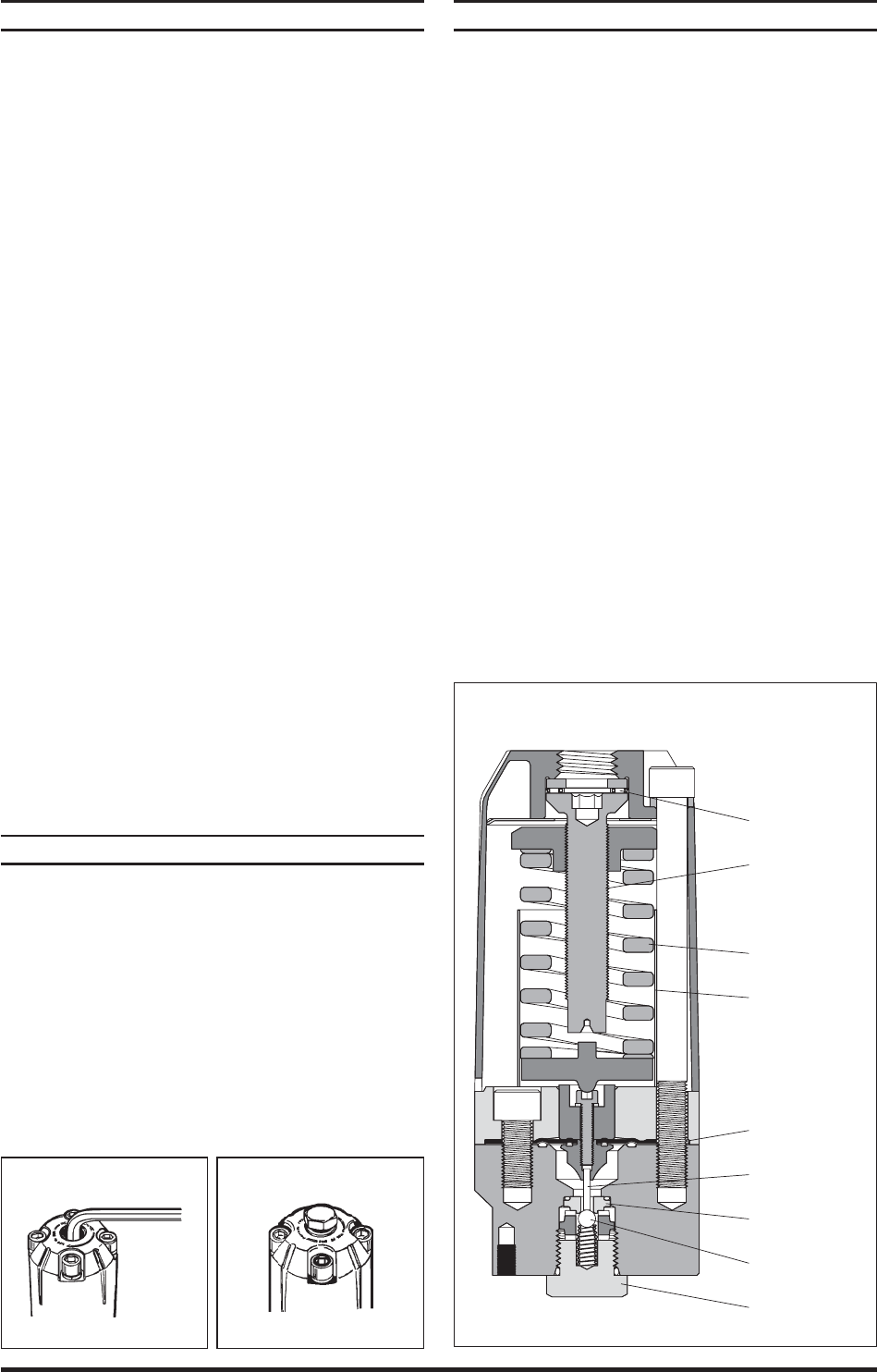
65178X-XXX-B (en) Page 3 of 8
OPERATING INSTRUCTIONS
Refer to pages 4 and 5 for parts reference.
To INCREASE outlet pressure, turn the (6) adjusting screw
CLOCKWISE (see gure 3).
To DECREASE outlet pressure, turn the (6) adjusting
screw COUNTERCLOCKWISE (see gure 3).
NOTE: Part Y106-109 Allen wrench is included to make neces-
sary pressure adjustments.
FLUSH-OUT FEATURE FOR DOWNSTREAM MODELS ONLY.
See gure 4.
Flush the regulator periodically. The interval may vary de-
pending on the amount and type of material used.
By using a wrench and “flush-out” plug (provided), the
operator is able to move the entire spindle downward
and force the ball off the seat which should purge the
regulator of particle build-up.
NOTE: The flush-out procedure temporarily overrides the
adjusted pressure. It will not, however, affect the regulator
setting when ushing operation is completed.
FLUSH-OUT PROCEDURE
Remove spray gun or dispensing device, this will allow
any particles to clear from the system.
Insert (21) flush-out plug and turn clockwise until it
touches the (4) washer (see view on page 5).
Turn up to two turns maximum. This will allow the ball to
unseat and pass material at free ow (unregulated). DO
NOT attempt to turn further to avoid damage.
Turn the plug back to its original position.
SEAT PLUG FEATURE
The (47) plug, located at the base of the regulator, can be
removed for access to the ball and seat assembly for clean-
ing and inspection for wear. With this feature, the regulator
does not have to be unthreaded from the pumping system.
Be certain to relieve system pressure (See “WARNING: DISAS-
SEMBLY HAZARD”).
MAINTENANCE
Disassembly should be done on a clean work bench and
use clean cloths.
If replacement parts are necessary, refer to the parts list
and drawings on pages 4 and 5.
Upon reassembly, lubricate parts and use Loctite where
indicated. Follow the torque speci cations as shown.
Service kits are available, which include parts typically
needed for an overhaul.
Keep good records of service activity and include the
regulator in a preventive maintenance program.
Certain “Smart Parts” are indicated with a “
” in the parts
list, these parts should be available for fast repair and re-
duction of down time.
View of Spring
Adjustment Procedure.
View of Flush-Out Plug.
Figure 3 Figure 4
1.
2.
3.
4.
TROUBLE SHOOTING
No uid pressure.
Check for damaged or worn diaphragms.
Look for possible obstruction by hardened material or
foreign matter, periodically use the regulator “Flush-out”
feature (Downstream models only). Use a uid lter up-
stream from the regulator.
Pressure creeps above the setting when system is
dead ended and in a static (no ow) mode.
Check for dirty seat and clean as appropriate.
Check for worn or damaged seat and replace if necessary.
Outlet pressure drops below setting.
Check pump for proper operation and check for possible
leakage problems.
Look for a clogged supply line problem, ush the supply
line.
Fluid leakage from spring housing.
Check the bonnet hold-down screws and the plate hold
down screws and re-torque as needed.
Check for damaged diaphragm, replace as needed.
Regulator will not function, even when dispens-
ing device is opened.
Check for possible obstruction in the uid line.
Inlet pressure is too high, causing a “Lock-Out” situation.
Read “WARNING: MISAPPLICATION HAZARD” found on
page 2.
Typical Downstream Regulator Cross Section
View Showing Major Components.
Adjusting Spring
Spring Stop
(used
to prevent compressing
spring to solid height)
Dual Diaphragm
Valve Stem
Seat
Ball
Seat Plug
Bearing
Adjusting Screw
Figure 5