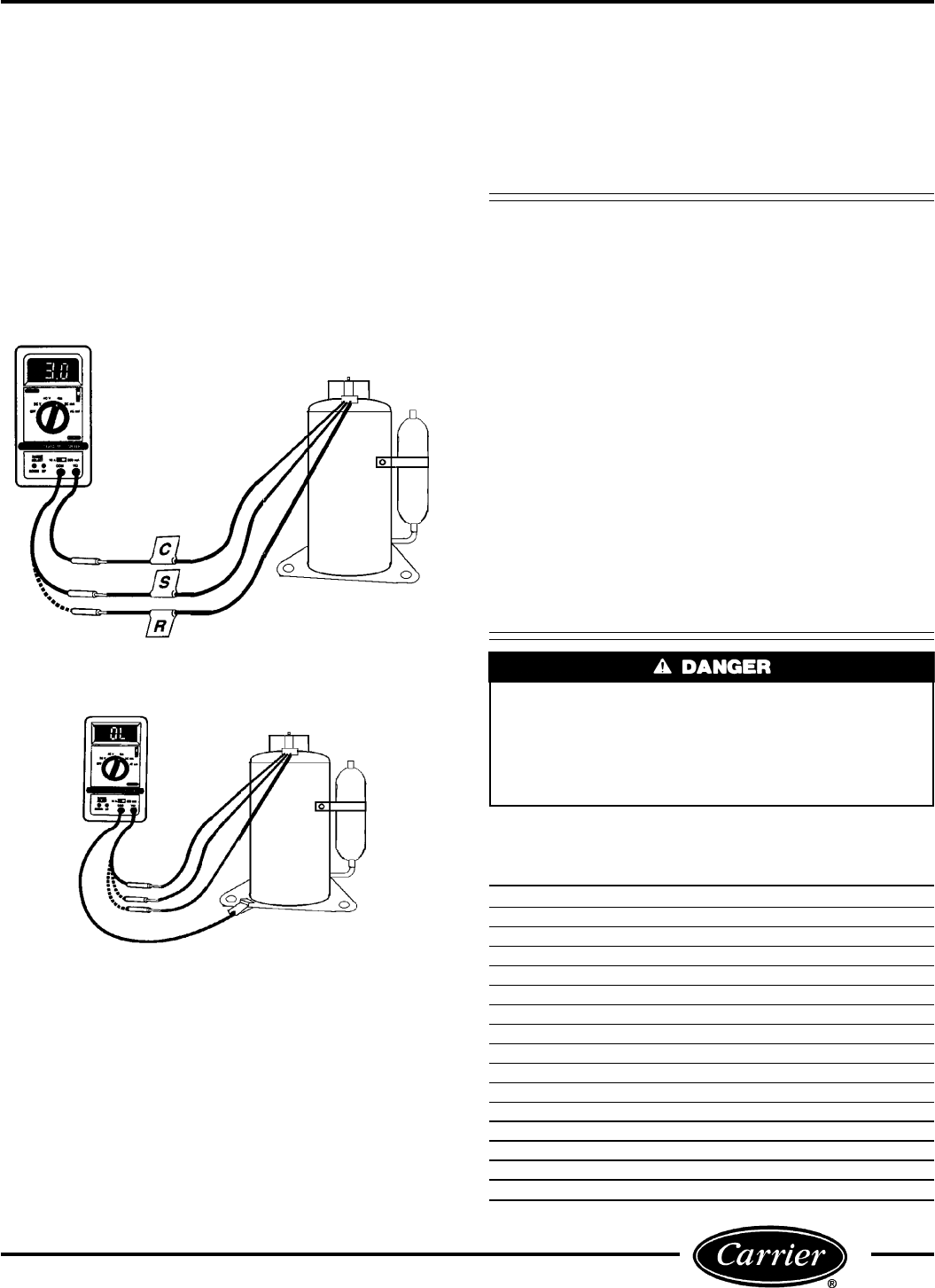
5. Next, test the resistance individually of each wire to
the shell of the compressor. The paint on the com-
pressor can prevent good contact between the probe
and the metal. The paint should be removed from
a small section of the shell of the compressor to ensure
good contact by the meter probe. The volt-ohmmeter
should be set to at least the 100X ohm level. The
measured resistance between each wire and ground
should be infinite or O.L. on the readout. If there
is measurable resistance one of the windings is likely
shorted to ground. See Figure 36.
6. A compressor that has a winding to winding short or
a winding to compressor shell short is electrically
failed and needs to be replaced. See the Compres-
sor Replacement section for details.
COMPRESSOR REPLACEMENT
Before working on the compressor, read the instructions
thoroughly and gather the necessary tools for the job.
Review all safety information on unit and in literature.
Always turn off all power to unit to avoid the possibil-
ity of electrical shock.
Consider the following safety issues before
beginning:
• New and unfamiliar tasks should be performed
under the supervision of an experienced service
technician.
• Personal protective equipment, such as work gloves
and safety glasses, should be worn.
• The floor around the work area should be clean and
free of debris.
• Make sure tools are the correct tools for the job
and that they are working properly and in good
condition.
• Never replace a blown fuse without correcting the
cause of the original failure. If thermally operated cir-
cuit breakers or overloads are tripping, make sure
the trip is not due to excessively high temperatures
or loose connections.
• When brazing suction and discharge lines, cool the
lines with a damp, clean cloth to prevent injury.
• Oil may be present in the compressor accumulator
and interconnecting tubing. Use caution when re-
moving tubing.
For compressors that are known to be dam-
aged: Remove refrigerant prior to disconnecting com-
pressor wires. Damaged hermetic compressor
terminals may become loose and eject from the com-
pressor. Wear safety glasses and keep your face
away from the area above the terminals when remov-
ing compressor wires.
Ⅲ TOOLS NEEDED — The following list includes the
recommended tools and devices for removing and replac-
ing the compressor.
1
⁄
2
-in. and
3
⁄
8
-in. Tube Benders
1
⁄
2
-in. Nut Driver
5
⁄
16
-in. Nut Driver
Flat Head Screwdriver
Piercing Valve
2 Parker Access Valves (Part No. AVUSE-5)
Pinch Off Tool
Filter Drier for 52SQ Units (Part No. Sporlan C-164S)
Filter Drier for 52SC or SE Units (Part No. KH43LG060)
Carrier TOTALTESTா Kit (Part No. TT1-001)
Totalclaimா System
Charging Cylinder or an Electronic Scale
Refrigerant-22
Tubing Cutter
Torch
Nitrogen Cylinder with Regulator
FIGURE 35 — SHORTED/OPEN WINDINGS TEST
FIGURE 36 — GROUNDED WINDINGS TEST
19