODIC MAINTENANCE – MONTHLY
Filters
Check the cleanliness of the fi lters and replace or clean
as required.
Linkages
Examine the damper and operator link ag es to in sure
that each is free and op er at ing smoothly.
Compressors
Oil Level Check: The oil level can only be tested when
the com pres sor is running in stabilized con di tions, to
ensure that there is no liquid refrigerant in the lower
shell of the com pres sor. When the compressor is run ning
in stabilized con di tions, the oil level must be be tween
1/4 and 3/4 in the oil sight glass. Note: at shut down,
the oil level can fall to the bot tom limit of the oil sight
glass.
Oil Analysis: Use York Type “T” POE oil (clear) for
units charged with R-410A refrigerant. The type of
refrigerant and amount per system is listed on the unit
rating plate. A change in the oil color or odor may
be an indication of contaminates in the refrigeration
system. If this occurs, an oil sample should be taken
and analyzed. If contaminations are present, the system
must be cleaned to prevent compressor failure. This can
be accomplished through the installation of oversized
suction and liquid line driers. The driers may have to be
changed several times to clean up the system depending
on the degree of contamination.
Never use the scroll compressor
to pump the re frig er ant system down
into a vac u um. Doing so will cause
in ter nal arcing of the compressor
motor, which will result in failure of
com pres sor.
Fan Bearing Lubrication
Add grease slow ly with shaft ro tat ing un til a slight
bead forms at the seals. If nec es sary, re-lubricate while
bear ing is stationary. The fan data plate (at tached to
the fan scroll) lists the type of grease that must be used
for lu bri cat ing the bearings. Refer to Table 4-1 for
lu bri cat ing schedule.
Re-lubrication is generally accompanied by a tem po rary
rise in operating tem per a ture. Excess grease will be
purged at seals.
Recommended Lubricant for Fan Bearings
A Lithium / Petroleum base grease con form ing to an
NLGI Grade II consistency is nor mal ly used. Lu bri cant
must be free of any chem i cal im pu ri ties such as free
acid or free alkali, dust, rust, metal particles or abrasive.
This light viscosity, low torque grease is rust inhibited
and water resistant, has a tem per a ture range of -30°F
to +200°F with intermittent highs of +250°F. Lubricate
bearings as re quired by the se ver i ty of required duty.
TABLE 4-1 – FAN BEARING – LUBRICATION INTERVALS
RELUBRICATION SCHEDULE (MONTHS) BALL BEARING PILLOW BLOCKS
SPEED (RPM) 500 1000 1500 2000 2500 3000 3500 4000 4500
SHAFT DIA
1/2” thru 1-11/16” 665332221
1-15/16” thru 2-7/16” 6542211/21/41/4
2-11/16” thru 2-15/16” 543211/21/2
3-7/16” thru 3-15/16” 43211/21/2