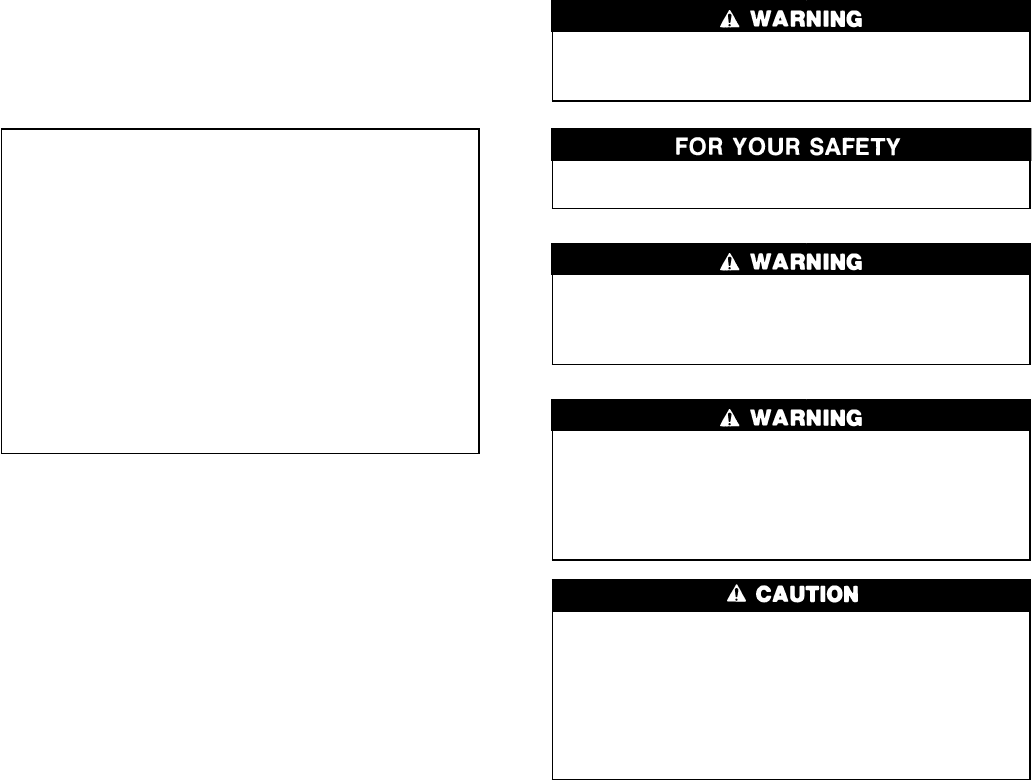
CONTENTS (cont)
Page
Lubrication ................................ 47
• COMPRESSORS
• FAN SHAFT BEARINGS
• FAN MOTOR BEARINGS
• DOOR HINGES
Coil Cleaning .............................. 47
Refrigerant Circuit ......................... 47
Oil Charge ................................. 49
Moisture/Liquid Indicator ................... 49
Filter Driers ................................ 49
Liquid Line Service Valve ................... 50
Compressor Suction and Discharge
Service Valves ............................ 50
High-Pressure Switch ...................... 50
Low-Pressure Switch ....................... 50
Pressure Relief ............................ 50
Adjustments ............................... 50
• EVAPORATOR FAN AND POWER EXHAUST
MOTOR PLATE
• BELT INSTALLATION AND TENSIONING
• PULLEY ALIGNMENT
Gas Valve Adjustment .......................52
• NATURAL GAS
Page
Main Burners ...............................52
• MAIN BURNER REMOVAL
Protective Devices ......................... 52
• COMPRESSOR PROTECTION
• EVAPORATOR-FAN MOTOR PROTECTION
• CONDENSER-FAN MOTOR PROTECTION
• HIGH- AND LOW-PRESSURE SWITCHES
Variable Frequency Drive (VFD) ............. 53
• SUPPLY FAN VFD
• EXHAUST FAN VFD
• DISPLAYING FAULT SEQUENCE
Control Modules ........................... 53
Processor Module(s) (PSIO) ................ 54
High-Voltage Relay Modules
(DSIO1 and DSIO2) ........................ 54
Refrigerant Feed Components .............. 54
Thermostatic Expansion Valve (TXV) ........ 54
Hot Gas Bypass ........................... 55
Condenser Fans ........................... 55
Compressor Removal ...................... 55
Compressor Replacement .................. 55
TROUBLESHOOTING ......................55-58
START-UP CHECKLIST ..............CL-1 to CL-4
GENERAL
This installation instruction contains base unit installa-
tion, start-up, and service instructions only. For complete in-
formation on PIC (Product Integrated Controls) controls and
troubleshooting, refer to separate Controls and Troubleshoot-
ing literature also enclosed in this literature packet.
IMPORTANT:
1. Tune all loops immediately after starting units. Re-
fer to Control Loop Checkout section on page 40
for more information on tuning loops.
2. The Data Reset function should be performed any
time one or more of the unit factory configuration
values are changed.
3. The HSIO (human sensor input/output) keypad and
display module is required for initial start-up of unit.
All units are shipped in STANDBYmode. The HSIO
must be used to change the unit to RUN mode. The
HSIO is not required for normal operation, how-
ever, at any time the unit needs to be transferred
back into STANDYBYmode, such as when servic-
ing a unit, it must be done with the HSIO.
SAFETY CONSIDERATIONS
Installation and servicing of air-conditioning equipment
can be hazardous due to system pressure and electrical com-
ponents. Only trained and qualified service personnel should
install, repair, or service air-conditioning equipment.
Untrained personnel can perform basic maintenance func-
tions of cleaning coils and filters and replacing filters. All
other operations should be performed by trained service per-
sonnel. When working on air-conditioning equipment, ob-
serve precautions in the literature, tags and labels attached
to the unit, and other safety precautions that may apply.
Follow all safety codes, including ANSI (American Na-
tional Standards Institute) Z223.1. Wear safety glasses and
work gloves. Use quenching cloth for unbrazing operations.
Have fire extinguisher available for all brazing operations.
Before performing service or maintenance operations on
unit, turn off main power switch to unit. Electrical shock
could cause personal injury.
Do not store or use gasoline or other flammable vapors
and liquids in the vicinity of this or any other appliance.
Improper installation, adjustment, alteration, service,
or maintenance can cause injury or property damage.
Refer to this manual. For assistance or additional infor-
mation, consult a qualified installer or service agency.
This unit uses a microprocessor-based electronic con-
trol system. Do not use jumpers or other tools to short
out components, or to bypass or otherwise depart from
recommended procedures. Any short-to-ground of the
control board or accompanying wiring may destroy the
electronic modules or electrical components.
Disconnect gas piping from 48 Series units when leak
testing at pressures greater than 0.5 psig. Pressures greater
than 0.5 psig will cause gas valve damage resulting in
a hazardous condition. If gas valve is subjected to pres-
sure greater than 0.5 psig, it must be replaced. When
pressure testing field-supplied gas piping at pressures of
0.5 psig or less, the unit connected to such piping must
be isolated by manually closing the gas valve.
2