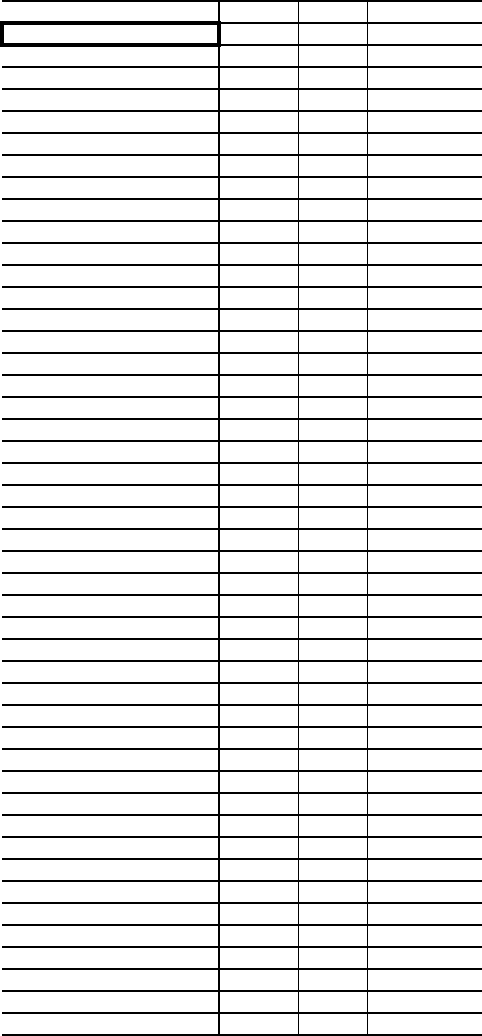
34
Table 14 — Service Configuration Selection
STAGED COOLING — The staging function is used for DX
cooling (1 or 2 stages). The staging function uses the cooling
submaster reference from the PID and compares the value to
the supply air temperature to calculate the required number of
output stages to energize.
Time Guard delays are provided to allow for up to 2 stages
of compression. Also, a DX Lockout will prevent operation
of the DX cooling if the outdoor air temperature is below this
value.
The cooling algorithm controls the valve or stages of DX
cooling to prevent the space temperature from exceeding the
current cooling set point (which includes any calculated offset
value from a T56 sensor slide bar during occupied periods).
Also, the cooling is controlled so that the supply air tempera-
ture does not fall below 50 F when cooling is active.
If number of stages is set to 1, then the SAT CMP2 LOCK-
OUT TEMP will be used as the low supply air set point.
Number of Stages: Range: 1 to 3
Default Value: 2
The Time Guards must be set to Enable for output to a
compressor, and set to Disable for output to a valve or
compressor unloader.
Stage 1
Time Guard: Range: Disable/Enable
Default Value: Enable
Stage 2
Time Guard: Range: Disable/Enable
Default Value: Enable
Stage 3
Time Guard: Range: Disable/Enable
Default Value: Disable
HEATING PID — The PremierLink™ controller determines
if a heating demand exists in the space. The controller reads the
space temperature sensor and compares the temperature to the
current low set point (including any calculated offset value
from a T56 or T57 sensor) during occupied periods. If it is
below the set point, and heating is configured and available, it
then calculates the required supply air temperature to satisfy
the given conditions. The calculated value (heating submaster
reference) is compared to the actual supply-air temperature and
the output is then adjusted to satisfy conditions by using a
Proportional/Integral/Derivative (PID) loop.
The Heating PID includes the following set points: Propor-
tional Gain, Integral Gain, Derivative Gain, and Starting Value.
Proportional Gain: Range: –100.0 to 100.0
Default Value: 6.0
Integral Gain: Range: –5.0 to 5.0
Default Value: 3.0
Derivative Gain: Range: –20.0 to 20.0
Default Value: 5.0
Starting Value: Units: Degrees F
Range: 40.0 to 120.0
Default Value: 75.0
STAGED HEATING — The Staged Heating function is used
for two-position valves or for electric heat (1 or 2 stages). The
staging function uses the heating submaster reference value
from the PID and compares it to the supply air temperature to
calculate the required number of output stages to energize.
Number of Stages: Range: 1 to 3
Default Value: 2
Stage 1
Time Guard: Range: Disable/Enable
Default Value: Enable
Stage 2
Time Guard: Range: Disable/Enable
Default Value: Enable
Stage 3
Time Guard: Range: Disable/Enable
Default Value: Enable
IAQ PID — The proportional gain affects the response of PID
calculations for staged control. The gain is also used for two-
position control to establish the hysteresis between on and off.
A larger gain speeds response time or reduces the hysteresis,
while a smaller gain requires a larger error to generate the same
response to changes in Indoor Air Quality. Enter the desired
proportional gain for the Indoor Air Quality control algorithm.
DESCRIPTION VALUE UNITS NAME
Cooling PID
Proportional Gain
6.0
KP
Integral Gain
3.0
KI
Derivative Gain
5.0
KD
Starting Value
70.0
dF STARTVAL
Staged Cooling
Total Number of Stages
2
STAGES
Stage 1 Time Guard
Enable
TG1
Stage 2 Time Guard
Enable
TG2
Stage 3 Time Guard
Disable
TG3
Heating PID
Proportional Gain
6.0
KP
Integral Gain
3.0
KI
Derivative Gain
5.0
KD
Starting Value
75.0
dF STARTVAL
Staged Heating
Total Number of Stages
2
STAGES
Stage 1 Time Guard
Enable
TG1
Stage 2 Time Guard
Enable
TG2
Stage 3 Time Guard
Enable
TG3
IAQ PID
Proportional Gain
0.1
KP
Integral Gain
0.0
KI
Derivative Gain
0.0
KD
Starting Value
0.0
%STARTVAL
Economizer PID
Proportional Gain
-4.0
KP
Integral Gain
-2.0
KI
Derivative Gain
-3.0
KD
Starting Value
70.0
dF STARTVAL
Submaster Gain Limit
-5.5
ESG
Submaster Center Value
60
%CTRVAL
Damper Movement Band
0
% ECONBAND
OAT Temp Band
25
^F TEMPBAND
Minimum Damper Position
20
%MDP
Low Temp MDP Override
100
%LOWMDP
DX Cooling Lockout
On
DXCTLO
DX Cooling Lockout Temp
45.0
dF DXLOCK
SAT CMP1 Lockout Temp
55.0
dF SATL01
SAT CMP2 Lockout Temp
50.0
dF SATL02
Time Guard Override
Off
TGO
Continuous Power Exhaust
Disable
MODPE
Supply Fan Status Enable
Disable
SFSENABL
Max Offset Adjustment
2.0
^F LIMT
Space Temp Trim
0.0
^F RATTRIM
Supply Air Temp Trim
0.0
^F SATTRIM