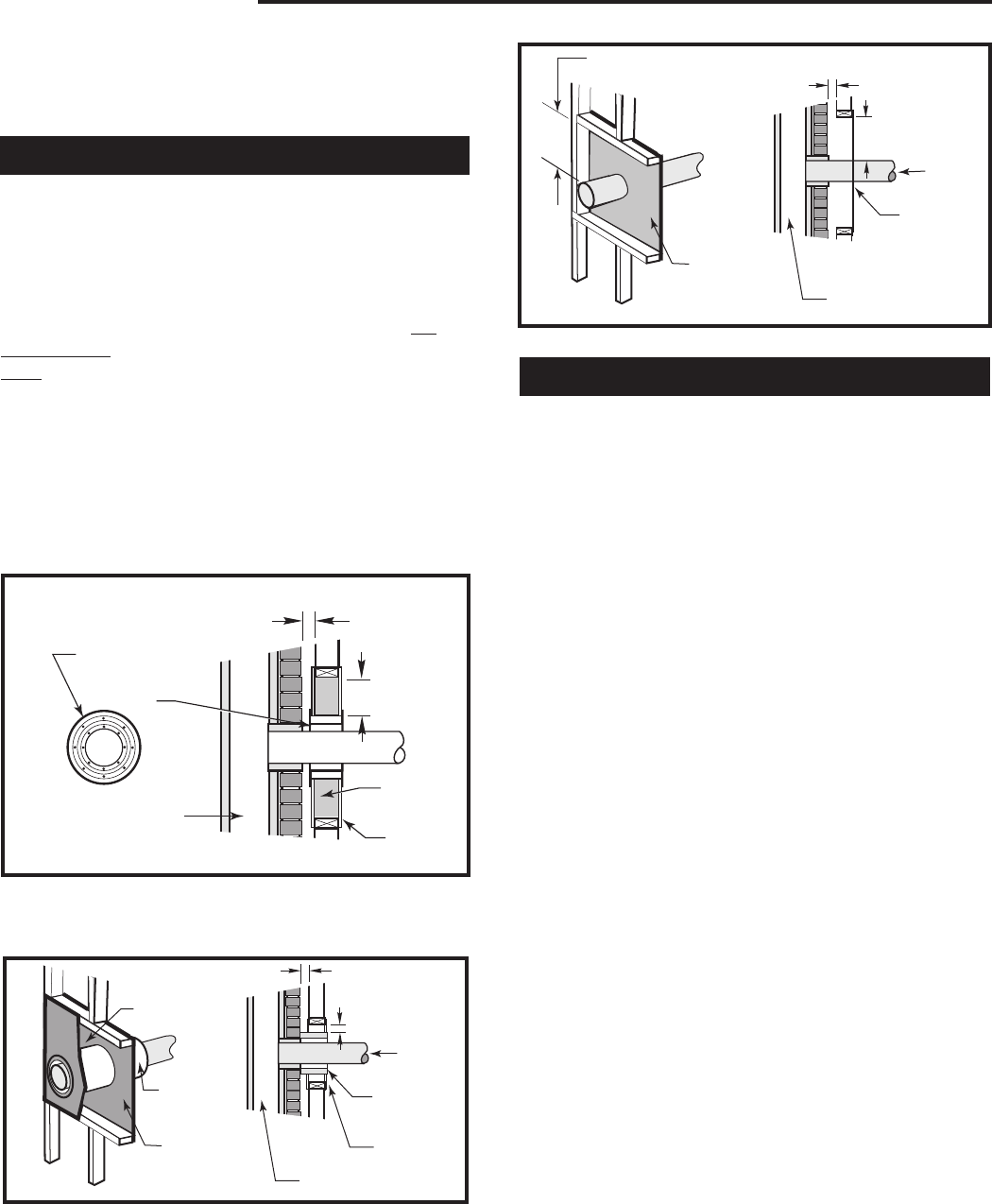
8
Vermont Castings Madison
30001453
Floor Protection
A tremendous amount of heat radiates from the bottom
plate of your Madison. The floor area directly under and
around the stove will require protection from radiant
heat as well as from stray sparks or embers that may
escape the firebox.
Heat protection is provided through the use of a Ver
-
mont Castings Bottom Heat Shield #1892. Spark and
ember protection must be provided by a floor protector
constructed with noncombustible material as specified.
Most installations will require that the bottom heat shield
be attached. Only when the stove is placed on a complete
-
ly noncombustible surface such as unpainted concrete over
earth may it be used without the heat shield.
Even when the bottom heat shield is installed, you must
provide special protection to the floor beneath. For
installations with the heat shield attached, use a non-
combustible floor protector such as 1/4” non-asbestos
mineral board or equivalent, or 24 gauge sheet metal.
The floor protector may be covered with a noncombus-
tible decorative material if desired. Do not obstruct the
space under the heater.
Protection requirements vary somewhat between the
United States and Canada as follows:
For U.S. installations the floor protector is required
under the stove and must extend at least 18” from the
front of the stove (“D”, Fig. 12), at least 4” from the right
side and rear (“C”, Fig. 12) and 16” from the left side
(“E”, Fig. 12). It must also extend under the chimney
connector and 2” to either side (“F”, Fig. 12).
To meet these requirements, a floor protector must be
at least 48” wide (“A”,Fig. 12) and 48” deep (“B”,Fig. 12)
In Canada, a noncombustible floor protector is required
under the heater also. The floor protector must extend
18” (457mm) to the front (D), and 8” (203mm) from the
right side (C) and rear (C) and 18” (457mm) from left
side (E).
ST274
single wall
w/ventilated thimble
12/99
Fig. 9 Wall Pass-through using single wall chimney
connector with a ventilated steel thimble.
Min. 6”
(152mm)
Chimney clearance to sheet steel
supports and combustibles
2” (51mm) Min.
Glass Fiber
Insulation
Chimney Connector
Chimney Flue
Steel Thimble
with two 1”
(25mm) Ventilated
Channels
Masonry Chimney construct
-
ed to NFPA 211
24 ga.Sheet
Steel Supports
ST274
• Placing a chimney connector pipe inside a section of
9” (230 mm) diameter, solid-insulated, factory-built
chimney, with two inches of air space between the
chimney section and combustibles. (Fig. 10)
Canadian Requirements:
In Canada, the Canadian Standards Association has
established specific guidelines regarding wall pass-
though design. Figure 11 shows one approved method
in which all combustible material in the wall is cut away
to provide the required 18” (457mm) clearance around
the connector. The resulting space must remain empty.
A flush-mounted sheet metal cover may be used on
one side only. If covers must be used on both sides,
each cover must be mounted on noncombustible spac-
ers at least 1” (25mm) clear of the wall. Your local
dealer or your local building inspector can provide de-
tails of other approved methods of passing a chimney
connector through a combustible wall.
In Canada, this type of installation must conform to
CAN/CSA-B365, Installation Code for Solid Fuel Burn-
ing Appliances and Equipment.
ST276
CSA approved wall
pass-through
12/99
Fig. 11 CSA approved Wall Pass-through.
24 ga.Sheet
Steel Support
24 ga. Sheet
Steel Support
(one side only)
Min. 18”
(460mm)
Chimney clearance to sheet steel
supports and combustibles
2” (51mm)
Min.
Chimney Flue
Chimney
Connector
Masonry Chimney con-
structed to CAN/CSA-B365
Min. 18”
(460mm)
ST276
ST275
wall with
ventilated
steel thimble
Fig. 10 Wall Pass-through with ventilated steel thimble.
24 ga. Sheet
Steel Supports
24 ga. Sheet
Steel Supports
2” (51mm) Min.
Chimney clearance to sheet steel
supports and combustibles
2” (51mm)
Min.
Chimney Flue
2” (51mm) Min.
air space
Prefab Chim-
ney
Section
Prefab
Chimney
Section
Chimney Con-
nector
Masonry Chimney construct-
ed to NFPA 211
ST275