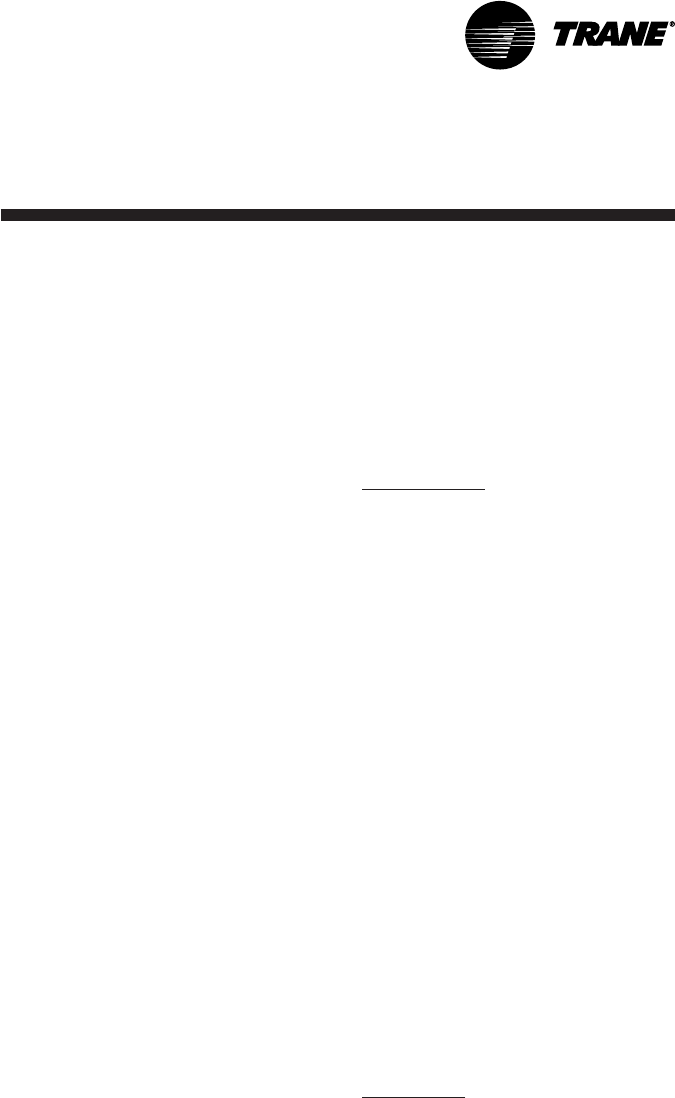
SCXG-SVX01B-EN 89
Input Devices and System
Functions
Following are basic input device and
system function descriptions used within
the UCM network on IntelliPak
®
self-
contained units. Refer to the unit wiring
diagrams for specific connections.
Water Purge
During the unoccupied mode, water-
cooled units will periodically circulate
water through the condensers and
waterside economizer if the user has
enabled the purge function at the HI.
The water purge function circulates
water to introduce fresh water-treatment
chemicals and help prevent water
stagnation. The number of hours be-
tween each periodic purge, or purge
duration, is user-defined at the HI
between 1-999 hours. If the periodic
purge timer expires while the unit is in
occupied mode, it will wait for the next
available unoccupied time before
initiating water purge. Contrary, if a
request for cooling occurs during a purge
sequence, purge will terminate and
cooling will commence.
Compressor Circuit Breakers
The compressors are protected by circuit
breakers that interrupt the compressor
power supply if the current exceeds the
breakers “must trip” value. During a
request for compressor operation, if the
compressor module (MCM or SCM)
detects a problem outside of it’s normal
parameters, it turns any operating
compressor(s) on that circuit off, locks out
all compressor operation for that circuit,
and initiates a manual reset diagnostic.
Compressor Motor Winding Thermostats
A thermostat is embedded in the motor
windings of each compressor. Each
thermostat opens if the motor windings
exceed approximately 221 F. The
thermostat resets automatically when
the winding temperature decreases to
approximately 181 F. Rapid cycling, loss
of charge, abnormally high suction
temperatures, or the compressor running
backwards could cause the thermostat to
open. During a request for compressor
operation, if the compressor module
detects a problem outside of it's normal
parameters, it turns any operating
compressor(s) on that circuit off, locks out
all compressor operation for that circuit,
and initiates a manual reset diagnostic.
Low Pressure Control
Low pressure (LP) control uses a binary
input device. LP cutouts are mounted on
the suction lines near the compressors.
The LP control contacts close when the
suction pressure exceeds 27 ± 4 psig. If
the LP control is open when a compres-
sor starts, none of the compressors on
that circuit will operate. They are locked
out and a manual reset diagnostic
initiates.
The LP cutouts open if the suction
pressure approaches 7 ± 4 psig. If the LP
cutout opens after a compressor starts,
all compressors operating on that circuit
will turn off immediately and will remain
off for a minimum of three minutes.
If the LP cutout trips four consecutive
times during the first three minutes of
operation, the compressors on that circuit
will lock out and a manual reset diagnos-
tic initiates.
Evaporator Temperature Sensor
Frostat™
The evaporator temperature sensor is an
analog input device that monitors
refrigerant temperature inside the
evaporator coil to prevent coil freezing. It
is attached to the suction line near the
evaporator coil with circuits 1 and 2
connected to the SCM/MCM and circuits
3 and 4 connected to the WSM. The coil
frost cutout temperature is factory set at
30 F. It is adjustable at the HI from 25-35 F.
The compressors stage off as necessary
to prevent icing. After the last
compressor stages off, the compressors
restart when the evaporator
temperature rises 10 F above the coil
frost cutout temperature and the
minimum three minute “off” time
elapses.
Saturated Condenser Temperature
Sensors
The saturated condenser temperature
sensors are analog input devices used on
all units. They are mounted inside a
temperature well located on a condenser
tube bend on air-cooled units, and in the
condenser shell on water-cooled units.
The sensors monitor the saturated
refrigerant temperature inside the
condenser coil and are connected to the
SCM/MCM for circuits 1 and 2 (air or
water cooled), and WSM for circuits 3
and 4 (only water-cooled).
Head Pressure Control
Head pressure control is accomplished
using two saturated refrigerant
temperature sensors on air-cooled units
and up to four sensors on water-cooled
units.
•
Air-cooled units: During a request for
compressor operation when the con-
densing temperature rises above the
lower limit of the control band, the
compressor module (SCM/MCM)
sequences condenser fans on. If the
operating fans cannot bring the condens-
ing temperature to within the control
band, more fans turn on. As the satu-
rated condensing temperature ap-
proaches the lower limit of the control
band, fans sequence off. The minimum
on/off time for condenser fan staging is
5.2 seconds. If the system is operating at
a given fan stage below 100% for 30
minutes he saturated condensing
temperature is above the efficiency
check point setting, a fan stage will be
added. If the saturated condensing
temperature falls below the efficiency
check point setting, fan control remains at
the present operating stage. If the fan
stage cycles four times within a 10
minute period, the lower limit tempera-
ture is redefined as being equal to the
lower limit minus the temporary low limit
suppression setting. The unit will utilize
this new low limit temperature for one
hour to reduce condenser fan short
cycling.
•
Water-cooled: Units without WSE, the
condenser valve modulates to maintain
an average saturated condenser
temperature. Units with WSE, if econo-
mizing and mechanical cooling is neces-
sary the economize valve will sacrifice
free cooling and modulate to maintain
condensing saturated temperature. If not
economizing, the condenser valve will
modulate to maintain condensing
saturated temperature.
Water-cooled units without head pres-
sure control will lock out mechanical
cooling at entering condenser water
temperatures below 54 F. Mechanical
cooling will resume when the entering
Owner
General
Information