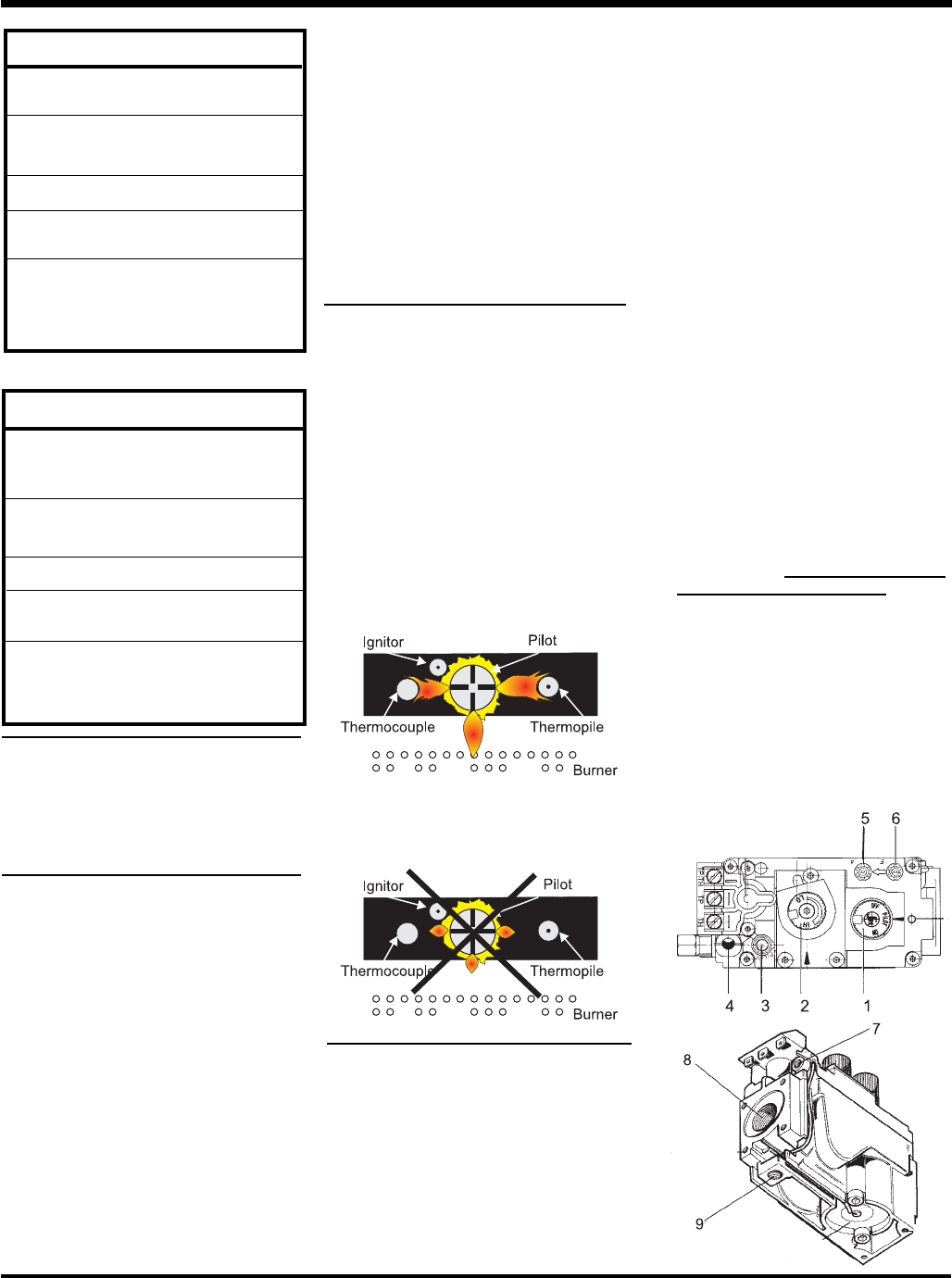
UltraGlow G36D Zero Clearance Direct Vent Gas Fireplace 23
INSTALLATION
GAS PIPE PRESSURE
TESTING
The appliance must be isolated from the gas
supply piping system by closing its individual
manual shut-off valve during any pressure
testing of the gas supply piping system at test
pressures equal to or less than 1/2 psig. (3.45
kPa). Disconnect piping from valve at pressures
over 1/2 psig.
HIGH ELEVATION
This unit is approved in Canada for altitude 0
to 4500 ft. (CAN1 2.17-M91) with the orifi ce
supplied.
GAS LINE
INSTALLATION
The gas line can be brought through either the
right or the left side of the appliance. The gas
valve is situated on the right hand side of the
unit and the gas inlet is on the right hand side
of the valve.
Note: If the gas line is being installed from
the left side, be sure to leave room to
accommodate servicing of the fan.
The gas line connection may be made of rigid
pipe, copper pipe or an approved fl ex connec-
tor. (If you are using rigid pipe, ensure that the
valve can be removed for servicing.) Since some
municipalities have additional local codes it is
always best to consult with your local authorities
and the CAN/CGA B149 installation code.
Incorrect fl ame pattern will have small, prob-
ably yellow fl ames, not coming into proper
contact with the rear burner or thermopile
or thermocouple.
For USA installations follow local codes and/or
the current National Fuel Gas Code, ANSI
Z223.1.
When using copper or fl ex connectors use only
approved fi ttings. Always provide a union so
that gas lines can be easily disconnected for
servicing. Flare nuts for copper lines and fl ex
connectors are usually considered to meet this
requirement.
Important: Always check for gas leaks with a
soap and water solution or gas leak detector.
Do not use open fl ame for leak testing.
PILOT ADJUSTMENT
Periodically check the pilot fl ames. Correct
fl ame pattern has three strong blue fl ames:
1 fl owing around the thermopile, 1 around
the thermocouple and 1 fl owing across the
burner (it does not have to be touching the
burner).
Note: If you have an incorrect fl ame pat-
tern, contact your Regency dealer
for further instructions.
The manifold pressure is controlled by a
regulator built into the gas control, and should
be checked at the pressure test point.
Note: To properly check gas pressure, both
inlet and manifold pressures should
be checked using the valve pressure
ports on the valve.
1) Make sure the valve is in the "OFF" posi-
tion.
2) Loosen the "IN" and/or "OUT" pressure
tap(s), turning counterclockwise with a
1/8" wide fl at screwdriver.
3) Attach manometer to "IN" and/or "OUT"
pressure tap(s) using a 5/16" ID hose.
4) Light the pilot and turn the valve to "ON"
position.
5) The pressure check should be carried out
with the unit burning and the setting should
be within the limits specifi ed on the safety
label.
6) When fi nished reading manometer, turn
off the gas valve, disconnect the hose and
tighten the screw (clockwise) with a 1/8"
fl at screwdriver. Note: Screw should be
snug, but do not over tighten.
S.I.T. VALVE DESCRIPTION
1) Gas cock knob
2) Manual high/low adjustment
3) Pilot Adjustment
4) Thermocouple Connection - option
5) Outlet Pressure Tap
6) Inlet Pressure Tap
7) Pilot Outlet
8) Main Gas Outlet
9) Alternative TC Connection
Point
G36D-NG System Data
For 0 to 4500 feet altitude
Burner Inlet Orifi ce Sizes: #42
Max. Input Rating 26,000 Btu/h
Min. Input Rating 13,100 Btu/h
Supply Pressure min.5.0" w.c.
Manifold Pressure
(High) 3.8"+/- 0.2"w.c.
Log Set: Ceramic fi bre, 7 per set.
Vent System: Simpson Dura-Vent Direct
Vent System or UltraGlow Direct
Vent System (Flex)
G36D-LP System Data
For 0 to 4500 feet altitude
Burner Inlet Orifi ce Sizes: #53
Max. Input Rating 26,000 Btu/h
Min. Input Rating 13,800 Btu/h
Supply Pressure min.12.0" w.c.
Manifold Pressure
(High) 11"+/- 0.2" w.c.
Log Set: Ceramic fi bre, 7 per set.
Vent System: Simpson Dura-Vent Direct
Vent System or UltraGlow Direct
Vent System (Flex)