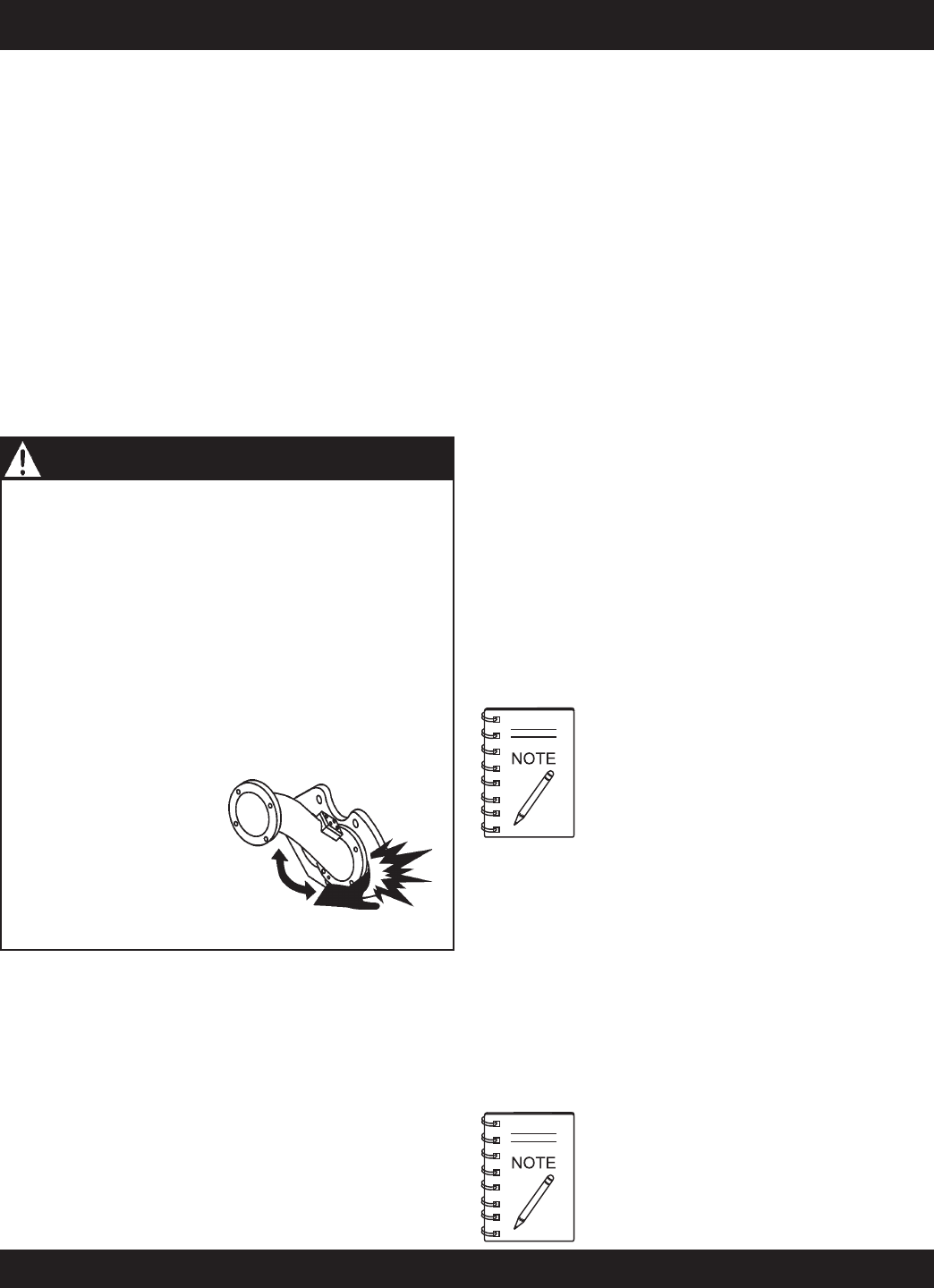
MAYCO LS400/LS500 PUMP — OPERATION AND PARTS MANUAL — REV. #6 (09/19/11) — PAGE 41
LS400/LS500 PUMP — MAINTENANCE (PUMP)
CYLINDER CUP REPLACEMENT PROCEDURE
1. Remove the two hydraulic hoses connected to the remix
motor. Plug the ports with fittings (not provided) to
prevent hydraulic hose leakage.
2. Remove the hopper discharge nipple and loosen sleeve
seal. Inspect and replace if wear is excessive.
3. Remove the two tie rod nuts and the four eyebolt nuts
securing the hopper to the pump frame.
CHANGING THE CONCRETE CYLINDER PISTON CUPS
The Rubber piston cups will occasionally require replacement
depending on the following factors.
■
The fluid level and cleanliness of the lubrication box.
■
The size and type of aggregate.
■
The type of concrete being pumped.
It is time to replace the cups when increasingly large particles
of sand and cement pass into the lubrication box. Do not
allow the cups to become so worn that they begin to pass
lubrication into the material cylinders. If the liquid level of
the lubrication box becomes to low, the rubber cups will
severely deform due to excessive heat. Whenever
replacement is due, both cylinder cups should be replaced.
Before installing 3/8” bolt, coat the back of
bolt heads with silicon sealant. Torque all three
bolts equal at 55 ft. lbs. each.
Felt ring must be saturated with 30 wt. oil
prior to installation.
10. Install the felt holder over the oiler plate. Install felt ring
into felt holder. Install the bronze ring.
11. Using silicon sealant place a small bead of sealant
material on the front of the rubber piston cup and the
rear of the face plate. Install over alignment studs and
into concrete cylinders.
12. Insert one 3/8” 16x3” bolt into the open bolt hole, remove
the alignment studs one at a time and install the
remaining 3/8” 16x3” bolts.
4. Using an approved lifting device, remove the hopper
using extreme care not to damage the hopper seal.
5. Start the engine and turn on the pressure test switch.
Cycle pump in reverse until hydraulic system obtains
maximum pressure, then turn pump and engine
off.
Remove ignition key and disconnect battery. Think
safety! Check the hydraulic gauges on panel and make
sure accumulator pressure reads zero. One piston
should be in the fully discharged position at the end of
the concrete cylinder.
6. Remove the three 3/8 – 16 x 3” bolts from the piston.
Remove the front faceplate.
7. Install two the 3/8’ 16x3” bolts back into the piston –
do not tighten. Use the two bolts as leverage to remove
the rubber piston cup and rear components.
8. Obtain two 3/8 16x7” full thread studs (these studs will
be used to assist in assembly alignment) insert the
two studs into the piston adapter. Coat the concrete
cylinder with grease.
9. Install the “O” Ring around the oiler plate. Install the
plate into the concrete cylinder utilizing the studs for
alignment.
During routine maintenance or removing material
blockage, you will be required to put your hand in the
concrete cylinders or near the shuttle tube. You are at
EXTREME RISK
of injury or
AMPUTATION
if the
engine is running or if pressure is in the hydraulic
system.
Prior to performing any maintenance on the pump,
follow described lock out-tag out procedures. Stop the
engine by turning off the ignition switch and remove
the starter key. Place a “DO NOT OPERATE” tag
over the switch and disconnect the battery. The
pressure reading on the
accumulator pressure
gauge
MUST
read
ZERO. ALWAYS make
sure the accumulator
circuit pressure reads
zero prior to performing any maintenance on the pump.
DANGER - AMPUTATION RISK