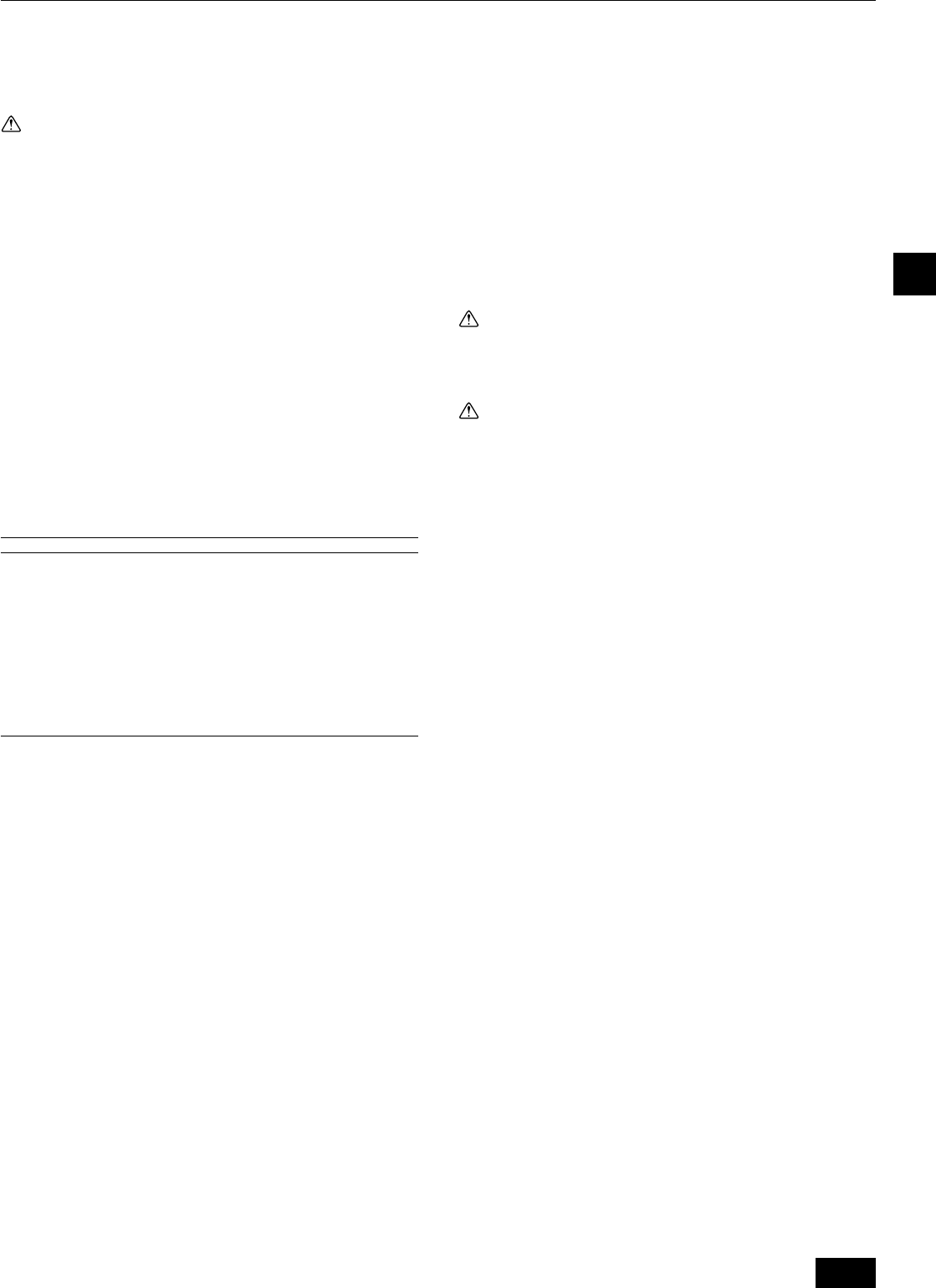
9
DFEINLPGRRUTRCZSVSLHGPO
GB
8. Refrigerant piping installation
The pipe is connected via a terminal-branch type connection in which refrigerant
piping from the outdoor unit is branched at the terminal and is connected to each
of the indoor units.
The method of pipe connection is as follows: flare connection for the indoor units,
gas pipes for outdoor units, brazed connection; liquid pipes, flare connection. Note
that the branched sections are brazed.
Warning:
Always use extreme care to prevent the refrigerant gas from leaking while
using fire or flame. If the refrigerant gas comes in to contact with a flame
from any source, such as a gas stove, it breaks down and generates a poi-
sonous gas which can cause gas poisoning. Never weld in an unventilated
room. Always conduct an inspection for gas leakage after installation of the
refrigerant piping has been completed.
8.1. Caution
This unit uses refrigerant R410A. Follow the local regulations on materials and
pipe thickness when selecting pipes. (Refer to the table below.)
1 Use the following materials for refrigeration piping.
• Material: Use copper alloy seamless pipes made of phosphorus deoxi-
dized copper. Ensure the inner and outer surfaces of the pipes are clean
and free from hazardous sulfur, oxide, dusts, shaving particles, oils, and
moisture (contamination).
• Size: Refer to item 8.2. for detailed information on refrigerant piping sys-
tem.
2 Commercially available piping often contains dust and other materials. Always
blow it clean with a dry inert gas.
3 Use care to prevent dust, water or other contaminants from entering the piping
during installation.
4 Reduce the number of bending portions as much as possible, and make bend-
ing radii as big as possible.
5 Always observe the restrictions on the refrigerant piping (such as rated length,
height difference, and piping diameter) to prevent equipment failure or a de-
cline in heating/cooling performance.
6 Either a lack or an excess of refrigerant causes the unit to make an emergency
stop. Charge the system with an appropriate amount of refrigerant. When serv-
icing, always check the notes concerning pipe length and amount of additional
refrigerant at both locations, the refrigerant volume calculation table on the
back of the service panel and the additional refrigerant section on the labels
for the combined number of indoor units (Refer to item 8.2. for detailed infor-
mation on refrigerant piping system).
7 Be sure to charge the system using liquid refrigerant.
Size (mm) Radial thickness (mm) Pipe type
ø6.35 0.8 Type-O
ø9.52 0.8 Type-O
ø12.7 0.8 Type-O
ø15.88 1.0 Type-O
ø19.05 1.2 Type-O
ø19.05 1.0 Type-1/2H or H
ø22.2 1.0 Type-1/2H or H
ø25.4 1.0 Type-1/2H or H
ø28.58 1.0 Type-1/2H or H
ø31.75 1.1 Type-1/2H or H
ø34.93 1.2 Type-1/2H or H
ø41.28 1.4 Type-1/2H or H
Copper pipe size and radial thickness for R410A.
*For pipe sized ø19.05 for R410A air conditioner, choice of pipe type is up to you.
8 Never use refrigerant to perform an air purge. Always evacuate using a
vacuum pump.
9 Always insulate the piping properly. Insufficient insulation will result in a de-
cline in heating/cooling performance, water drops from condensation and other
such problems (Refer to item 9.4 for thermal insulation of refrigerant piping).
0 When connecting the refrigerant piping, make sure the valve of the outdoor
unit is completely closed (the factory setting) and do not operate it until the
refrigerant piping for the outdoor and indoor units has been connected, a re-
frigerant leakage test has been performed and the evacuation process has
been completed.
A Braze only with non-oxide brazing material for piping. Failure to do so
may damage the compressor. Be sure to perform the non-oxidation braz-
ing with a nitrogen purge.
Do not use any commercially available anti-oxidizing agent since it may
cause pipe corrosion and degrading of the refrigerant oil.
Please contact Mitsubishi Electric for more details.
(Refer to item 9.2. for details of the piping connection and valve operation)
B Never perform outdoor unit piping connection work when it is raining.
Warning:
When installing and moving the unit, do not charge the system with any
other refrigerant other than the refrigerant specified on the unit.
- Mixing of a different refrigerant, air, etc. may cause the refrigerant cycle to mal-
function and may result in severe damage.
Caution:
• Use a vacuum pump with a reverse flow check valve.
- If the vacuum pump does not have a reverse flow check valve, the vacuum
pump oil may flow back into the refrigerant cycle and cause deterioration of
the refrigerator oil.
• Do not use the tools shown below used with conventional refrigerant.
(Gauge manifold, charge hose, gas leak detector, check valve, refrigerant
charge base, vacuum gauge, refrigerant recovery equipment)
- Mixing of conventional refrigerant and refrigerator oil may cause the refrig-
erator oil to deteriorate.
- Mixing of water will cause the refrigerator oil to deteriorate.
- R410A refrigerant does not contain any chlorine. Therefore, gas leak detec-
tors for conventional refrigerants will not react to it.
• Manage the tools used for R410A more carefully than normal.
- If dust, dirt, or water gets in the refrigerant cycle, the refrigerator oil will dete-
riorate.
•Never use existing refrigerant piping.
- The large amount of chlorine in conventional refrigerant and refrigerator oil
in the existing piping will cause the new refrigerant to deteriorate.
• Store the piping to be used during installation indoors and keep both
ends of the piping sealed until just before brazing.
- If dust, dirt, or water gets into the refrigerant cycle, the oil will deteriorate and
the compressor may fail.
• Do not use a charging cylinder.
- Using a charging cylinder may cause the refrigerant to deteriorate.
• Do not use special detergents for washing piping.
8.2. Refrigerant piping system
Connection example
[Fig. 8.2.1] (P.3)
Å Outdoor model ı Liquid pipe
Ç Gas pipe
A Outdoor unit B Indoor unit