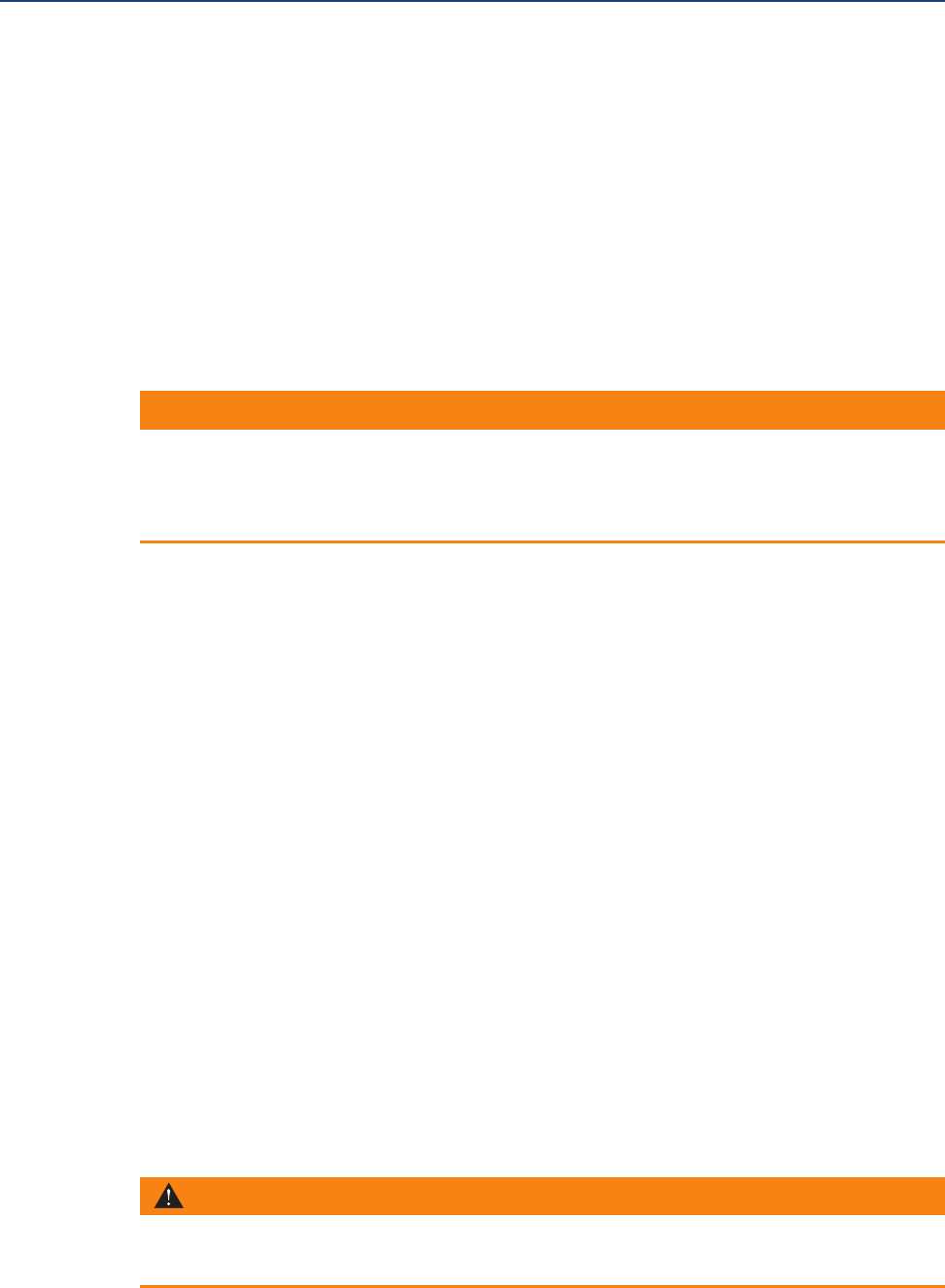
76 Troubleshooting
S
ection 4: Troubleshooting
6
888Xi Advanced Electronics Instruction Manual
December 2012 PN 51-6888Xi
B
ad Reference Side Cell Electrode - A bad reference side cell electrode can cause an elevated O
2
reading.This fault is usually indicated by a frequent "Calibration Recommended" alarm and
increasing cell impedance readings. A high cell impedance can be calibrated out, but if the
impedance continues to increase rapidly, the sensing cell must be replaced.
4.5.2 Probe passes calibration, O
2
still reads low
The diffusion element at the end of the probe is a passive filter. It plugs very slowly, since there is
no active flow being drawn across it. In applications that have a heavy particulate loading (coal or
wood fired boilers, cement and lime kilns, catalyst regeneration, recovery boilers, etc.), this diffu-
sion element will eventually plug.
4.5.3 How do I detect a plugged diffuser?
The O
2
cell's speed of response will degrade. The O
2
trend in the control room will become
smoother.
When calibrating, the calibration gas flow rate will be noted to be lower. Never readjust this flow
upwards to correct for a plugged diffuser. Adjust this flow only when a new diffuser is installed.
Always note the time it takes for the cell to recover to the normal process value after the cal gas
is removed. As the diffuser plugs, this recovery time will get longer and longer. Use the
Calibration Record provided to record and track Calibration Response times.
The 6888Xi Advanced Electronics is available with enhanced software feature to automatically
characterize the rate of diffuser pluggage during a calibration cycle.
4.5.4 Can I calibrate a badly plugged diffuser?
It may not be possible to immediately replace a plugged diffuser while the process is on line.
One can calibrate the probe without pressurizing the cell by adjusting the calibration gas flow
rate downward before calibration. For instance, say the process is at 3%, and the first calibration
gas is 8%. Adjust the flow of cal gas downward until the reading begins to migrate from 8% to
lower values, indicating that process gases are now mixing in with the calibration gases.
Adjust the flow rate back up until this mixing is just eliminated. Calibrate at this flow rate.
Replace the diffuser at the first opportunity.
WARNING
Install all protective equipment covers and safety ground leads after troubleshooting. Failure to install
covers and ground leads could result in serious injury or death.
NOTE
It is important not to pressurize the sensing cell during calibrations by flowing excessive cal gas
against a plugged diffuser. Always use a two-stage regulator for setting calibration gas pressure.
Calibration flow rates should be set only when a new diffuser is installed. As the diffuser plugs, do
not adjust the flow rates upward.