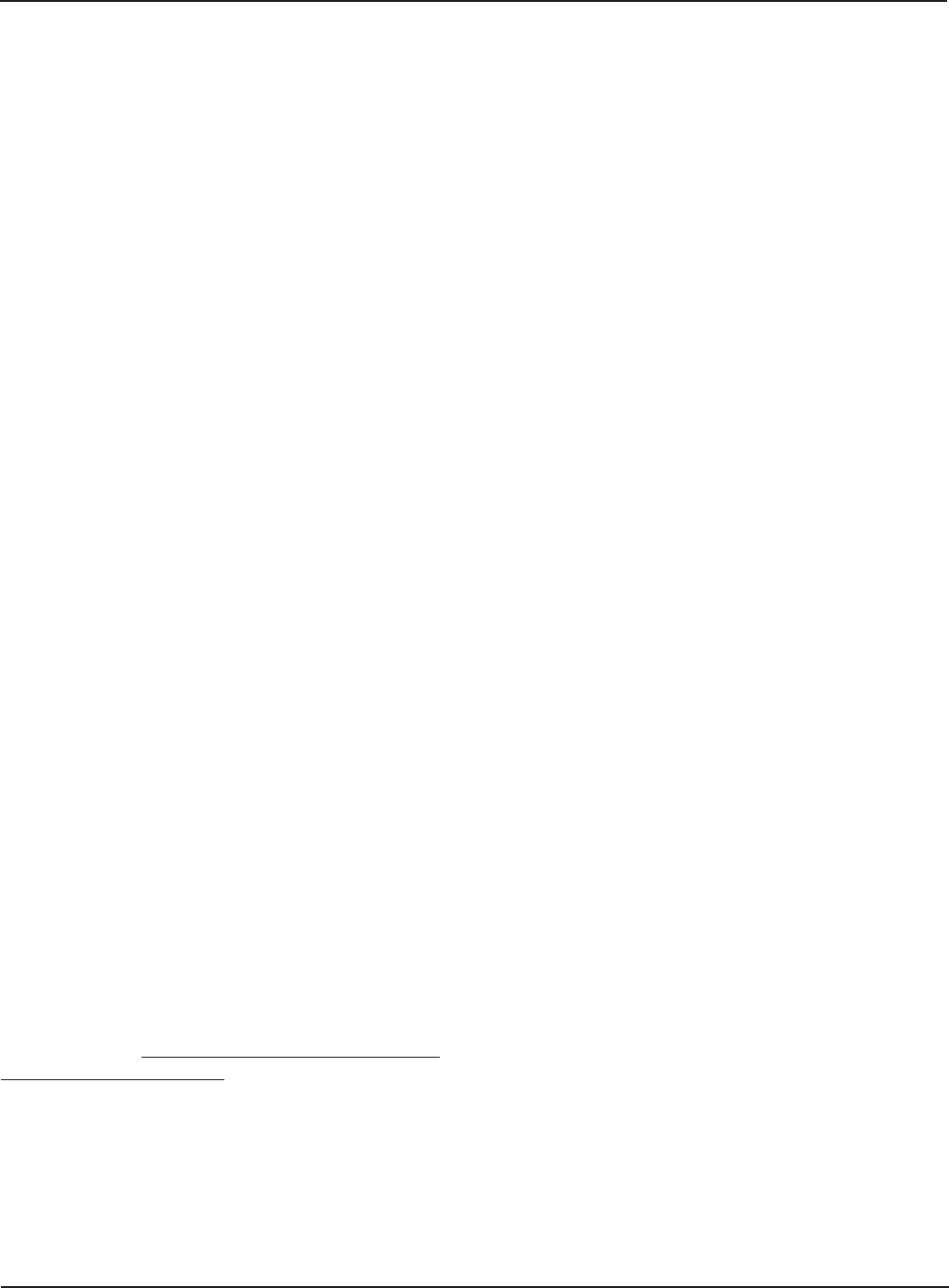
Manual 2100-549G
Page 31 of 59
START UP
DESCRIPTION OF STANDARD
EQUIPMENT
Solid State Electronic Heat Pump Control
Provides efficient 30, 60 or 90-minute defrost cycle. A
thermistor sensor and speed up terminal for service
along with a 8-minute defrost override are standard on
the electronic heat pump control. By default, the I-TEC
are factory shipped on the 90-minute defrost cycle.
High / Low Pressure Switch
Provides refrigerant circuit high pressure and loss of
charge protection. Includes lockout circuit built into
heat pump control that is resettable from room
thermostat.
Five Minute Compressor Time Delay
Provides short cycle protection for the compressor
which extends compressor life. Built into the electronic
heat pump control as standard.
Dual Sensor Condensate Overflow
Senses and provides system shut down if draining issue
causes water level to rise in either drain pan.
Low Ambient Control
The low ambient control permits cooling operation
down to 0°F outdoor ambient.
IMPORTANT INSTALLER NOTE
For improved start-up performance, wash the indoor coil
with a dishwasher detergent.
PHASE MONITOR
All units with three phase scroll compressors are
equipped with a 3 phase line monitor to prevent
compressor damage due to phase reversal.
The phase monitor in this unit is equipped with two
LEDs. If the Y signal is present at the phase monitor
and phases are correct the green LED will light and the
compressor contactor is allowed to energize.
If phases are reversed, the red fault LED will be lit and
compressor operation is inhibited.
If a fault condition occurs, reverse two of the supply
leads to the unit. Do not reverse any of the unit factory
wires as damage may occur.
THREE PHASE SCROLL COMPRESSOR
START UP INFORMATION
Scroll compressors, like several other types of
compressors, will only compress in one rotational
direction. Direction of rotation is not an issue with
single phase compressors since they will always start
and run in the proper direction.
However, three phase compressors will rotate in either
direction depending upon phasing of the power. Since
there is a 50-50 chance of connecting power in such a
way as to cause rotation in the reverse direction,
verification of proper rotation must be made.
Verification of proper rotation direction is made by
observing that suction pressure drops and discharge
pressure rises when the compressor is energized.
Reverse rotation also results in an elevated sound level
over that with correct rotation, as well as, substantially
reduced current draw compared to tabulated values.
Verification of proper rotation must be made at the time
the equipment is put into service. If improper rotation
is corrected at this time there will be no negative impact
on the durability of the compressor. However, reverse
operation for even one hour may have a negative
impact on the bearing due to oil pump out.
All three phase scroll compressors used in the
I-TEC
series are wired identically internally. As a result, once the
correct phasing is determined for a specific system or
installation, connecting properly phased power leads to the
same Fusite terminal should maintain proper rotation
direction. The direction of rotation of the motor may be
changed by reversing any two line connections to the unit.
SERVICE HINTS
1.
Caution user to maintain clean air filters at all
times. Also, not to needlessly close off supply air
registers. This may reduce airflow through the
system, which shortens equipment service life as
well as increasing operating costs and noise levels.
2.
Switching to heating cycle at 75°F or higher outside
temperature may cause a nuisance trip of the remote
reset high pressure switch. Turn thermostat off,
then on to reset the high pressure switch.
3.
The heat pump wall thermostats perform multiple
functions. Be sure that all function switches are
correctly set for the desired operating mode before
trying to diagnose any reported service problems.
4. Check all power fuses or circuit breakers to be
sure they are the correct rating.
5. Periodic cleaning of the outdoor coils to permit full
and unrestricted airflow circulation is essential.
6. Annual maintenance is required to make sure that
all of the systems are functioning properly.
a. Check to make sure that the drains are not
obstructed in any way.
b. Remove any debris in the condenser section of
the unit.
c. Inspect and wash outdoor coils as necessary.
7. All motors are sealed and require no oiling.