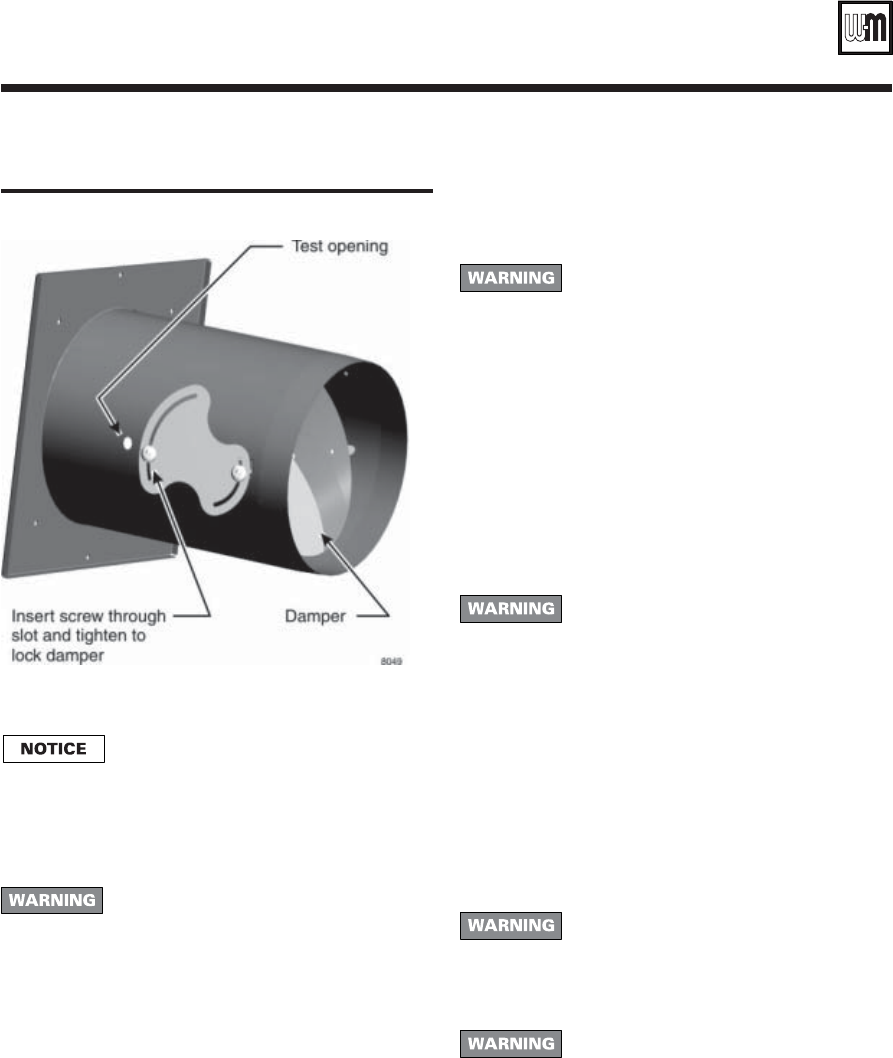
• Installation • Start-Up • Maintenance • Parts
33Part No. 550-141-935/0602
Make final adjustments (continued)16
Figure 35 Flue damper assembly, typical
Skim steam boilers:
Clean all newly installed steam boilers to
remove oil. Failure to properly clean can
result in violent water level fluctuations,
water passing into steam mains, or high
maintenance costs on strainers, traps and
vents. Skim boiler only. Do not clean old
piping or leaks can occur.
Do not use petroleum-based cleaning or
sealing compounds in boiler system.
Severe damage to system components can
result, causing substantial property
damage.
1. Remove 1½" plug from skim tapping tapping “
A” –
Figure 28, page 29). Provide 1½" skim piping from
tapping to floor drain (pipe to side of boiler).
2. Raise waterline to midpoint of skim piping.
3. Fire burner to maintain temperature below steaming
rate during skimming process.
4. Feed in water to maintain water level. Cycle burner to
prevent rise in steam pressure.
5. Continue skimming until discharge is clear. This may
take several hours.
6. Drain boiler. While boiler is warm
but not hot, flush
all interior surfaces under full pressure until drain water
runs clear.
7. Remove skim piping. Re-insert plug at boiler skim
tapping.
8. Close drain cock. Fill with fresh water to normal water
line. Start burner and steam for 15 minutes to remove
dissolved gases. Stop burner.
9. Check traps and air vents for proper operation.
Determine if water treatment is needed
(water boilers only):
Do not use petroleum-based cleaning or
sealing compounds in boiler system.
Severe damage to system components can
result, causing substantial property
damage.
Continual make-up water will reduce boiler life. Minerals
can build up in sections, reducing heat transfer, overheating
cast iron and causing section failure.
For unusually hard water areas or low pH conditions (less
than 7.0) consult local water treatment company.
Freeze protection (when used):
1. Use antifreeze especially made for hydronic systems.
Inhibited propylene glycol is recommended.
Do not use automotive, ethylene glycol or
undiluted antifreeze. Severe personal
injury or death can result.
2. 50% solution provides protection to about -30°F.
3. Local codes may require back-flow preventer or actual
disconnect from city water supply.
4. Determine quantity according to system water content.
Boiler water content is listed on page 34. Percent of
solution will affect sizing of heat distribution units,
circulator and expansion tank.
5. Follow antifreeze manufacturer's instructions.
Check boiler for gas-tight seal:
Boiler must be sealed gas-tight to prevent
possible flue gas leakage and carbon
monoxide emissions, resulting in severe
personal injury or death.
1. Remove boiler jacket side and top panels.
The boiler contains ceramic fiber and
fiberglass materials. Use care when
handling these materials per instructions
on page 38 of this manual. Failure to
comply could result in severe personal
injury.
2. Start burner. Observe all sealing points and chalk mark
any not gas-tight.
3. To seal all chalk-marked areas:
a. use silicone sealant on section flueways.
b. check gaskets and sealing rope placement.
4. Reinstall all jacket panels.