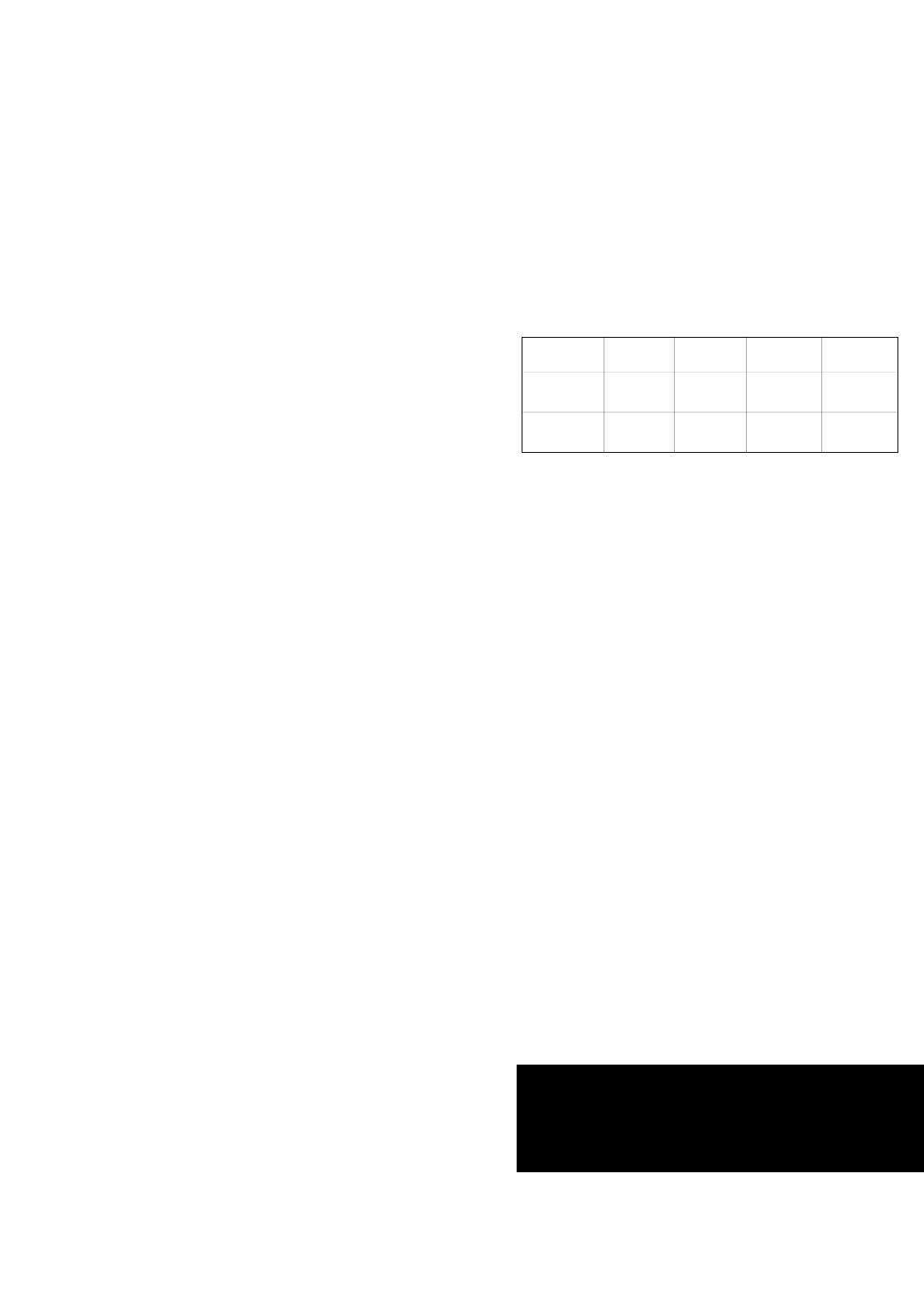
15
4. Check gas manifold for proper position and reassemble
burners to the manifold. Line up holes in burners with the ori-
fices, and slide assembly back into position. Be sure to rein-
stall burners with burner ports on the top surface
(upright).
5. When a low water cut-off has been utilized, follow the
manufacturer’s maintenance instructions. As a minimum, test
the operation of electronic controls at least once a year.
Remove, clean and inspect the probe. Float type controls
should be flushed once a month during the heating season. If
LWCO fails to operate properly; it must be replaced.
6. Follow "System Start-Up & Adjustments" procedures in
Section 3 of this manual.
STEAM BOILER CLEANING INSTRUCTIONS
The following procedures must be followed on initial start-up
and if the presence of sediment, sludge or impurities hamper
proper boiler operations.
1. With gate valves closed on supply and return lines, start
burner and allow boiler to become pressurized so that the pres-
suretol may be adjusted and set for limit cut-off desired (nor-
mally about 3 psi). Turn off burner and allow pressure to drop to
0 psi., then proceed with the following cleaning procedure.
2. Remove the pressure relief valve.
3. Add caustic soda (lewis lye) through this opening at the
rate of one pound per thousand square feet of radiation
capacity. Scout, Squirk or similar steam boiler cleaners may
be used instead of lye. Trisodium phosphate (1/4#) is also an
excellent cleaner.
4. Provide pipe connection (full size) from pressure relief
valve opening to a convenient drain to serve as a vent.
5. Fill the boiler with a manual fill valve until water starts to
trickle from this pipe.
6. Fire boiler at sufficient rate to generate and maintain
steam. Entrain water and impurities will then discharge (with
steam) from open vent. Add water as necessary so that the
low water cutoff does not shut off burner.
7. Continue this process for a minimum of one hour. The process
should continue until the steam is dry (no water coming from the
vent when the water in the gauge glass is at a normal level,
approximately 2/3 full). The time required could vary up to 3 hours.
8. Turn gas valve to off position. While boiler is still hot, drain
completely through boiler drain. Make sure that all low points
in the return line are also completely drained. These areas
could trap chemicals and dirt.
9. Close boiler drain and refill with clean untreated warm
water. If warm water is not used, fill very slowly so as not to
crack boiler sections. Fill until water overflows through vent
pipe and runs clear.
10. Completely drain boiler again.Refill with clean untreated
water to normal level.
11. Remove vent drain piping and reinstall pressure relief
valve. Open gate valves on supply and return lines. Turn on
burner. System is now ready to operate.
HOW TO CHANGE ORIFICES
1. Shut off power supply and gas supply to the boiler.
2. Remove burner access panel. Lift burners up and to rear
until burners are disengaged from orifices.
3. Check orifices for proper drill size. Size is stamped onto
the body of the brass orifice (see Figure 4.1). Size can also
be checked by using a pin gauge.
4. All orifices are screwed into the manifold and may be
removed by using a 5/8" wrench or socket.
5. Reverse procedures above to install orifices and burners.
Be sure to reinstall burners with burner ports on the top
surface (upright).
HEATING SYSTEM PROBLEMS & CAUSES
No Heat
1. Blown fuse or circuit breaker.
2. Switch turned off.
3. Pilot outage
4. IID system malfunction.
5. Flue damper not open.
6. Water level too low.
Odor, Excessive
Moisture In Building
1. Leak in piping.
2. Carbon build-up in flueways.
3. Blocked chimney.
Noise
1. Ignition or ignition noise
due to incorrect air shutter
adjustment.
2. Whistle due to burr on
orifices.
3. Burner "fluteings" due to air
shutter opening too wide.
FIGURE 4.1: GB200 ORIFICE SIZES
Boiler
Model
GB200-3 GB200-4L GB200-4H GB200-5
(1) Nat. Gas
Drill Size
(2) Prop. Gas
Drill Size
41 41 37 38
53 53 52 52
CAUTION: Label all wires prior to disconnection
when servicing controls. Wiring errors can cause
improper and dangerous operation.
Verify proper operation after servicing.
Insufficient Heat
1. Incorrect thermostat
anticipator setting.
2. Low pressuretol setting.
3. Boiler undersized or
underfired.
4. Insufficient radiation.
Yellow Flame,
Carbon Build-Up
1. Unit overfired.
2. Air shutter misadjust-
ment.
3. Wrong orifices.
4. Burning in burner mix-
ing tube.
Overheating
1. Wrong thermostat
anticipator setting.
2. Bad thermostat
location.
3. Bad thermostat.