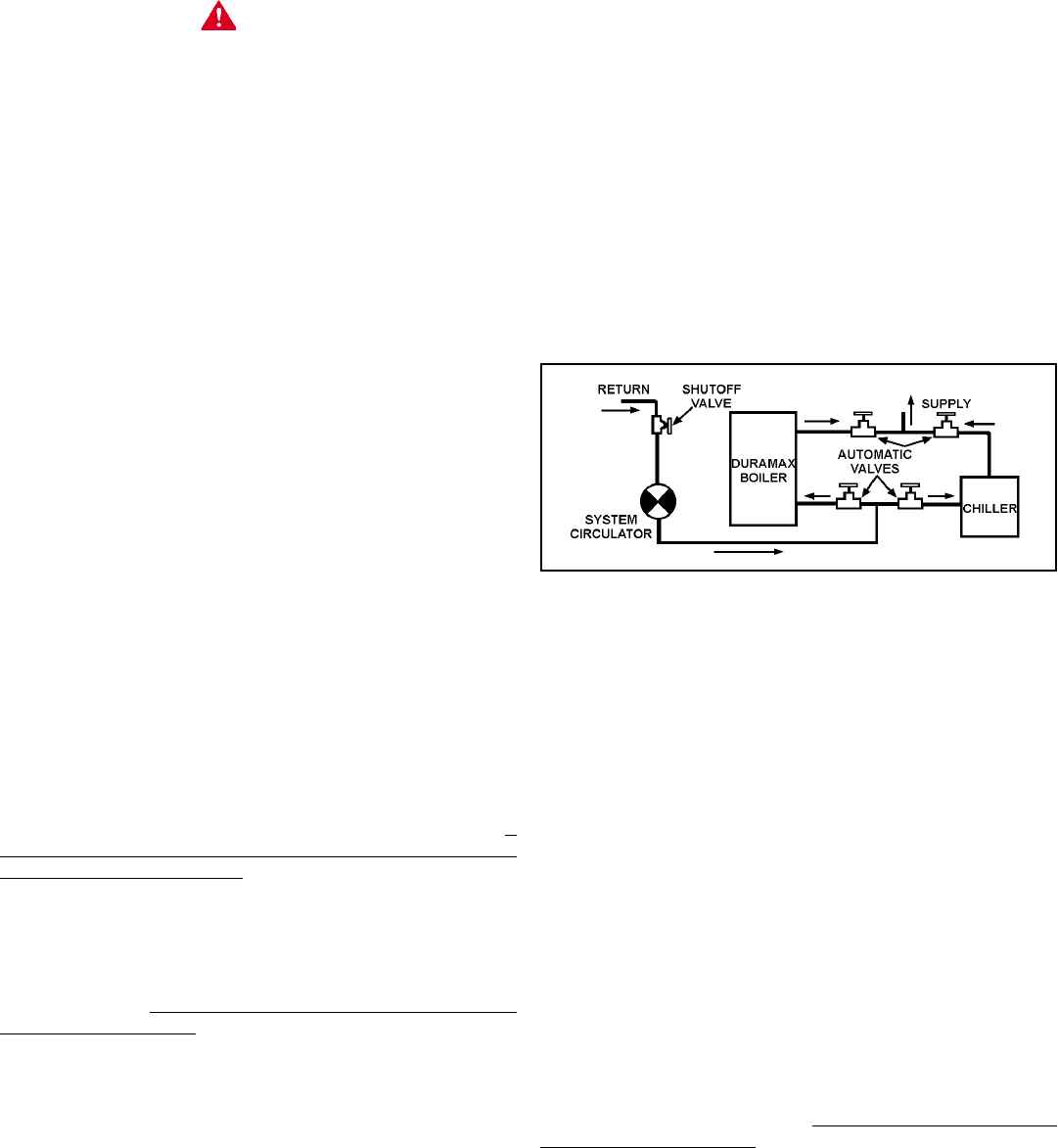
12
IF ANY OF THE ORIGINAL WIRE, AS SUPPLIED WITH THE
APPLIANCE, MUST BE REPLACED, IT MUST BE REPLACED
WITH TYPE 105°C WIRE OR ITS EQUIVALENT, EXCEPT FOR
THE FLAME SENSOR AND IGNITION CABLE WHICH ARE 250°C.
SERVICING WIRING AND/OR CONTROL
CAUTION
Label all wires prior to disconnection when servicing controls. Wiring
errors can cause improper and dangerous operation.
Verify proper operation after servicing.
SYSTEMS EQUIPMENT
INSTALLATION
The following is a brief description of the equipment required for
installations noted in this manual. All installations must comply
with local codes.
The boilers described in this manual may be used for space heating
or for the heating of potable water. If the heater is to be used for
hydronic space heating, follow the descriptions given for equipment
required for installation on pages 12 through 31. However, if units
are to be used for heating potable water, the information describing
specific systems is found starting on page 32. Installations must
comply with all local codes.
WATER SUPPLY LINE
These boilers can be used ONLY in a forced circulation hot water
heating system. Since most forced circulation systems will be of
the closed type, install the water supply line as shown on piping
diagrams, fig’s. 10 and 14.
Fast filling of large pipe, old radiator installations (where high
pressures are not available) requires bypassing of the pressure
reducing valve. Generally, pressure purging is not possible with a
well pump system. High point air venting is essential. For details,
refer to OPERATING INSTRUCTIONS section of this manual.
If the system is of the open type, a pressure reducing valve will not
be required as the water supply to the system will be controlled by
a manually operated valve. An overhead surge tank is required.
A
MINIMUM PRESSURE OF 15 PSI MUST BE MAINTAINED ON
THE BOILER AT ALL TIMES to ensure avoidance of potential
damage to the boiler which may not be covered by the warranty.
EXPANSION TANK
If the system is of the closed type, install an expansion tank as
shown in fig. 10.
The sizing of the expansion tank for a closed
system is very important and is directly related to the total water
volume of the system. Refer to ASME or other reliable specifications
for sizing.
An air separator as shown in the piping diagrams is recom- mended
especially for modern commercial hydronic systems.
VENT VALVES
It is recommended that automatic, loose key or screwdriver type
vent valves be installed at each convector or radiator.
SYSTEM HEADERS
Split systems with individual supply and return lines from the boiler
room should normally have this piping connected to supply and
return manifold headers near the boiler. To achieve good water
distribution with minimum pressure drop for several circuits,
manifolds should be larger than system loops.
The circuits should be spaced on the header at a minimum of 3"
(76 mm) center to center. Install a balancing cock in each return line.
Manifold headers are recommended for split systems with or without
zone valves and also those installations with zone circulators. If
the system is to be split at remote points, good practice requires
special attention be given to main pipe sizing to allow balancing of
water flow.
COOLING PIPING
The boiler, when used in connection with a refrigeration system,
must be installed so the chilled medium is piped in parallel with the
boiler with appropriate valves to prevent the chilled medium from
entering the boiler. See figure 7.
FIGURE 7
Water temperature in the heating system must be reduced to less
than 100°F before cooling system is started, or damage to the
chiller unit may occur.
The boiler piping system of a hot water boiler connected to heating
coils located in air handling units where they may be exposed to
refrigerated air circulation must be equipped with flow control valves
or other automatic means to prevent gravity circulation of the boiler
water during the cooling cycle.
Primary/secondary pumping of both the chiller(s) and the boiler(s)
is an excellent winter-summer change-over method, because
cooling flow rates are much more than heating flow rates. In this
way each system (heating or cooling) is circulated independently.
SAFETY FLOW SWITCH
The safety flow switch is a safety device which must be installed at
the water outlet of the unit to prevent main burner operation in the
event of inadequate water flow through the boiler.
This switch may be mounted in a horizontal pipe line or a vertical
pipe line with upward water flow. Do not install the switch where
the water flow is downward.
For best performance mount the switch in a section of pipe where
there is a straight run of at least 5 pipe diameters on each side of
the flow switch (i.e. do not locate adjacent to valves, elbows, orifices,
etc.).