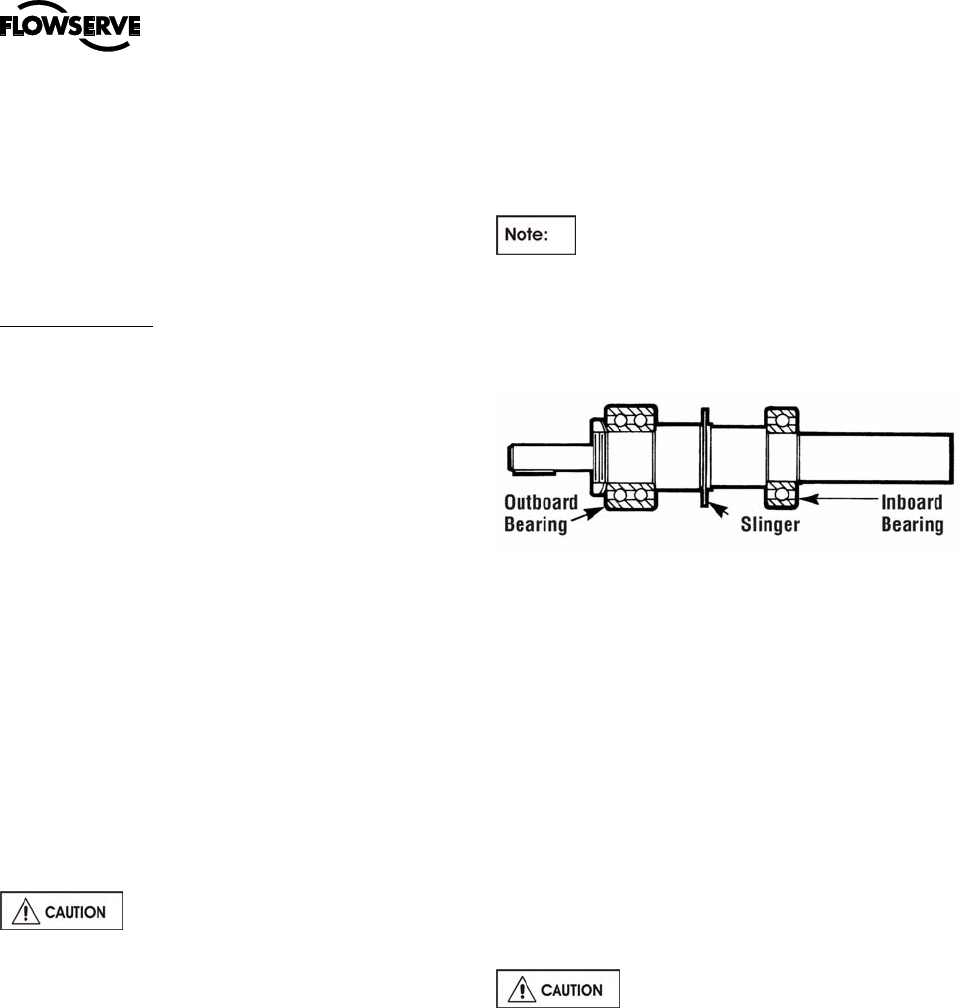
MARK 3 USER INSTRUCTIONS ENGLISH 71569102 08-06
Page 50 of 68 flowserve.com
Many companies today are using laser alignment
which is a more sophisticated and accurate
technique. With this method a laser and sensor
measure misalignment. This is fed to a computer
with a graphic display that shows the required
adjustment for each of the motor feet.
See section 4.8 for recommended final shaft
alignment limits.
Vibration analysis
Vibration analysis is a type of condition monitoring
where a pump’s vibration “signature” is monitored on
a regular, periodic basis. The primary goal of
vibration analysis is extension on MTBPM. By using
this tool Flowserve can often determine not only the
existence of a problem before it becomes serious, but
also the root cause and possible solution.
Modern vibration analysis equipment not only detects
if a vibration problem exists, but can also suggest the
cause of the problem. On a centrifugal pump, these
causes can include the following: unbalance,
misalignment, defective bearings, resonance,
hydraulic forces, cavitation and recirculation. Once
identified, the problem can be corrected, leading to
increased MTBPM for the pump.
Flowserve does not make vibration analysis
equipment, however Flowserve strongly urges
customers to work with an equipment supplier or
consultant to establish an on-going vibration analysis
program. See note 3 under figure 6-19 regarding
acceptance criteria.
6.9 Assembly of pump and seal
It is important that all pipe threads be
sealed properly. PTFE tape provides a very reliable
seal over a wide range of fluids, but it has a serious
shortcoming if not installed properly. If, during
application to the threads, the tape is wrapped over the
end of the male thread, strings of the tape will be formed
when threaded into the female fitting. These strings can
then tear away and lodge in the piping system.
If this occurs in the seal flush system, small orifices can
become blocked effectively shutting off flow. For this
reason, Flowserve does not recommend the use of
PTFE tape as a thread sealant.
Flowserve has investigated and tested alternate
sealants and has identified two that provide an
effective seal, have the same chemical resistance as
the tape, and will not plug flush systems. These are
La-co Slic-Tite and Bakerseal. Both products contain
finely ground PTFE particles in an oil based carrier.
They are supplied in a paste form which is brushed
onto the male pipe threads. Flowserve recommends
using one of these paste sealants.
Full thread length engagement is required for all
fasteners.
Refer to figure 6-2 for recommended bolt
torques.
6.9.1 Power end assembly
The Mark 3A design has an optional oil slinger. If the
slinger was removed during disassembly, install a
new slinger [2541]. (See figure 6-22.)
Figure 6-22
6.9.1.1 Bearing installation
Mounting of bearings on shafts must be done in a clean
environment. Bearing and power end life can be
drastically reduced if even very small foreign particles
work their way into the bearings. Wear clean gloves.
Bearings should be removed from their protective
packaging only immediately before assembly to limit
exposure to possible contamination. After removing
the packaging they should only come in contact with
clean hands, fixtures, tools and work surfaces.
The chart shown in figure 6-23 gives the SKF part
numbers for bearings in Flowserve Mark 3 pumps. Note
that the term “inboard bearing” refers to the bearing
nearest to the casing. “Outboard bearing” refers to the
bearing nearest to the motor. (See figure 6-22.)
Both bearings have a slight interference
fit which requires that they be pressed on the shaft with
an arbor or hydraulic press. Figure 6-20 identifies the
bearing fits. Even force should be applied to only the
inner race. Never press on the outer race, as the force
will damage the balls and races.
An alternate method of installing bearings is to heat
the bearings to 93 °C (200 °F) by means of an oven
or induction heater. With this approach the bearing
must be quickly positioned on the shaft.
Never heat the bearings above 110 °C (230 °F). To
do so will likely cause the bearing fits to permanently
change, leading to early failure.