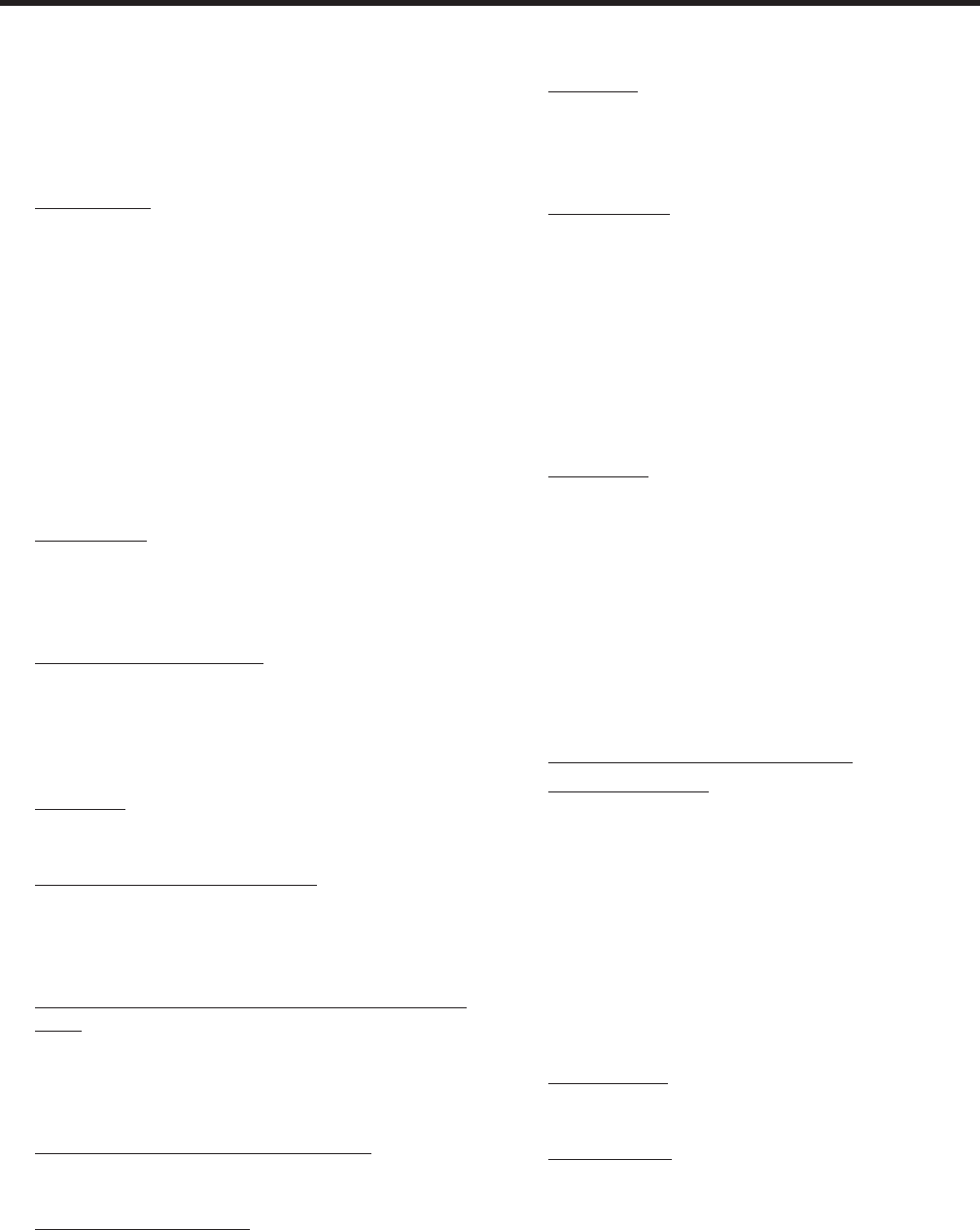
JOHNSON CONTROLS
42
FORM 100.50-EG5 (108)
mechanically expanded into the end sheets. Coils
are confi gured in a V-bank confi guration, with indi-
vidual fl at coils rotated from the vertical plane for
protection from hail damage for each condensing
circuit. Condensing coils shall have a subcooler for
more effi cient, stable operation.
3. Compressors: Units shall use industrial-duty her-
metic scroll compressors, piped and charged with
oil and R-410A refrigerant. Compressors shall have
an enlarged, liquid-carrying capacity to withstand
rugged operating conditions. Compressor frame
shall be cast iron, with cast-iron fi xed and orbiting
scrolls. Each compressor shall feature a line break,
designed to protect the compressor from over-tem-
perature and over-current conditions. Compressors
shall be vibration-isolated from the unit, and installed
in an easily accessible area of the unit. All compres-
sor-to-pipe connections shall be brazed to minimize
potential for leaks. Each compressor shall include
an oil sight glass.
4. Low Ambient: Compressors shall operate down to
0°F Control [optional] by monitoring the refrigeration
system discharge pressure and adjusting condenser
airfl ow to maintain the proper head pressure to
protect compressor operation.
5. In-Line Refrigerant Driers: Refrigerant piping in-
cludes thermal-expansion valves with replaceable
thermostatic elements, high- and low-pressure
switches, anti-recycling timing device to prevent
compressor restart for five minutes after shut-
down.
6. Freezestat: Freezestats shall be provided to prevent
coil freeze-up and reduce the risk of liquid fl oodback
to the compressor.
7. Condenser Wire Grill [optional]: The condenser
section shall be enclosed by a wire grill condenser
enclosure on the three exposed sides. Plastic fi nish
shall match the color and salt-spray specifi cations
of the unit exterior.
8. Hot-Gas Bypass [optional on constant-volume
units]: Hot-gas-bypass piping shall be provided to
enable compressor unloading to as low as 5% to
better match cooling demand at low loads, prevent
excessive cycling of the compressor, and reduce
the risk of coil freeze-up.
9. Compressor-sound treatment [optional]: Compres-
sor sound blankets shall be provided to attenuate
radiated sound from the compressors.
10. Service Valves [optional]: Liquid, suction and dis-
charge service valves shall be included to provide
a means of isolating the refrigerant charge in the
system so that the refrigeration system may be
serviced without removing the charge of the unit.
Controls (Simplicity Elite)
1. Enclosure: Unit shall be shipped complete with
factory-confi gured, installed, wired and tested roof-
top unit controller housed in a rain-and-dust-tight
enclosure with hinged, latched, and gasket sealed
door.
2. Basic Controls: Control shall include automatic start,
stop, operating, and protection sequences across
the range of scheduled conditions and transients.
The rooftop unit controller shall provide automatic
control of compressor start/stop, energy-saver-
delay and anti-recycle timers, condenser fans, and
unit alarms. Automatic reset to normal operation
after power failure. Software stored in nonvolatile
memory, with programmed setpoints retained in
lithium battery backed real time clock (RTC) memory
for minimum 5 years.
3. Diagnostics: Upon demand, the controller shall run
through a self-diagnostic check to verify proper
operation and sequence loading. The rooftop unit
controller shall continually monitor all input and out-
put points on the controller and to maintain proper
operation. The unit shall continue to operate in a
trouble mode or shut down as necessary to prevent
an unsafe condition for the building occupants, or to
prevent damage to the equipment. In the event of
a unit shutdown or alarm, the operating conditions,
date and time shall be stored in the shutdown history
to facilitate service and troubleshooting.
4. Controls and BAS Communications
(RS-485) Modbus: The unit shall include Modbus
communications directly from the unit controller.
Equipment that is not native to the unit.
A fi eld installed Modlinc Gateway device is required
by the manufacturer to communicate to BACnet
(MSTP), A control points list shall be provided by
the manufacturer to facilitate communications
programming with the building automation system.
Programming, establishing communications and
commissioning shall be the responsibility of the in-
stalling controls contractor. Start-up assistance and
support may be purchased from the manufacturer.
Analog inputs: 0-10VDC inputs shall be provided
for remote reset of supply air temperature, and duct
static pressure
Binary outputs: Dry (or “wet”) contacts shall be pro-
vided for alarm outputs for supply fan fault, cooling/
heating fault, or general/sensor faults. Contacts
shall also be provided for occupied/unoccupied,
shutdown, smoke purge, exhaust or pressurization
operations; call for cooling or heating.
Guide Specifi cations (continued)