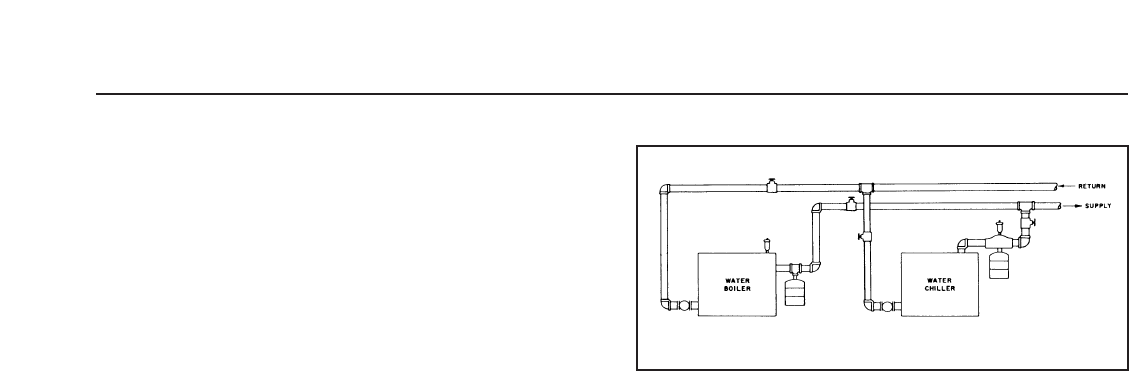
VI
CTORY VSPH Models
19
5. Cold Water Fill
P
ressure reducing (fill) valve and shut-off valve should be
installed.
6
. Relief Valve Discharge Piping
Use same size or larger piping than valve outlet. Must ter-
minate 6" minimum from floor with a plain (no threads)
end. Place a bucket under pressure relief valve discharge.
Make sure discharge is always visible. DO NOT hard-pipe
t
o drain piping.
7. Providing Protection from Freezing
A
nti-freeze is sometimes used in hydronic heating systems
to protect against freeze-up in the event of power failure or
control shutdown when the building is unoccupied. It
should be recognized that unless the building is kept
above freezing temperature by some means, the plumbing
system is not protected. Two types of anti-freeze may be
used: ETHYLENE GLYCOL, used in automobiles, has
desirable properties, but is toxic. Its use maybe prohibited
when system water/glycol solution is in contact with a
potable water vessel (as an indirect hot water heater with
built-in heating coils). PROPYLENE GLYCOL is used in
the quick-freeze food industry; it is practically non-toxic. Its
use may be permitted when system solution is in contact
with a potable water vessel. When anti-freeze must be
used, inhibited propylene glycol is recommended. Useful
information on the characteristics, mixing proportions, etc.
of glycol in heating systems is given in Technical Topics
No. 2A, available from the Hydronics Institute, 34 Russo
Place, Berkeley Heights, NJ 07922. Consult glycol manu-
facturers for sources of propylene glycol.
8. Water Treatment
A good water treatment program will not only extend the
useful life of this boiler but it will also save much of the
time and expense of repairs made necessary by pre-
ventable occurrences. A reputable water treatment compa-
ny should be consulted to evaluate and determine the best
overall treatment program for your boiler equipment.
PIPING A HEATING - COOLING SYSTEM TO A WATER
BOILER AND CHILLER
Figure 18 illustrates a method of piping a heating-cooling sys-
tem to a water boiler and a chiller. Hand valves (shown) or
automatic valves must be installed to prevent circulation of
chilled water in the boiler or hot water in the chiller.
The air control system and pressure control system must
operate with chiller only, or the boiler only, being valved to the
piping system. Separate control devices on the boiler and
chiller may be used, or a single set of air and pressure con-
trols on the common piping may be preferred.
If the boiler is used to supply hot water to heating coils in air
handling units, flow control valves or other devices must be
installed to prevent g
ravity circulation of water in the coils dur-
ing the cooling cycle.
OPERATING INSTRUCTIONS
I. Filling and Venting Water Systems
A. Fill the system with water. Vent or purge of air.
B. Fire the boiler as soon as possible (see following warn-
ing and instructions) and bring water temperature in
the system.
C. Vent air and add water as needed to achieve operating
pressure on boiler gauge. Pressure must be between
approximately 12 psi (cold water) and 25 psi at water
temperature setting of high limit control, for boilers
equipped with 30 psi relief valves. Boilers rated for a
higher pressure and equipped with a matching relief
valve may operate at a higher pressure, but no higher
than 5 psi below the relief valve opening pressure.
D. Check for and repair any leaks before placing system
in service.
BEFORE FIRING BOILER, make these checks:
1. System is full of water. Air is vented or purged.
2. Relief valve is installed in accordance with ASME Boil-
er and Pressure Vessel Code, Section IV. Valve open-
ing is not closed or reduced in size.
3. Venting is installed according to instructions under
“FLUE GAS VENTING REQUIREMENTS”.
4. All wiring is completed, following applicable wiring dia-
grams.
5. Using soap solution, check for gas leaks in all gas pip-
ing from meter to boiler pilot and manifold. DO NOT
use open flame.
Figure 18. Cooling system to a water boiler and chiller.