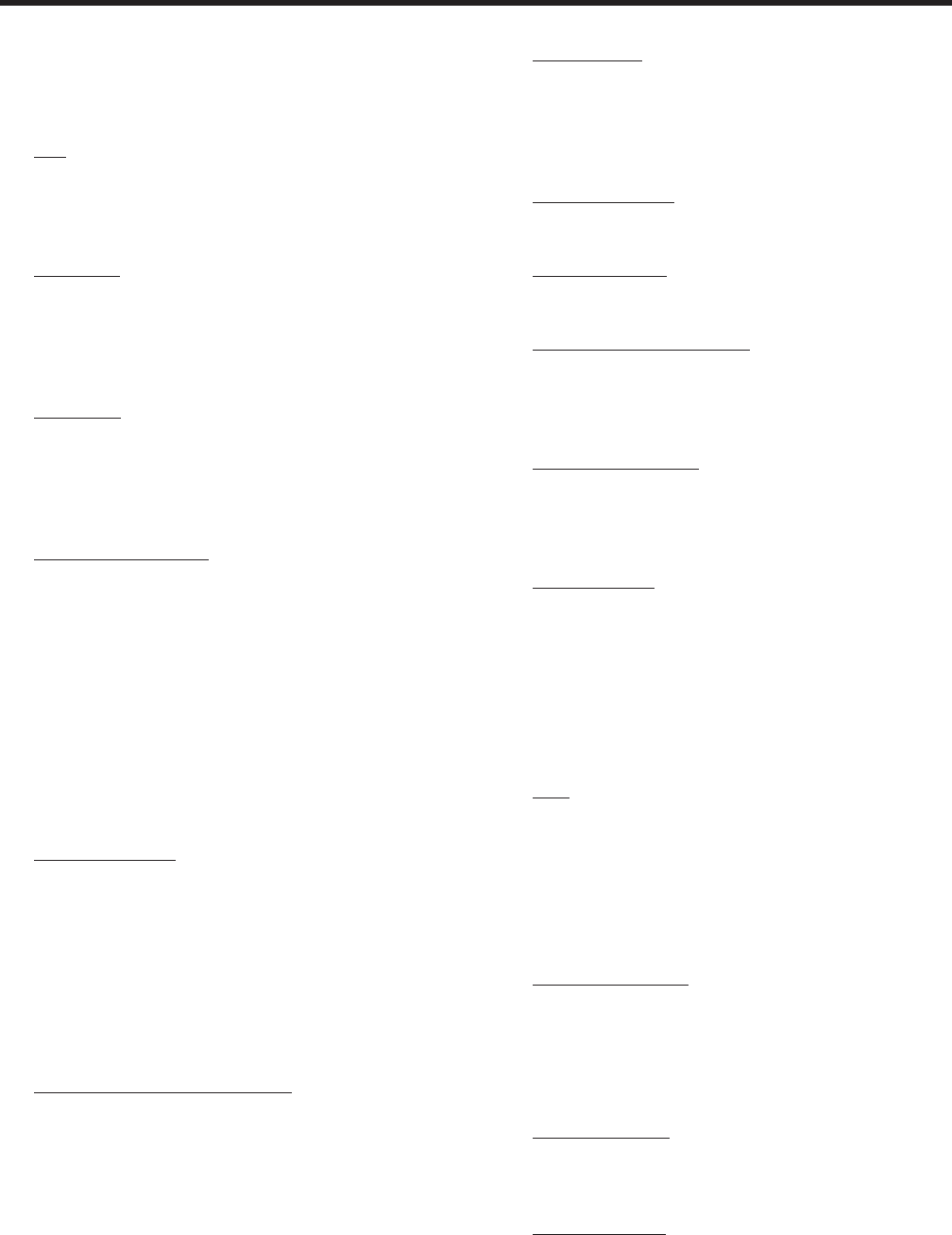
FORM 100.50-EG5 (108)
41
JOHNSON CONTROLS
The intermediate pans shall have drop tubes to guide
condensate to the main drain pan.
Supply Fan Section
1. Fan: The fan section shall be equipped with a single
double-width, double-inlet (DWDI), forward-curved
[airfoil optional] centrifugal type wheel for horizontal
discharge. An access door shall be provided on both
sides of the unit for fan/motor access.
2. Fan Motor: Fan motors shall be NEMA design ball-
bearing types with electrical characteristics and
horsepower as specifi ed. Motors shall be 1750
RPM, open drip-proof type [TEFC optional]. The
motor shall be located within the unit on an adjust-
able base.
Mountings: Fan and fan motor shall be internally
mounted and isolated on a full-width, isolator-sup-
port channel using 1-inch [2-inch] springs. The fan
discharge shall be connected to the fan cabinet
using a fl exible connection to insure vibration-free
operation.
Bearings and Drives: Fan bearings shall be self-
aligning, pillow block or fl anged type regreaseable
ball bearings and shall be designed for an average
life (L50) of at least 200,000 hours. All bearings shall
be factory lubricated and equipped with standard
hydraulic grease fi ttings and lube lines extended
to the motor side of the fan. Fan drives shall be
selected for a 1.5 service factor and antistatic belts
shall be furnished. All drives shall be fi xed pitch. Fan
shafts shall be selected to operate well below the
fi rst critical speed and each shaft shall be factory
coated after assembly with an anticorrosion coat-
ing.
3. VAV Fan Control: VAV supply fan control shall be
accomplished by using a variable-frequency drive
matched to the supply-fan motor HP. The VFD
shall include an integral DC line reactor to reduce
harmonic distortion in the incoming and outgoing
power feeds. If a DC line reactor is not provided, an
AC line reactor must be provided. Inlet guide vanes
shall not be acceptable. VFD control keypads shall
be located in the control cabinet for accessibility and
servicing while the unit is operating.
4. Optional VFD manual bypass: a three-contactor
manual bypass shall be provided to permit replace-
ment of the VFD in the event of a power failure.
Discharge Plenum
[SELECT ONE OF THE FOLLOWING HEAT/NO
HEAT CONFIGURATIONS]
1. Cooling Only: The discharge-air-temperature sen-
sor shall be located in the discharge plenum and
be located such that it accurately measures the
supply-air temperature. Walls shall be lined with a
solid liner to prevent erosion of the insulation and
to separate insulation from the air stream.
1. Staged Gas Heat: The heating section shall include
an induced-draft furnace with two stages [four
stages or six stages] of heating capacity.
Heat Exchanger: The heat exchanger shall be con-
structed of tubular aluminized steel [stainless steel],
with stainless steel fl ue baffl es and fl ue assembly.
Burner and Ignition Control: The burner shall include
a direct-driven induced-draft combustion fan with
energy effi cient intermittent direct spark ignition,
redundant main gas valves with pressure regula-
tor.
Combustion-Air Fan: The inducer fan(s) shall main-
tain a positive fl ow of air through each tube, to expel
the fl ue gas and to maintain a negative pressure
within the heat exchanger relative to the conditioned
space.
Safety Devices: A high-limit controller with automatic
reset to prevent the heat exchanger from operat-
ing at an excessive temperature shall be included.
An air-proving switch shall prevent ignition until
suffi cient airfl ow is established through the heat
exchanger. A rollout switch shall provide secondary
airfl ow-safety protection. The rollout switch shall
discontinue furnace operation if the fl ue becomes
restricted.
Flue: The furnace fl ue shall be shipped loose to pro-
tect it from damage during transit. The fl ue shall be
fi eld-mounted by the installing contractor. The fl ue
outlet shall be located above the unit to help prevent
recycling of combustion gases back through the
heat exchanger. Agency Certifi cation: Gas heating
sections are both ETC/CETL approved to both US
and Canadian safety standards.
1. Heat Exchanger(s): The heat exchanger(s) shall be
constructed of tubular aluminized steel [stainless
steel], with stainless steel fl ue baffl es and fl ue as-
sembly.
Condenser Section
1. Condenser Fans: Condenser fans shall be matched
up with compressors to optimize system control.
Condenser fans shall be propeller-type, directly
driven by permanently lubricated TEAO motor.
2. Condenser Coil: Condenser coils shall be seam-
less copper tubes, arranged in staggered rows,