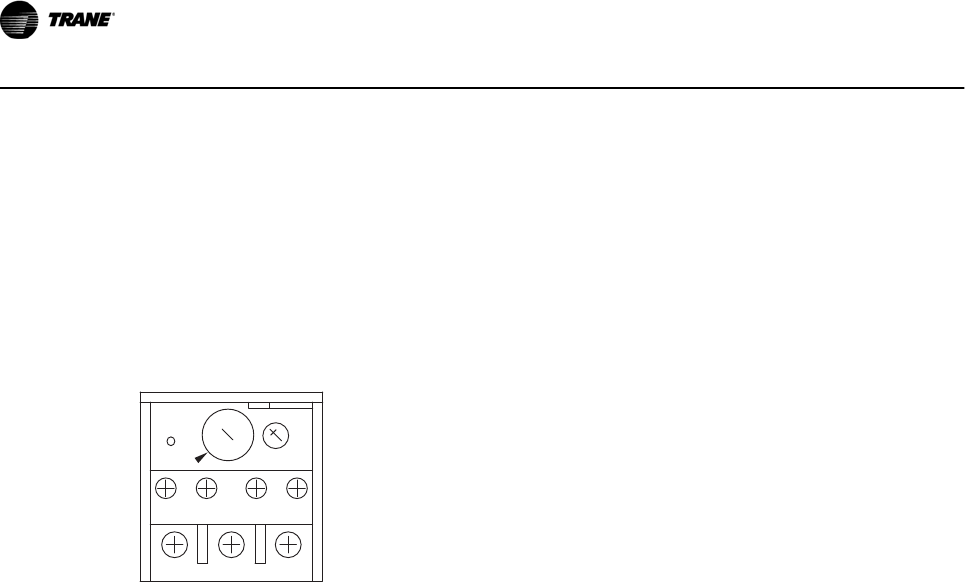
Operation
Overloads and motors are both rated by class. The class is
defined by the NEC to determine the maximum time to
trip. A Class 20 overload, for example, has a typical trip
delay of 20 sec. or less at 600% current and normal
operating temperature. This allows for high motor inrush
current for 20 sec. while the motor is ramping up to
synchronous speed. The trip time, however, is based on
the percentage of overload. The higher the overload, the
shorter the time.
T1
T2 T3
97NO
98NO 95NC
96NC
10
20
30
RESET
TEST
MANUAL
AUTO
TRIP
5
130BX229.10
Figure 6.5 Sample Overload Device
Overload Function Setup
•
Set the overload current dial to the FLA of the
motor. DO NOT add the service factor of the
motor into the setting. A service factor of 1.2 x
FLA is designed into the overload.
•
Pressing the test pushbutton verifies the
operation of the overload. The overload should
trip when pressed. Use the reset pushbutton to
reset the overload after testing.
•
Reset is used to reset the overload after it trips. If
the overload is still hot, wait until the motor
reaches normal operating temperature before
resetting. The overload offers a manual (hand) or
auto reset selection. It is highly recommended to
operate in the manual factory setting to prevent
the risk of damage to the motor.
6.1.11 ECB Safety Interlock
General Information
The safety interlock feature prevents the drive or bypass
from operating. Only a fire mode command to run
overrides this function. For operation in drive or bypass
mode, the safety external interlock input contact must be
closed. External inputs include, but are not limited to, high
and low pressure limit switches, fire alarm, smoke alarm,
high and low temperature switches, and vibration sensors.
Operation
When an external safety input closes on ECB terminals 1
and 2 on connector X57, the option panel is in operational
mode. When open, power to the motor is disabled. The
bypass ignores all run commands except for fire mode
operation, when applicable. The drive display indicates
alarm 221, bypass interlock, meaning the problem is
external to the drive. A factory installed jumper between
X57 terminals 1 and 2 allows the unit to operate when no
safety input is connected. This jumper must be removed
when connecting in a safety interlock circuit.
Safety Interlock Function Setup
•
Remove factory-installed jumper between ECB
connector X57 terminals 1 and 2 on drive control
terminals.
•
Wire safety input to connector X57 terminals 1
and 2.
•
For technicians familiar with connecting to drive
terminals 12 and 27 for safety interlock, be aware
that ECB bypass operation will NOT stop with the
external fault report. Use terminals 1 and 2 on
connector X57, as indicated, for bypass control.
6.1.12 ECB Common Run/Stop
General Information
The common run/stop function provides remote run and
stop control of the motor while in either drive or bypass.
Without common run/stop, the motor would automatically
run at full speed whenever the bypass is activated. The
remote signal provides drive control as well as bypass
control, making this one input common to both. Common
run/stop is enabled by factory default. When used with the
run permissive function, common run/stop permits run
request operation in bypass.
Operation
A user supplied remote run command wired to drive
terminals 13 and 18 initiates remote drive or bypass
operation. Common run/stop can also be activated by
hand on the keypad or through serial communication.
Operation in either drive or bypass is determined by drive
or bypass mode selection, not the run/stop command.
Prior to Enabling Common Run/Stop
•
Complete the start-up procedure to verify motor
rotation direction in bypass is correct and that
the system is ready in all respects for continuous
full speed operation in bypass.
Common Run/Stop Setup
•
Wire a remote run/stop to drive input terminals
13 and 18 (default run input). Ensure that
parameter 18 is programmed for run (default
setting).
Electronically Controlled B...
6-12 BAS-SVX49A-EN