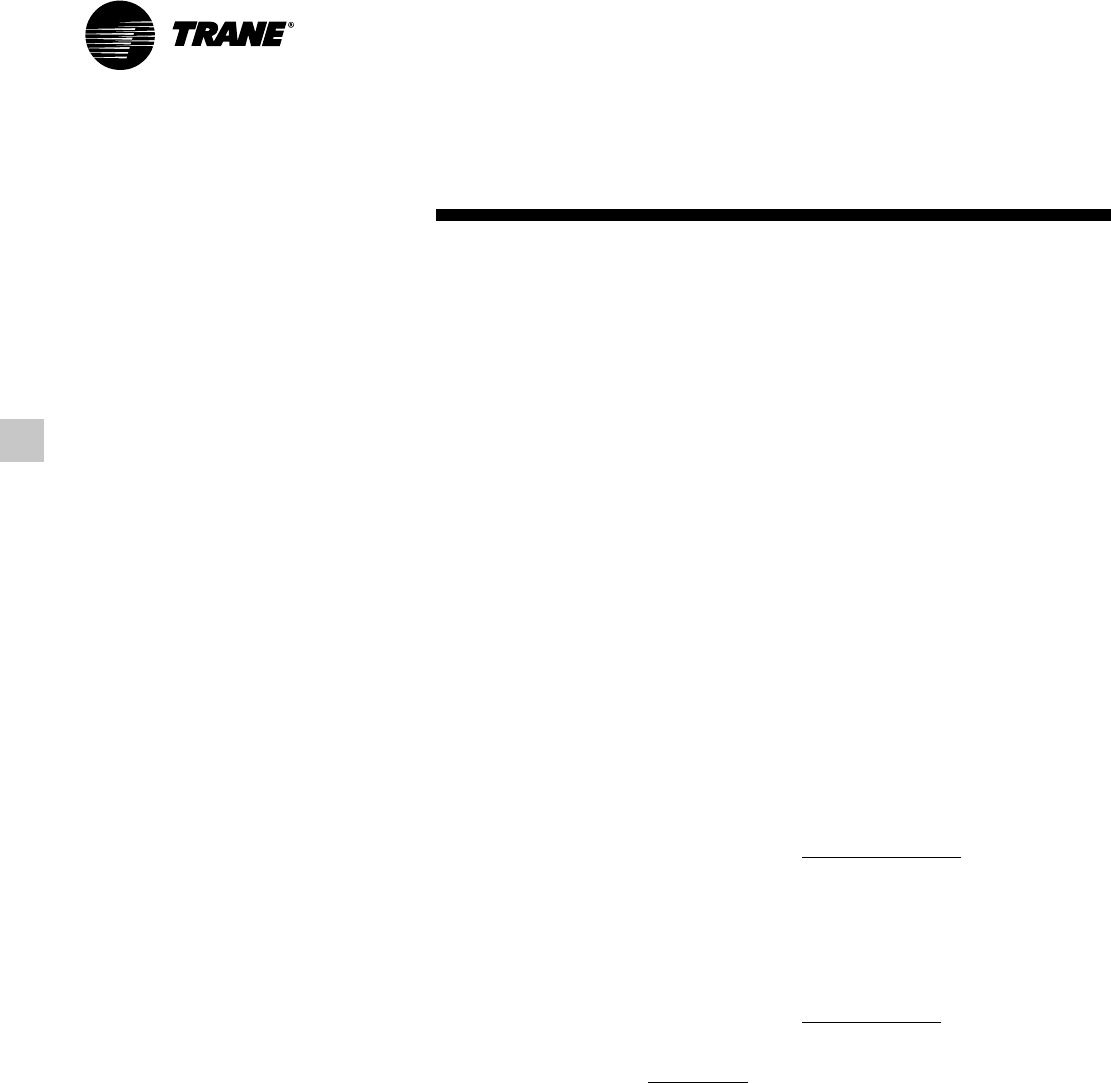
RT-PRC010-EN16
Selection
Procedure
This section outlines a step-by-step
procedure that may be used to select a
Trane single-zone air conditioner. The
sample selection is based on the
following conditions:
• Summer outdoor design conditions —
95 DB/76 WB ambient temperature
• Summer room design conditions —78
DB/65 WB
• Total cooling load — 430 MBh (35.8
tons)
• Sensible cooling load — 345 MBh (28.8
tons)
• Outdoor air ventilation load — 66.9
MBh
• Return air temperature — 80 DB/65 WB
Winter Design:
• Winter outdoor design conditions —0 F
• Return air temperature — 70 F
• Total heating load — 475 MBh
• Winter outdoor air ventilation load —
133 MBh
Air Delivery Data:
• Supply fan cfm — 17,500 cfm
• External static pressure — 1.2 in wg
• Minimum outdoor air ventilation —
1,750 cfm
• Exhaust fan cfm — 12,000 cfm
• Return air duct negative static pressure
— 0.65 in wg
Electrical Characteristics:
• Voltage/cycle/phase — 460/60/3 Unit
Accessories:
• Gas fired heat exchanger — high heat
module
• Throwaway filters
• Economizer
• Modulating 100 percent exhaust/
return fan
COOLING CAPACITY SELECTION
Step 1 — Nominal Unit Size Selection
A summation of the peak cooling load
and the outside air ventilation load
shows: 430 MBh + 66.9 MBh = 496.9
MBh required unit capacity. From
Table PD-9, a 50 ton unit capacity with
standard capacity evaporator coil at
80 DB/65 WB, 95 F outdoor air
temperature and 17,500 total supply cfm
is 551 MBh total and 422 MBh sensible.
Thus, a nominal 50 ton unit with
standard capacity evaporator coil
is selected.
Step 2 — Evaporator Coil Entering
Conditions
Mixed air dry bulb temperature
determination:
Using the minimum percent of OA (1,750
cfm ÷ 17,500 cfm = 10 percent),
determine the mixture dry bulb to the
evaporator.
RADB + % OA (OADB - RADB) = 80 +
(0.10) (95 - 80) = 80 + 1.5 = 81.5 F
Approximate wet bulb mixture
temperature:
RAWB + % OA (OAWB - RAWB) = 65 +
(0.10) (76 - 65) = 65 + 1.1 = 66.1 F
Step 3 — Determine Supply Fan Motor
Heat Gain
Having selected a nominal 50 ton unit,
the supply fan bhp can be calculated. The
supply fan motor heat gain must be
considered in final determination of unit
capacity.
Supply Air Fan
Determine unit total static pressure at
design supply cfm:
External Static Pressure 1.2 inches
Evaporator Coil 0.25 inches
(Table PD-43)
Return Duct Negative 0.65 inches
Static Pressure
Heat Exchanger 0.31 inches
(Table PD-43)
Throwaway Filter 0.10 inches
(Table PD-43)
Economizer w/Exhaust Fan 0.12 inches
(Table PD-43)
Trane Roof Curb 0.13 inches
(Table PD-43)
Unit Total Static Pressure 2.76 inches
Using total of 17,500 cfm and total
static pressure of 2.76 inches, enter Table
PD-36. Table PD-36 shows 15.3 bhp with
924 rpm.
From Chart SP-1 supply fan motor heat
gain = 46.0 MBh.
Step 4 — Determine Total Required
Cooling Capacity
Required capacity = Total peak load + OA
load + supply air fan motor heat.
Required capacity = 430 + 66.9 +
46.0 = 543 MBh (45.2 tons)
Step 5 — Determine Unit Capacity
From Table PD-9, unit capacity at 81.5 DB/
66.1 WB entering the evaporator, 17,500
supply air cfm, 95 F outdoor ambient, is
561 MBh (45.8 tons) with 426 MBh
sensible.
Step 6 — Determine Leaving Air
Temperature
Unit sensible heat capacity corrected for
supply air fan motor heat = 426 MBh - 46
MBh = 380 MBh.
Supply air dry bulb temperature
difference =
Sensible Btu =
1.085 x Supply cfm
380 MBh ÷ (1.085 x 17,500 cfm)
= 20.0 F
Supply air dry bulb = 81.5 DB - 20.0
= 61.5 F
Unit enthalpy difference =
Total Btu =
4.5 x Supply cfm
561 MBh ÷ (4.5 x 17,500 cfm) =
7.12 Btu/lb
Leaving enthalpy = h(ent WB) -
h(diff). From Table 21-1 h(ent WB) =
30.9 Btu/lb
Leaving enthalpy = 30.9 Btu/lb - 7.12
Btu/lb = 23.78 Btu/lb
Supply air wet bulb = 55.9
Leaving air temperature = 61.5
DB/55.9 WB