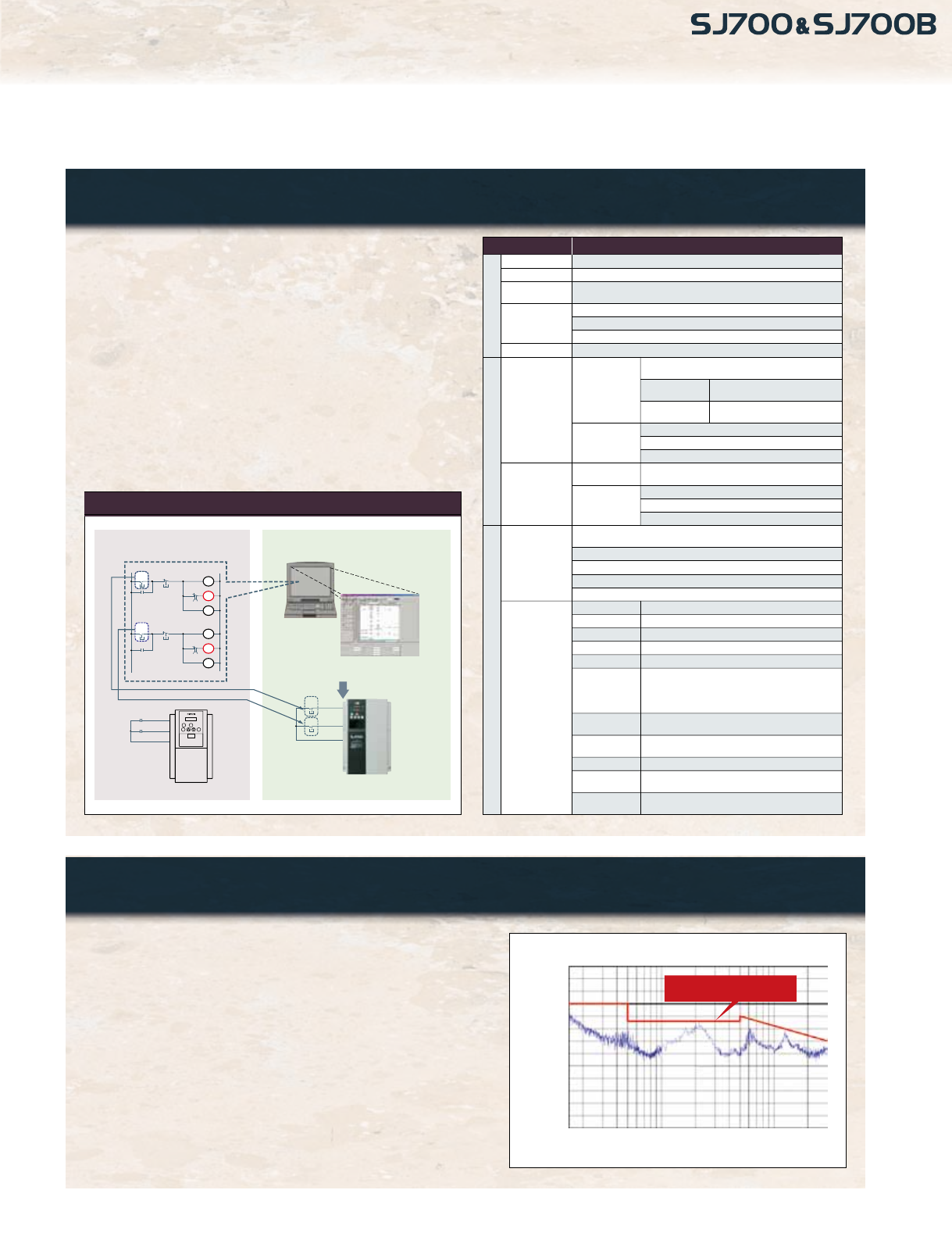
Possible with SJ700 Series
High performance, powerful functions,
yet user friendly.
Inverter control by Built-in
Programming function
Sequence operation is realized by downloading to an inverter a
program created with Hitachi's EzSQ software.
Tailor inverter operation to meet changing process
requirements, and replace separate PLCs in some cases.
By simplifying or eliminating external hardware, signficant cost
savings can be achieved.
Password function is incorporated to provide security for
proprietary program data against loss or unauthorized
modification.
Built-in EMC Filter up to 150kW
*
Cost and space reduction compared with external EMC Filter.
Reduces electromagnetic noise.
Meets EN61800-3 2nd-Environment
*
SJ700: European Version and Japanese Version does not have 150kW
SJ700B: All models
Brake circuit up to 22kW
*
Cost and Space reduction compared with external Braking
Controller.
*
SJ700B: Up to 30kW
EMC Filter & Brake circuit integrated as Standard
Programming [EzSQ: Easy Sequence] function
Example (SJ700-110HFEF2)
Frequency [Hz]
Level [db]
Typical Example - Replacing External Relay Circuit
Item Description
Language SpecI/O functionReserved word
Language type BASIC Like
Supported Device
Windows(DOS/V)OS:Windows2000, WindowsXP)
Programming
environment
Editor(Windows), Display(Windows)
Programmable flow control <Loop, Unconditional jump, conditional jump,
Time control, Sub routine, Others>
Operation command <+,-,,*, /, substitution, mod, abs>
I/O control(Bit input, Word input, Bit output, Word output)
Timer control <on delay, off delay>
Inverter parameter setting
User U(00)-U(31)/32 point
Timer UL(00)-UL(07)/8 point
Set frequency SET-Freq
Acceleration time
ACCEL
Deceleration time
DECEL
Monitor
Output frequency, Output current, Rotative direction,
PID feedback, Converted frequency, Output torque,
Output voltage, Power, Cumulative RUN time,
Cumulative power-on time, trip
General-purpose
input contact
X(00)-X(07)/8 point
General-purpose
output contact
Y(00)-Y(05)/6 point(1 point is relay output)
UB(00)-UB(07)/8 pointInternal user
TD(0)-TD(7)/8 point
Internal timer
contact
In a remote operator display code.
Inverter input
and output
Grammar check(Windows)
Program download/upload, All clear
Interpreter 2.0ms/command (Sub routine supported. 8 nested)
Memory area
Executable format
External input
External output
Command
Variable
1,024 steps or 6k byte
(Smaller of these)Program is stored in internal of inverter.
External digital
contact input
External analog
input
General-purpose
output terminal
Contact signal/Open collector signal input
(Internal DC24V power supply available)
Program RUN
command
FW terminal is reserved
General-purpose
input
Maximum of 8 point(X(00)-X(07))
XA(0) : 0-10V (O terminal)
XA(1) : 4-20mA (OI terminal)
XA(2) : 0-10V (O2 terminal)
External analog
output
YA(0) : Setup for FM terminal is possible.
YA(1) : Setup for AM terminal is possible.
YA(2) : Setup for AMI terminal is possible.
Maximum of 8 point(Y(00)-Y(05))
QP: Quasi Peak
*
Windows
®
is a registered trademark of Microsoft Corporation.U.S.A and other countries.
130
120
110
100
90
80
70
60
50
40
30
20
10
0
150k 200k 500k 1M 2M 5M 7M 10M 20M 30M
Over-current suppress ON
Suppresses over current and continues running
Impact load
Motor current
Voltage of the
main circuit DC
Output frequency
High starting Torque,
Powerful Drive and easy setting
High starting Torque
Trip avoidance function
Over current &
voltage suppress function
Improved Sensorless Vector Control and Auto Tuning
produce high starting torque of 200% or more at 0.3Hz.*
1
Easy setup of motor constants
Ideal for applications which need high torque, such as
cranes, extruders and lifts.
Higher internal calculation speed improves current control
performance.
Over-current suppress and Over-voltage suppress functions
avoid inverter trip during acceleration and deceleration.
Hitachi exclusive
0Hz Domain sensorless
vector control
Develops 150%(SJ700B:120%)
*
2
torque at
0Hz speed reference
Ideal for cranes and other applications
that require high torque at starting.
*
2
when inverter is one frame size larger than motor.
Position Control Function
The SJ700, with optional feedback board installed, together
with an encoder-equipped motor can perform position control.
For many applications, suitable performance can be
achieved at a lower cost than servo systems.
Based on your four motion parameters (position command,
speed command, acceleration time and deceleration time),
the SJ700 will move an object from original position A to
target position B.
After the movement,
the inverter keeps servo
lock status.
DC Bus AVR Function
During Deceleration
The SJ700 controls deceleration time so that the DC bus
voltage does not exceed the over-voltage trip level, providing
trip-less operation during deceleration.
Motor Torque vs. Speed
Torque [%]
Speed (min
-1
)
200
100
0
-100
-200
300 600 900 1200 1500 1800
0.3Hz
Starting point A
Target point B
EN61800-3 2nd Envinment
[C3]QP Limit Level
Over-current suppress OFF
OC-Trip
Frequency
Motor current
Standard Inverter SJ700 Using EzSQ
EzSQ
Programming
Programming Window
Download
SJ700
Series Applicable motor
SJ700B
0.4 to 55kW
75 to 132kW
185 to 400kW
11 to 75kW
90 to 160kW
Starting torque
0.3Hz/200%
0.3Hz/180%
0.3Hz/150%
0.5Hz/150%
0.5Hz/120%
*1Starting torque
*
)
*
)
*
) Derating is applied for SJ700B. Please consult technician at Hitachi or its distributor before use.
For More Precise Control For General Purpose Use
Series
Line up
S
J
700
S
J
700B
1 2