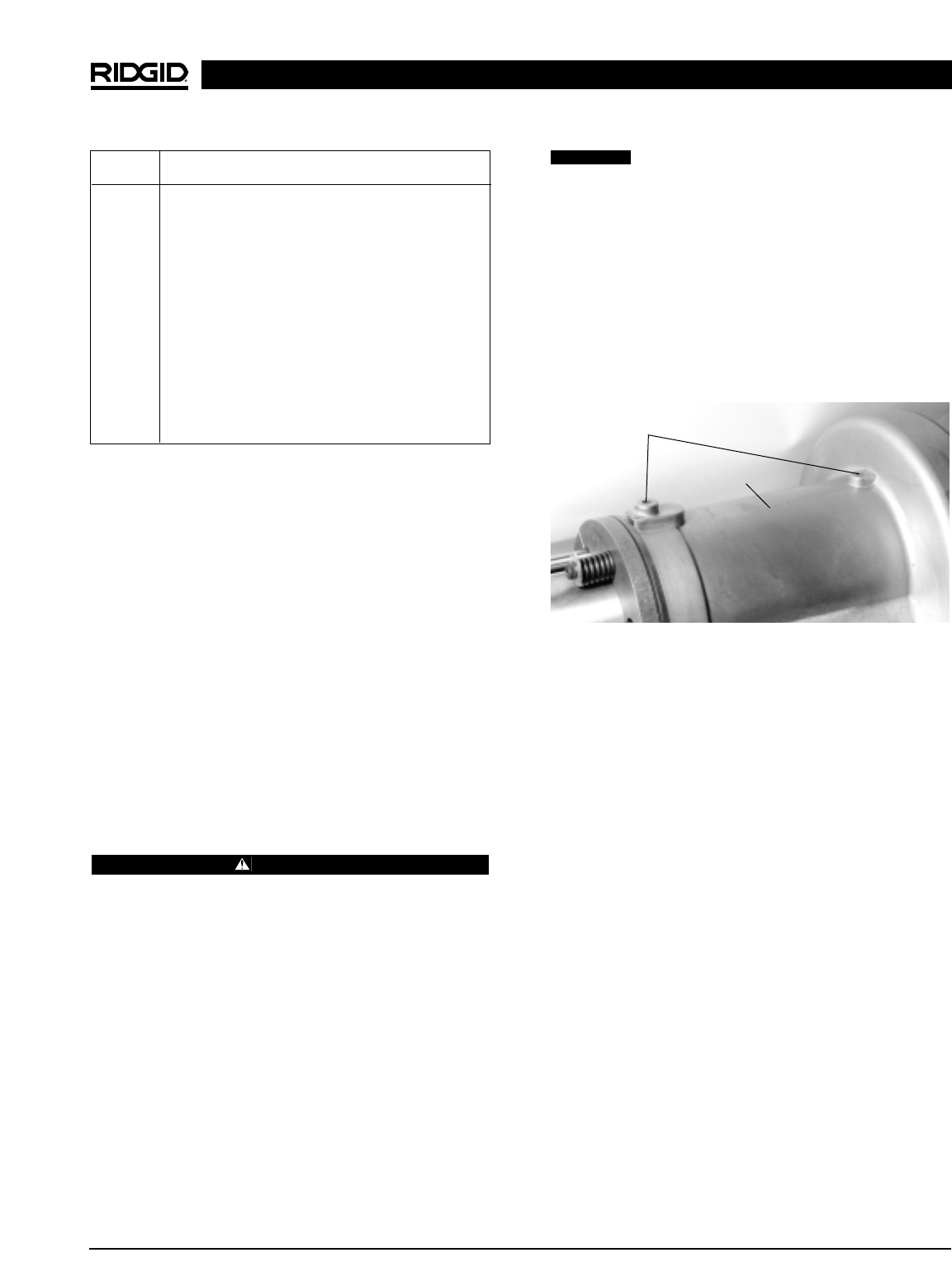
Ridge Tool Company
19
Pipe Support Stands
No. 819 Nipple Chuck (Right Hand Only)
No. 839 Adapter Kit
Pipe Adapters..............
1
/
8
″ through 1
1
/
2
″
Stud Adapters..............
1
/
4
″ through 2″ UNC
1
/
4
″ through 1
1
/
2
″ UNF
Accessories For Threading
By Close-Coupled Method
No. 241 Carriage Mount Kit
No. 141 Geared Threader….for threading
2
1
/
2
″ - 4″ pipe
Pipe Support Stand
NOTE! See Ridge Tool catalog for complete list of pipe
supports, thread cutting oil and dies.
Maintenance Instructions
WARNING
Make sure machine is unplugged from power
source before performing maintenance or mak-
ing any adjustment.
Oil System Maintenance
Periodic cleaning of oil reservoir and filter screens will
promote proper operation of machine. Replace cutting oil
when it becomes dirty or contaminated.
1. Remove and clean top chip pan screen.
2. Remove and clean secondary screen from chip pan.
3. Remove drain plug and drain cutting oil.
4. Clean oil filter screen and remove sludge built up in oil
reservoir.
DO NOT operate machine with oil filter in
bottom of oil reservoir removed. This could cause chips to
clog oil line and/or damage the oil pump.
NOTE! RIDGID Thread Cutting Oil produces high qual-
ity threads and maximizes die life. For informa-
tion concerning its use and handling, refer to the
labels on the oil containers. Disposal of the oil
should be in accordance with government reg-
ulations.
Spindle Bearing Lubrication
(Figure 22)
Figure 22 – Spindle Bearing Lubrication
Main spindle bearing lubrication ports are located on top
and at each end of the spindle housing.
Bearings are oil impregnated when manufactured and
will serve to lubricate spindle until scheduled mainte-
nance is performed.
Lubrication with 10 drops of SAE 20 Weight Nondetergent
oil is recommended every six months (more often under
heavy machine usage).
Front Jaw Insert and Centering Finger
Replacement
1. Run machine in the OPEN position to open jaws.
2. With machine OFF and unplugged, remove front
cover.
3. Loosen screw that holds jaw insert and centering
finger in place. This should allow jaw insert to separate
from jaw assembly. (Figures 23A & B)
4. On a workbench, drive out top pins holding centering
finger in place and install new centering finger.
NOTE! When driving pin out on workbench, do not bend
centering finger.
1822-I Pipe and Bolt Threading Machine
Model
No. Description
819 Nipple Chuck 1/2″ - 2″ NPT
819 Nipple Chuck 1/2″ - 2″ BSPT
839 Adapter Kit for No. 819 Nipple Chuck
821 Blade Type Cutter
822 Adapter Kit for No. 821 Blade Cutter
141 4″ Geared Threader NPT
141 4″ Geared Threader BSPT
241 Carriage-Mount Kit for No. 141 Threader
1460 Oil Pan Cover Kit
E-863 L.H./R.H. Reamer Cone
364 Wheel Type Cutter
Conversion Kit for Plastic Coated Pipe
Grooving Tool
E-1050 Saran Tool for 821
D471 45° Bevel, Cut-Off Tool for 821
344 Reamer
Gear Grease (1224 & 1822)
CAUTION
Spindle Housing
Bearing Lubrication
Ports