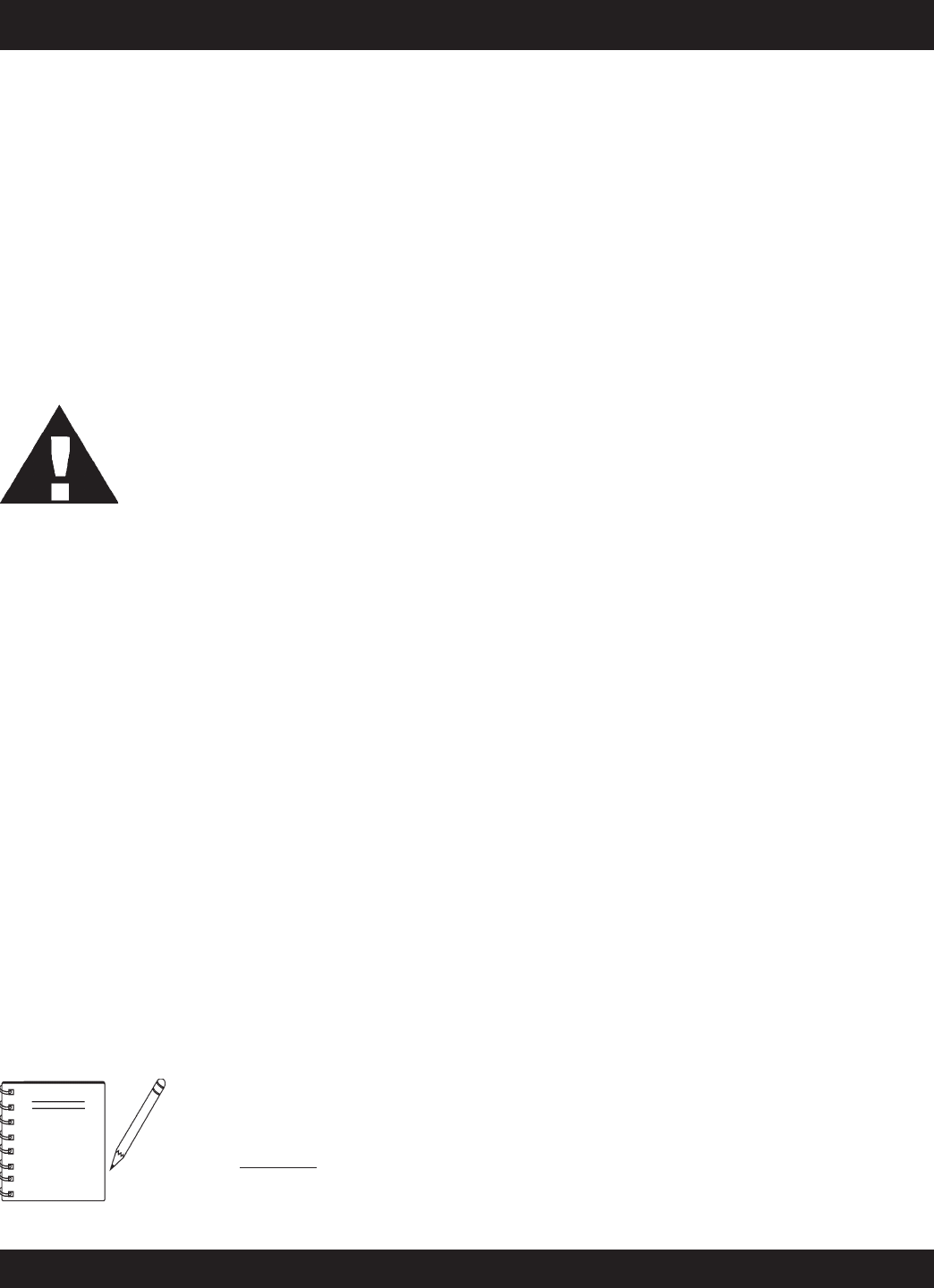
MAYCO ST-45HRM PUMP — OPERATION & PARTS MANUAL — REV. #4 (07/16/04) — PAGE 27
ST-45 PUMP — OPERATING PROCEDURES
18. Down-Hill Pumping – can be difficult on some jobs. The
slurry procedure would be the same as explained on the
pages titled Operating Suggestions. It is suggested that a
sponge 2”x 4”x 6” be placed in the hose before the start of
pumping. Wet the sponge before placing it in the hose.
The reason for using the wet sponge is to keep the slurry from
running too far ahead of the concrete and so reducing the
possibility of separation. When the pump is stopped, the
material can flow slowly down, due to gravity, and cause the
hose to collapse.
When pumping is resumed, you can expect blockage at the
point of hose collapse. To prevent this from happening, the
hose can be “kinked off” at the discharge end when the pump
is stopped to prevent the gravity flow of the material in the
hose.
The use of stiffer mixes when pumping down-hill will de-
crease gravity flow of the material in the hose and will assure
a smoother operation between the cam roller bearing and
cam plate. As with any job, make sure that the hose and the
couplings are in good workable shape.
19. Vertical Pumping – When pumping vertically up the side of
a building, above 40 feet, we would recommend the instal-
lation of
steel pipe
securely fastened at intervals as necessary
to support the pipe. Ninety degree, long radius pipe sweeps
should be installed at the top and bottom of the steel line.
If, for any reason, the mix should set up in the system, the
following procedure (
E through H
) is suggested:
E. Disconnect the hose from the pump and wash the pump
out immediately.
F. Reconnect the hose and fill the hopper with water.
G. Reconnect the hose and fill the hopper with water. DO
NOT try to push all the concrete out of all of the hose
lines at one time.
For example: If you had 200 ft. of system out, you would
disconnect each hose. Clean it out by pushing water
through the first hose off the pump, then continue
progressing through all the hoses, until all the system
is clean.
H. If waiting time is excessive, it would be wise to wash out
the pump and hoses and start over when the new truck
arrives. This can be avoided by being observant to the
pump and system, also taking into consideration the
above factors (E through H) affecting the mix.
WARNING
17. If it is necessary to wait 1/2 hour or more for another load
of concrete, and to prevent setting of the mix in the system,
it is advisable to consider the following factors
(
A through
D
) affecting the concrete :
A. How old is the concrete?
B. Is there an accelerator, calcium chloride, red label, etc.,
in the concrete?
C. The temperature of the day, 80, 90, degrees?
D. How much system you have out and how stiff was the mix
you were pumping?
When disconnecting hoses, use
EXTREME CAUTION! The hose is
under
pressure!
NOTE
Make sure the accumulator pressure gauge
reads ZERO psi. prior to performing any
maitinance or inspection.
D. Carefully knock the end of the hose away from the
reducer.
E. Chip the concrete out of the reducer with the pry bar.
F. Remove the reducer. From the discharge end,
chip the concrete out of the shuttle tube with the pry-bar.
If concrete cannot be loosened from the outlet of the
shuttle tube, remove the clean-out plug on the bottom
of the hopper to discharge the concrete.
G. The senior operator may then remove the inspection
cover plate from the shuttle tube by using a long
extension wrench and the 24" pry bar.
H. Chip the blockage out with the pry-bar.
I. Flush the shuttle tube with water.
J. Replace and seal the inspection cover plate on the
shuttle tube.
K. Before resuming operation of the pump, perform the
“Reverse” Pumping Procedure to relieve pressure on
the shuttle tubes.