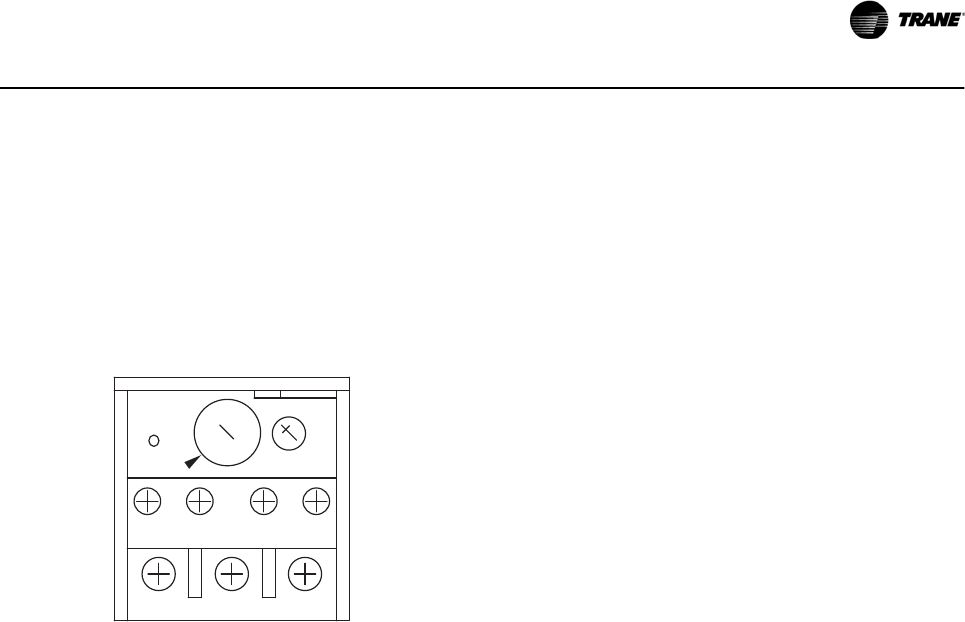
trip when pressed. Use the reset pushbutton to
reset the overload after the test.
•
Reset is used to reset the overload after it trips. If
the overload is still hot, wait until the motor
reaches normal operating temperature before
resetting. The overload offers a manual (hand) or
auto reset selection. It is highly recommended to
operate in the manual factory setting to prevent
the risk of damage to the motor.
T1
T2 T3
97NO
98NO 95NC
96NC
10
20
30
RESET
TEST
MANUAL
AUTO
TRIP
5
130BX229.10
Figure 5.2 Sample Overload Device
5.1.6 EMB2 Safety Interlock
General Information
The safety interlock feature prevents the drive or bypass
from operating. For operation in drive or bypass, the safety
interlock input contact must be closed. Only a fire mode
command to run in bypass overrides this function. Safety
inputs include, but are not limited to, high and low
pressure limit switches, fire alarm, smoke alarm, high and
low temperature switches, and vibration sensors.
Operation
When an external safety input closes, the panel is in
operational mode. When open, power is interrupted to the
drive output and bypass contactors and relays, and the
bypass ignores all run commands except for fire mode
operation. When power is interrupted in drive mode, the
drive display indicates an external fault, meaning the
problem is external to the drive. In some instances, a fault
can be caused by a failure within the panel, which will still
be reported as an external fault from the drive. A factory
installed jumper allows the unit to operate when no safety
input is connected. This jumper must be removed when
connecting a safety interlock in the circuit.
Safety Interlock Function Setup
•
Remove factory-installed jumper between
terminals 5 and 6 on connector X55
•
Wire safety input to terminals 5 and 6 on
connector X55
5.1.7 EMB2 Fire Mode
General Information
Fire mode runs the motor at full speed in bypass and is
intended to ignore common safety, overload, and mode
selector switch inputs in emergency situations. The motor
will continue to run in bypass until fire mode is removed
or the unit fails.
Prior to Enabling Fire Mode
•
Complete the start-up procedure to verify motor
rotation direction in bypass is correct and that
the system is ready in all respects for continuous
full speed operation in bypass.
Operation
•
Activation of fire mode is accomplished by
closing connector X55, input terminals 7 and 8.
•
When activated, a relay overrides the safety
circuit, motor overload, and bypass switch (SW1)
position.
•
Fire mode is deactivated only when removed or
fuses blow.
•
Fire mode status can be reported through
connector X55, terminals 9 and 10, a normally
open dry contact that closes when fire mode is
active.
Fire Mode Function Setup
•
Wire the fire mode input to connector X55,
terminals 7 and 8.
•
Wire the fire mode status output to connector
X55, terminals 9 and 10.
5.1.8 EMB2 Fault Reporting
General Information
A fault indication is provided if the drive experiences a
fault or bypass input power is lost. The EMB2 bypass
control card monitors the drive fault output for status
reporting. The fault contacts are fail-safe, meaning that if
power is removed, a fault condition is automatically
reported. Fault status is not monitored in bypass
operation.
Operation
For the EMB2, fault reporting is monitored through a
Form-C relay (RL2) on the bypass control board. The relay
reports a fault on connector X59 terminals 5, 6, and 7. In
normal operation, the relay is powered and terminal 5 is
closed with terminal 7 open. In a fault condition, power to
the relay is lost and the relay positions automatically
reverse, signaling the fault condition. Terminal 6 is
common to both.
Electromechanical Bypass (EMB2) Operation
BAS-SVX49A-EN 5-5