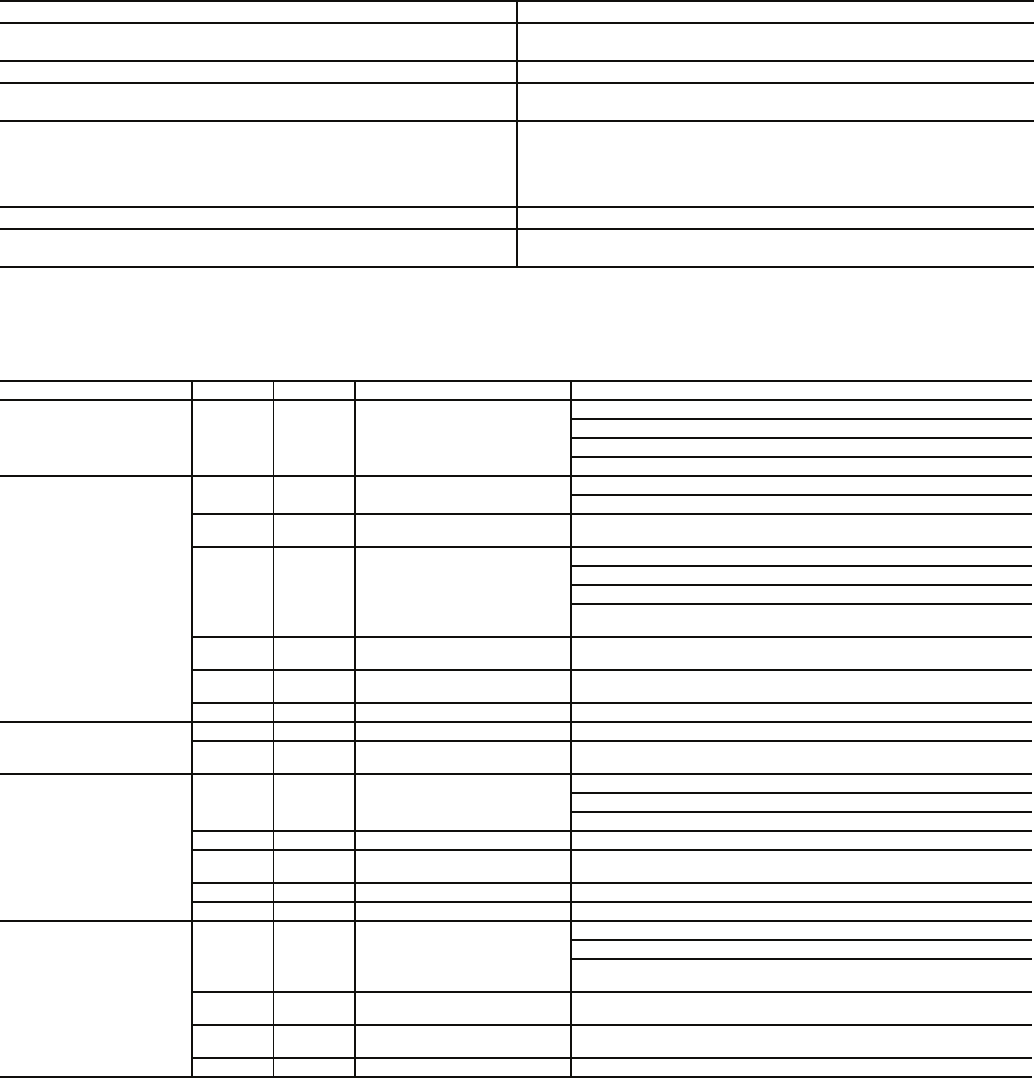
55
Moisture Check — To perform moisture check:
• Check that connectors are orientated “down” (or as recom-
mended by equipment manufacturer).
• Arrange harnesses with “drip loop” under motor.
• Check if condensate drain is plugged.
• Check for low airflow (too much latent capacity).
• Check for undercharged condition.
• Check and plug leaks in return ducts, cabinet.
Table 38 — Good Practices
Table 39 — WSHP Troubleshooting
LEGEND
DO DO NOT
Check motor, controls wiring, and connections thoroughly before replac-
ing motor.
Automatically assume the motor is bad.
Orient connectors down so water cannot get in. Install “drip loops.” Locate connectors above 7 and 4 o’clock positions.
Use authorized motor and control model numbers for replacement. Replace one motor or control model number with another (unless
replacement is authorized).
Keep static pressure to a minimum by:
• Using high efficiency, low-static filters.
• Keeping filters clean.
• Designing ductwork for minimum static and maximum comfort.
• Improving ductwork when replacement is necessary.
Use high pressure drop filters.
Use restricted returns.
Size equipment wisely. Oversize system then compensate with low airflow.
Check orientation before inserting motor connectors. Plug in power connector backwards.
Force plugs.
FAULT HEATING COOLING POSSIBLE CAUSE SOLUTION
Main Power Problems X X Green Status LED Off Check line voltage circuit breaker and disconnect.
Check for line voltage between L1 and L2 on the contactor.
Check for 24 vac between R and C on controller.
Check primary/secondary voltage on transformer.
HP Fault — Code 2
High Pressure
X Reduced or no water flow in cool-
ing
Check pump operation or valve operation/setting.
Check water flow adjust to proper flow rate.
X Water temperature out of range in
cooling
Bring water temperature within design parameters.
X Reduced or no airflow in
heating
Check for dirty air filter and clean or replace.
Check fan motor operation and airflow restrictions.
Dirty air coil — construction dust etc.
External static too high. Check blower performance per
Tables 11-13.
X Air temperature out of range
in heating
Bring return-air temperature within design parameters.
X X Overcharged with refrigerant Check superheat/subcooling vs typical operating condition per
Tables 20-30.
X X Bad HP switch Check switch continuity and operation. Replace.
LP/LOC Fault — Code 3
Low Pressure/Loss of
Charge
X X Insufficient charge Check for refrigerant leaks.
X Compressor pump down at start-
up
Check charge and start-up water flow.
FP1 Fault — Code 4
Water Freeze Protection
X Reduced or no water flow
in heating
Check pump operation or water valve operation/setting.
Plugged strainer or filter. Clean or replace.
Check water flow adjust to proper flow rate.
X Inadequate antifreeze level Check antifreeze density with hydrometer.
X Improper freeze protect setting
(30 F vs 10 F)
Clip JW2 jumper for antifreeze (10 F) use.
X Water temperature out of range Bring water temperature within design parameters.
X X Bad thermistor Check temperature and impedance correlation.
FP2 Fault — Code 5
Air Coil Freeze Protection
X Reduced or no airflow in
cooling
Check for dirty air filter and clean or replace.
Check fan motor operation and airflow restrictions.
External static too high. Check blower performance per
Tables 11-13.
X Air temperature out of range Too much cold vent air. Bring entering air temperature within design
parameters.
X Improper freeze protect setting
(30 F vs 10 F)
Normal airside applications will require 30 F only.
X X Bad thermistor Check temperature and impedance correlation.
LED — Light-Emitting Diode
RV — Reversing Valve
TXV — Thermostatic Expansion Valve