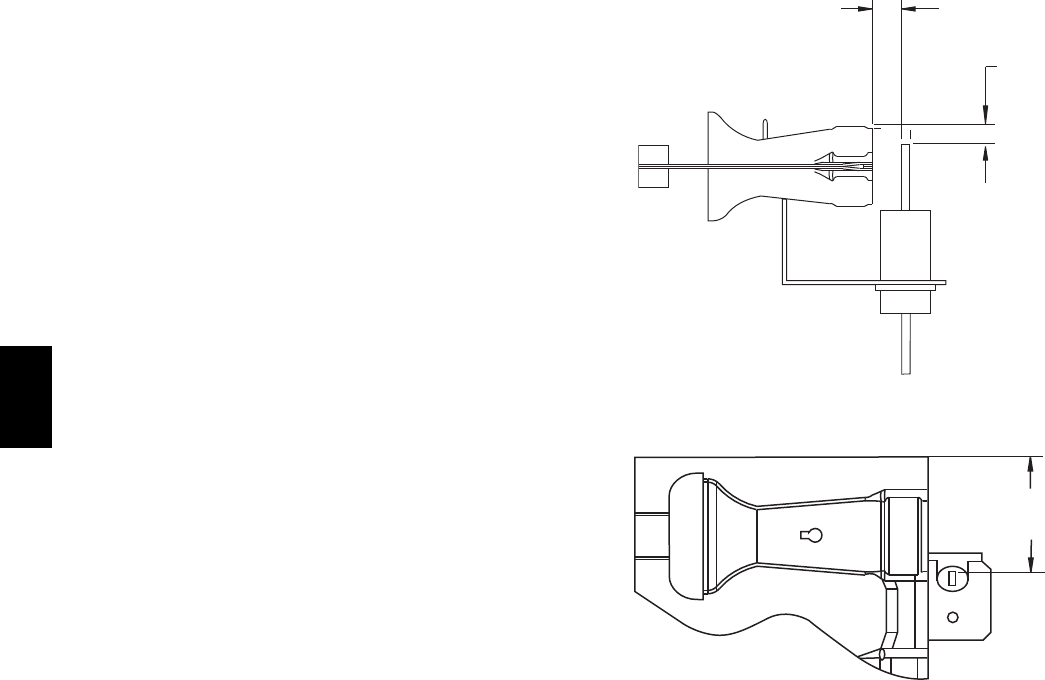
48
them thoroughly. A heavy build --up of soot and carbon indicates
that a problem exists which needs to be corrected, s uch as
improper adjustment of manifold pressure, insufficient or poor
quality combustion air, incorrect size or damaged manifold
orifice( s), improper gas, or a restricted heat exchanger. Action
must be taken to correct the problem.
If it becomes necessary to clean the heat exchangers because of
dust or corrosion, proceed as follows:
1. Turn OFF gas and electrical power to furnace.
2. Remove outer access door.
3. Disconnect vent connector from furnace vent elbow.
4. For downflow or horizontal furnace having an internal
vent pipe, remove internal vent pipe within the casing.
5. Disconnect wires to the following components. Mark
wires to aid in reconnection of (be careful when
disconnecting wires from switches because damage may
occur):
a. Draft safeguard switch.
b. Inducer motor.
c. Pressure switch(es).
d. Limit overtemperature switch.
e. Gas valve.
f. Hot surface igniter.
g. Flame--sensing electrode.
h. Flame rollout switches.
6. Remove screws that fasten the collector box assembly to
the cell panel. Be careful not to damage the collector box.
Inducer assembly and elbow need not be removed from
collector box.
7. Disconnect gas line from gas manifold.
8. Remove the 5 screws that attach the burner assembly to
the cell panel. The gas valve and individual burners need
not be removed from support assembly. Remove NOx
baffles if installed.
NOTE: Be very careful when removing burner assembly to
avoid breaking igniter. See Fig. 56 and 57 for correct igniter
location.
9. Using field--provided 25--caliber rifle cleaning brush,
36--in. (914 mm) long, 1/4” (6 mm) diameter steel spring
cable, a variable speed, reversible electric drill, and
vacuum cleaner, clean cells as follows:
a. Remove metal screw fitting from wire brush to allow
insertion into cable.
b. Insert the twisted wire end of brush into end of spring
cable, and crimp tight with crimping tool or crimp by
strikingwith ball-- peenhammer.TIGHTNESS ISVERY
IMPORTANT.
9/32”
7.1mm
5/16”
7.9mm
A05025
Fig. 56 -- Igniter Position--Side View
1-7/8
47.6 mm
A05026
Fig. 57 -- Igniter Position--Top View
NOTE: The materials needed in item 9 can usually be purchased
at local hardware stores.
(1.) Attach variable--speed, reversible drill to the end of
spring cable (end opposite brush).
(2.) Insert brush end of cable into the outlet opening of
cell and slowly rotate with drill. DO NOT force
cable. Gradually insertcableinto upperpass ofcell.
(See Fig. 58.)
(3.) Work cable in and out of cell 3 or 4 times to obtain
sufficient cleaning. DO NOT pull cable with great
force. Reverse drill and gradually work cable out.
(4.) Insert brush end of cable in burnerinlet opening of
cell, and proceed to clean 2 lower passes of cell in
same manner as upper pass.
(5.) Repeat foregoing procedures until each cell in
furnace has been cleaned.
(6.) Using vacuum cleaner, remove residue from each
cell.
(7.) Us ing vacuum cleaner with soft brush attachment,
clean burner assembly.
(8.) Clean flame sensor with fine steel wool.
(9.) Install NOx baffles (if removed).
(10.) Reinstall burner assembly. Center burners in cell
openings.
10. Remove old sealant from cell panel and collector box
flange.
11. Spray releasing agent on the heat exchanger cell panel
where collector box assembly contacts cell panel.
NOTE: A releasing agent such as cooking spray or equivalent
(must not contain corn or canola oil, aromatic or halogenated
58PHA