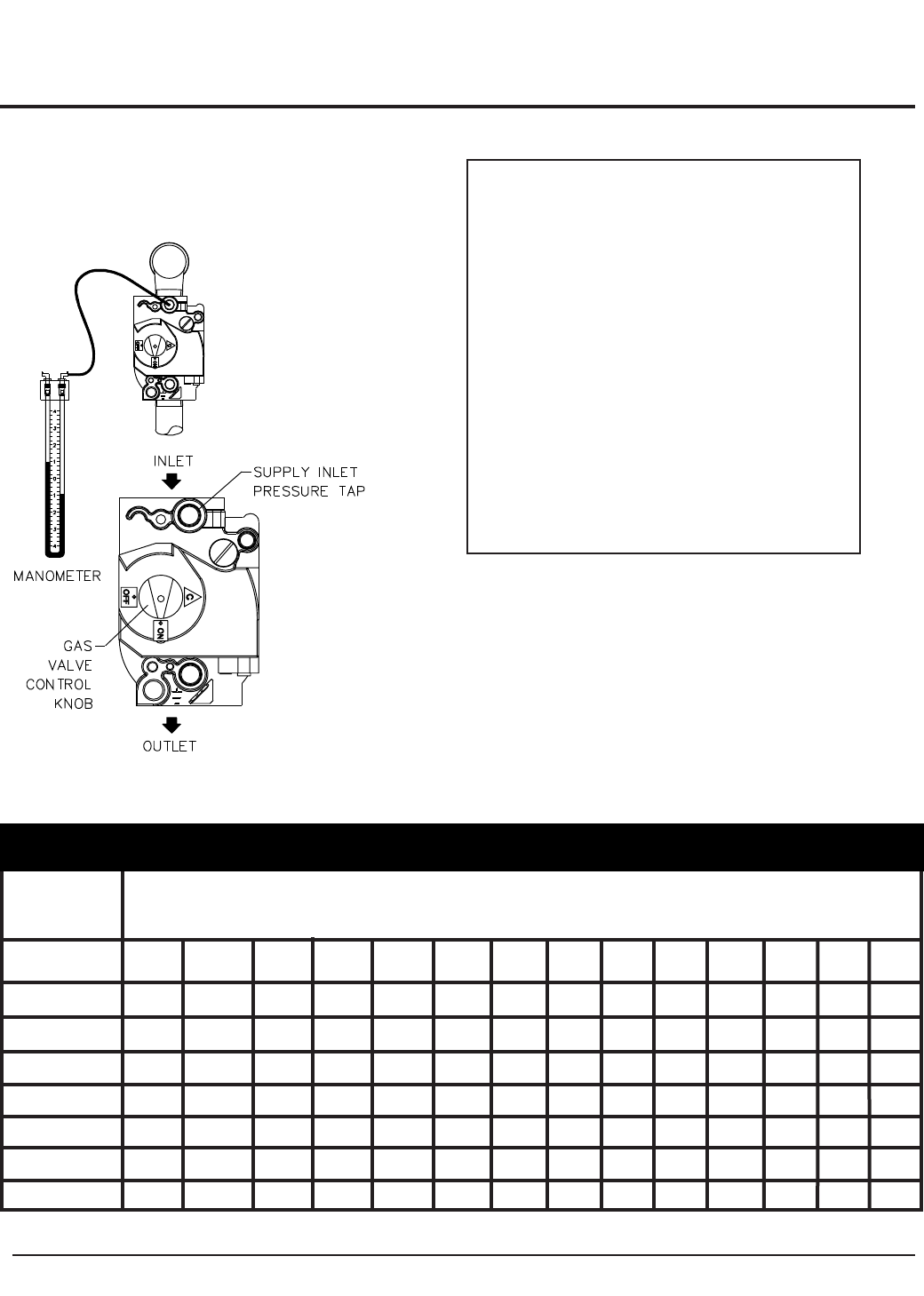
Installation and
Service Manual
31
Check burner performance by cycling the system while you
observe burner response. Burners should ignite promptly.
Flame pattern should be stable, see Burner Flames, page 56.
Turn system off and allow burners to cool, then cycle burners
again to ensure proper ignition and flame characteristics.
FIG. 30 Measuring Gas Supply Pressure at Combination
Gas Valve
Gas Manifold Pressure Adjustment
1. Loosen knurled knob that fastens the control panel access
door and pull out control panel.
2. Turn the power switch located in the lower left corner
behind the control panel access door to the “O” or “OFF”
position.
3. Remove the top front jacket access panels to access the gas
valves.
Nominal Iron Length of Pipe In Straight Feet
Pipe Size,
(Inches) 10 20 30 40 50 60 70 80 90 100 125 150 175 200
TABLE - L
Multiple Unit Installations Gas Supply Pipe Sizing
3/4" 369 256 205 174 155 141 128 121 113 106 95 86 79 74
1" 697 477 384 328 292 267 246 256 210 200 179 164 149 138
1 1/4" 1,400 974 789 677 595 543 502 472 441 410 369 333 308 287
1 1/2" 2,150 1,500 1,210 1,020 923 830 769 707 666 636 564 513 472 441
2" 4,100 2,820 2,260 1,950 1,720 1,560 1,440 1,330 1,250 1,180 1,100 974 871 820
2-1/2" 6,460 4,460 3,610 3,100 2,720 2,460 2,310 2,100 2,000 1,900 1,700 1,540 1,400 1,300
3" 11,200 7,900 6,400 5,400 4,870 4,410 4,000 3,800 3,540 3,300 3,000 2,720 2,500 2,340
4" 23,500 16,100 13,100 11,100 10,000 9,000 8,300 7,690 7,380 6,870 6,150 5,640 5,130 4,720
Maximum capacity of pipe in thousands of BTU’s per hour for gas pressures of 14 Inches Water Column (0.5 PSIG) or less and a total system
pressure drop of 0.5 Inch Water Column (Based on NAT GAS, 1025 BTU’s per Cubic Foot of Gas and 0.60 Specific Gravity).
IMPORTANT: The gas valves are
referenced to the fan pressurized
chamber by a hose connected from the
vent of the gas valve regulator to the
chamber pressure tap located on the front
inside portion of the jacket. Reference the
drawings in this section for component
and connection points for pressure
measurement. The procedure for
connecting a manometer or magnehelic
must be followed to obtain actual net
manifold pressure for normal operation. A
manometer or magnehelic gauge legible
in 0.1" increments up to 10 inches w.c. is
required to check and adjust the manifold
pressure. The regulator cover screw on
the gas valve must be in place and tight at
all times for the unit to operate properly.