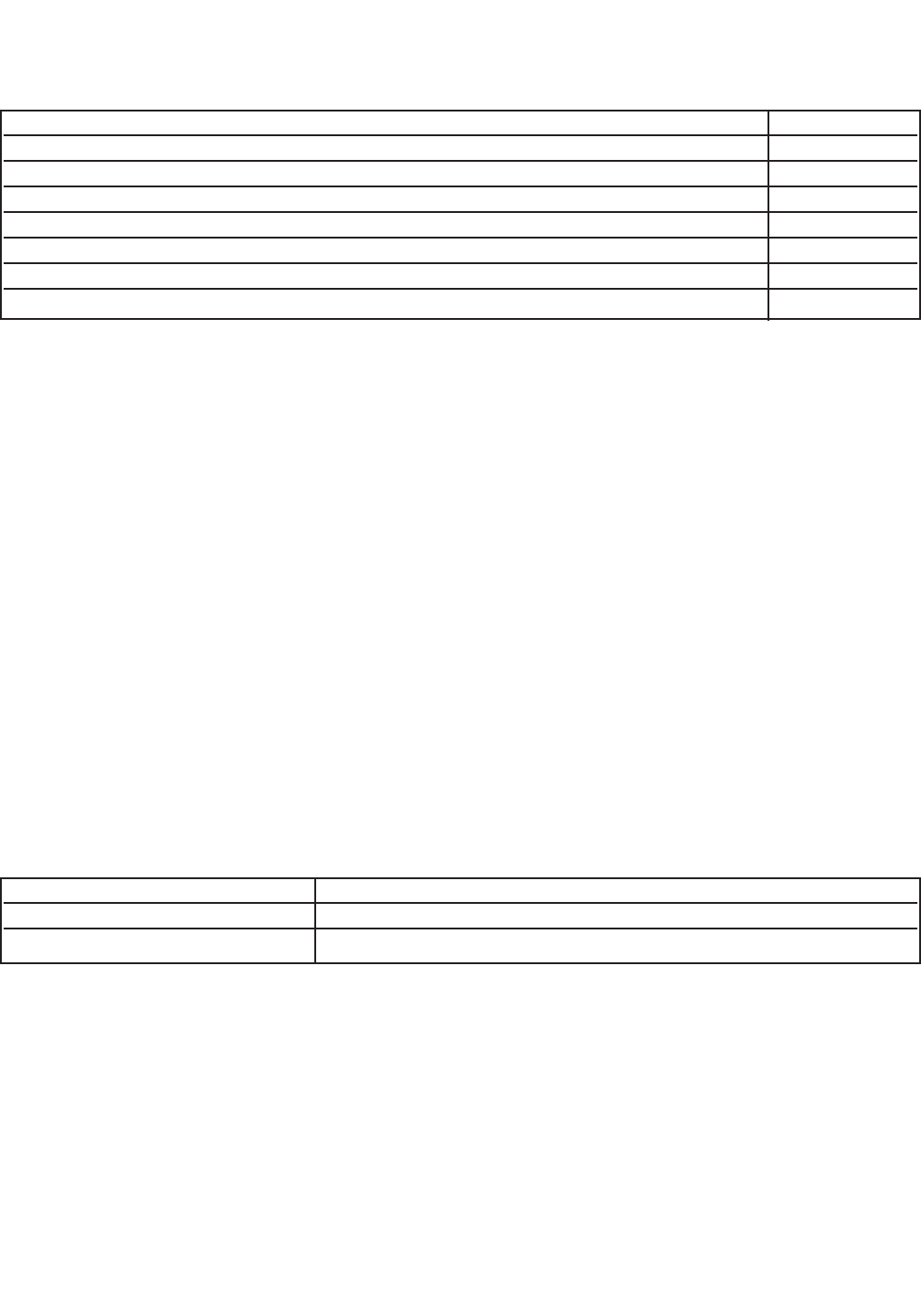
MODEL 54eA SECTION 15.0
TROUBLESHOOTING
15.9 TROUBLESHOOTING WHEN NO FAULT MESSAGE IS SHOWING - pH
15.9.1 Warning or error message during two-point calibration.
Once the two-point (manual or automatic) calibration is complete, the controller automatically calculates the sen-
sor slope (at 25°C). If the slope is less than 45 mV/pH, the controller displays a "Slope error low" message. If the
slope is greater than 60 mV/pH, the controller displays a "Slope error high" message. The controller will not update
the calibration. Check the following:
A. Are the buffers accurate? Inspect the buffers for obvious signs of deterioration, such as turbidity or mold
growth. Neutral and slightly acidic buffers are highly susceptible to molds. Alkaline buffers (pH 9 and greater),
if they have been exposed to air for long periods, may also be inaccurate. Alkaline buffers absorb carbon diox-
ide from the atmosphere, which lowers the pH. If a high pH buffer was used in the failed calibration, repeat the
calibration using a fresh buffer. If fresh buffer is not available, use a lower pH buffer. For example, use pH 4
and pH 7 buffer instead of pH 7 and pH 10 buffer.
B. Was adequate time allowed for temperature equilibration? If the sensor was in a process liquid substantially
hotter or colder than the buffer, place it in a container of water at ambient temperature for at least 20 minutes
before starting the calibration.
C. Were correct pH values entered during manual calibration? Using auto calibration eliminates error caused by
improperly entered values.
D. Is the sensor properly wired to the analyzer? Check sensor wiring including any connections in a junction box.
See Section 3.3.
E. Is the sensor dirty or coated? See the sensor instruction sheet for cleaning instructions.
F. Is the sensor faulty? Check the glass impedance. From the main display, press any key to enter the main
menu. Move the cursor to "Diagnostic variables". Press Enter (F4). Press the key until "Glass imped" is
showing. Refer to the table for an interpretation of the glass impedance value.
G. Is the controller faulty? The best way to check for a faulty controller is to simulate pH inputs. See Section 15.13.
Problem See Section
Warning or error message during two-point calibration 15.9.1
Warning or error message during standardization 15.9.2
Controller will not accept manual slope 15.9.3
Sensor does not respond to known pH changes 15.9.4
Calibration was successful, but process pH is slightly different from expected value 15.9.5
Calibration was successful, but process pH is grossly wrong and/or noisy 15.9.6
Process reading is noisy 15.9.7
less than 10 MΩ Glass bulb is cracked or broken. Sensor has failed.
between 10 MΩ and 1000 MΩ Normal reading
greater than 1000 MΩ pH sensor may be nearing the end of its service life.
97