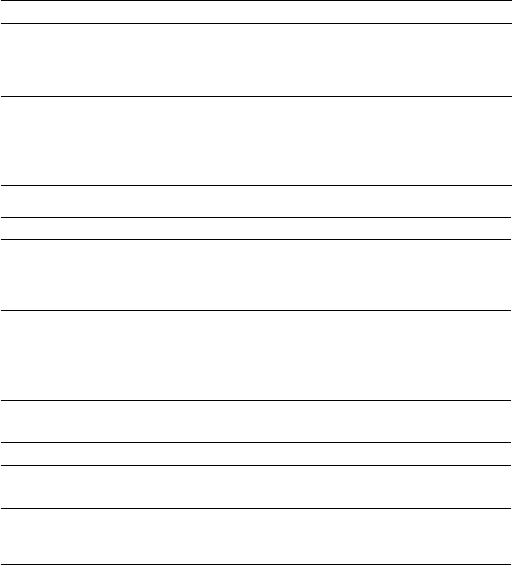
31
5.17 - High pressure load shedding function
This function does not require an additional board. It prevents
high pressure a break on a circuit by the following means:
• Preventing any capacity increase on the circuit once the
high pressure value has reached an initial threshold.
• Shedding one or more capacity stages once a second
protection threshold has been reached.
In the event of capacity stages being shed, no capacity increase
will be authorised on the circuit concerned for a period of 5
minutes.
5.18 - Pumping down
When the lead compressor in each circuit is started or stopped,
that circuit goes through a pumping down cycle to purge the
evaporator and suction line of refrigerant. The maximum
duration of this cycle is 3 minutes.
5.19 - Master/slave assembly
Two PRO-DIALOG Plus units can be linked to produce a master/
slave assembly. The two machines are interconnected over the
CCN bus. All parameters required for the master/slave function
must be configured through the Service configuration menu.
Master/slave operation requires the connection of a temperature
probe at the common manifold on each machine, if the heat
exchanger leaving water temperature is controlled.
The master/slave assembly can operate with constant or variable
flow. In the case of variable flow each machine must control its
own water pump and automatically shut down the pump, if the
cooling capacity is zero. For constant flow operation the pumps
for each unit are continuously operating, if the system is opera-
ting. The master unit can control a common pump that will be
activated, when the system is started. In this case the slave unit
pump is not used.
LOCAL OPERATING MODE
PARAMETER STATUS
HEATING/
COOLING
OPERATING
MODE
cooling
cooling
heating
holidays
holidays
ACTIVE SETPOINT
cooling setpoint 1
cooling setpoint 2
heating setpoint
cooling setpoint 1
cooling setpoint 2
LOCAL
SETPOINT
SELECTION
sp 1
sp2
-
auto
auto
SCHEDULE 2
PROGRAM STATUS
-
-
-
occupied
unoccupied
HEATING/
COOLING
OPOERATING
MODE
heating
cooling
cooling
-
-
ACTIVE SETPOINT
heating setpoint
cooling setpoint 1
cooling setpoint 2
cooling setpoint 1
cooling setpoint 2
CONTROL
CONTACT
-
sp 1
sp2
holidays
holidays
SCHEDULE 2
PROGRAM STATUS
-
-
-
occupied
unoccupied
REMOTE OPERATING MODE
PARAMETER STATUS
HEATING/COOLING
OPERATING MODE
cooling
cooling
heating
ACTIVE SETPOINT
cooling setpoint 1
cooling setpoint 2
heating setpoint
SCHEDULE 2
PROGRAM STATUS
occupied
unoccupied
-
CCN OPERATING MODE
PARAMETER STATUS
All control commands to the master/slave assembly (start/stop,
setpoint, heating/cooling operation, load shedding, etc.) are
handled by the unit which is configured as the master, and must
therefore only be applied to the master unit. They will be trans-
mitted automatically to the slave unit. The master unit can be
controlled locally, remotely or by CCN commands. Therefore
to start up the assembly, simply validate the Master operating
type (MASt) on the master unit. If the Master has been confi-
gured for remote control then use the remote volt-free contacts
for unit start/stop. The slave unit must stay in CCN operating
type continuously. To stop the master/slave assembly, select
Local Off (LOFF) on the master unit or use the remote volt-
free contacts if the unit has been configured for remote control.
One of the functions of the master unit (depending on its con-
figuration) may be the designation, whether the master or slave is
to be the lead machine or the follower. The roles of lead machine
and follower will be reversed when the difference in running
hours between the two units exceeds a configurable value,
ensuring that the running times of the two units are automatically
equalised. The changeover between lead machine and follower
may take place when the assembly is started up, or even whilst
running. The running time balancing function is not active if it
has not been configured: in this case the lead machine is
always the master unit.
The lead machine will always be started first. When the lead
machine is at its full available capacity, start-up delay (confi-
gurable) is initialised on the follower. When this delay has
expired, and if the error on the control point is greater than 1.7°C,
the follower unit is authorised to start and the pump is activated.
The follower will automatically use the master unit active set-
point. The lead machine will be held at its full available capa-
city for as long as the active capacity on the follower is not
zero. When the follower unit receives a command to stop, its
evaporator water pump is turned off with 20 seconds delay.
In the event of a communication fault between the two units,
each shall return to an autonomous operating mode until the
fault is cleared. If the master unit is halted due to an alarm, the
slave unit is authorised to start without prior conditions.
5.20 - Controlling Pro-Dialog Plus units with a System
Manager
Up to eight PRO-DIALOG Plus units (or System Manager
compatible units) can be controlled by one control module of
the FSM or CSM III type which can handle multi-tasking of
control functions such as starting units in sequence.