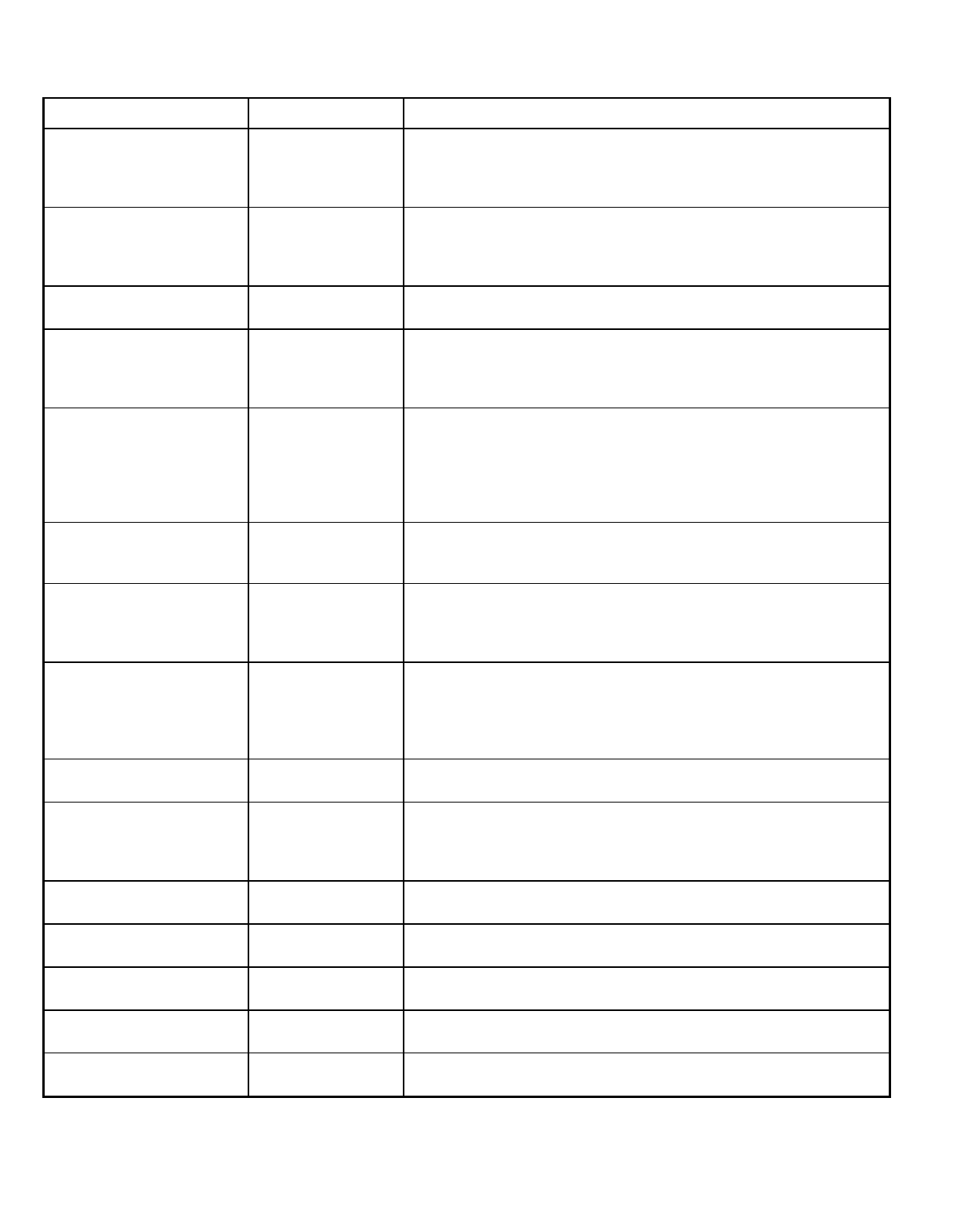
684025 15
Troubleshooting Chart
PROBLEM CAUSE SOLUTION
System will not run or
stops while running.
Air pressure or air
volume is too low.
Increase air pressure. Check air compressor and air supply filters
re
g
ulator, lubricator valves and other components for blocka
g
es
and restrictions. If this is a new system, be sure that air supply
components have been sized properly.
The fluid valves or
hoses are closed or
restricted.
Check the
g
un, fluid hoses, mix manifold, static mixer, fluid filters,
re
g
ulators, valves and other fluid line components for blocka
g
es
and restrictions. If this is a new system, be sure that the fluid
components have been sized properly.
The air motor is
worn or damaged.
Service the air motor. See “servicing the Air Motor” on page 17.
The displacement
cylinder(s) is
damaged or has
seized
See troubleshootin
g
techniques below to isolate the problem
cylinder. See “Service the cylinders” on page 16.
The fluid pressure
bounces significantly
(>500 psi) while pump is
running
Air volume is too
low.
Verify that air pressure at the air motor inlet is not droppin
g
durin
g
pump chan
g
eover. Check air compressor and air supply filters
regulator, lubricator valves and other components for blockages and
restrictions. If this is a new system, be sure that air supply
components have been sized properly. 1” NPT hoses, fittin
g
s and
accessories are required to provide the necessary air volume.
Feed pump
pressure is too
high.
Reduce feed pump pressure. Feed pump pressures must be less
than 25% of proportioner output pressure.
The displacement
cylinder(s) check
valves are not
seating.
See troubleshootin
g
techniques below to isolate the problem
cylinder. See “Service the cylinders” on page 16.
Mix ratio test is
significantly different from
the mix ratio setting.
Mix ratio test was
not performed at
the normal
operating pressure
of the pump
Perform ratio test again following ratio test procedure on page 12.
Running out of one
material.
Check and refill material reservoirs. Repeat the test after the air has
been removed from the system.
The displacement
cylinder(s) are worn
or the check valves
are not seating.
See troubleshootin
g
techniques below to isolate the problem
cylinder(s). See “Service the cylinders” on page 16.
Spray output is spitting Runnin
g
out of one
material.
Check and refill material reservoirs. Remember that once air is in
the fluid system it may take a while for all of it to escape..
Siphon hoses are
leaking in air.
Ti
g
hten and seal all siphon fittin
g
s on proportionin
g
pump and feed
pumps.
A squeaking or knocking
noise is heard.
The bearin
g
s are
dry or worn.
Lubricate the bearin
g
s or replace them if required. See “service the
bearings” on page 18.
The proportioner speeds
up or runs erratically
Runnin
g
out of one
material.
Check and refill material reservoirs.
The cylinders are
worn or damaged.
See troubleshootin
g
techniques below to isolate the problem
cylinder(s). See “Service the cylinders” on page 16.