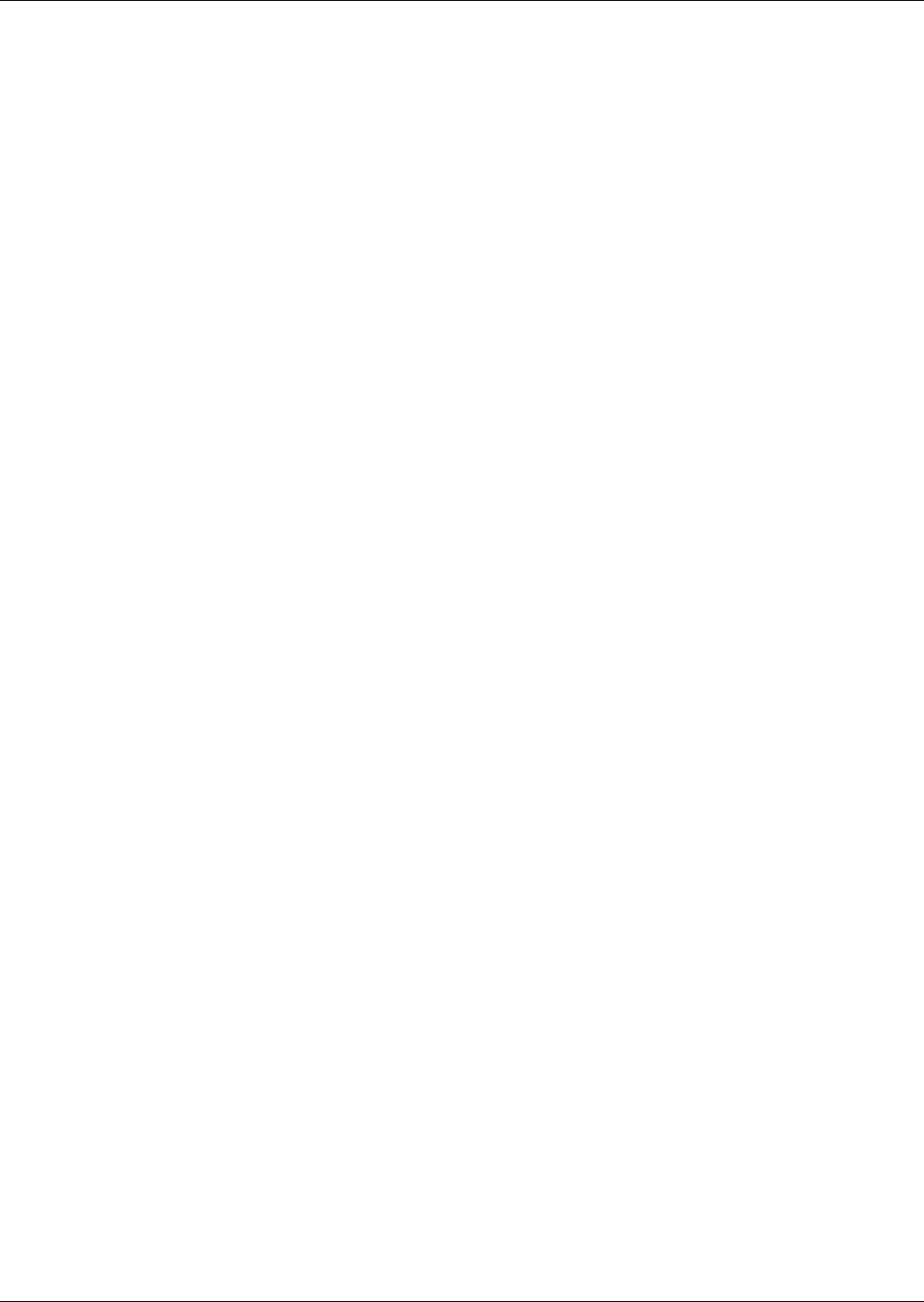
Glycol/GLYCOOL-Cooled Models—Self-Contained Compressor
43 Liebert
®
Challenger 3000
™
5.4 Glycol Piping
These guidelines apply to the field leak checking and fluid requirements for field piping systems.
General Guidelines
• Equipment damage and personal injury can result from improper piping installation, leak
checking, fluid chemistry and fluid maintenance.
• Follow local piping codes, safety codes.
• Qualified personnel must install and inspect system piping.
• Contact a local water consultant regarding water quality, corrosion protection and freeze
protection requirements.
• Install manual shutoff valves at the supply and return line to each indoor unit and drycooler to
permit routine service and emergency isolation of the unit.
NOTICE
Risk of water leakage. Can cause severe property damage and loss of critical data center
equipment.
This unit requires a water drain connection. It may require an external water supply to
operate the humidifier. Improper installation, application and service practices can result in
water leakage from the unit.
Do not locate the Liebert Challenger 3000 directly above any equipment that could sustain
water damage. Emerson recommends installing monitored leak detection equipment for the
unit and supply lines.
NOTICE
Risk of frozen fluids. Can cause equipment and building damage.
Freezing system fluids can rupture piping. Complete system drain-down cannot be ensured.
When the field piping or unit may be exposed to freezing temperatures, charge the system
with the proper percentage of glycol and water for the coldest design ambient.
Automotive antifreeze is unacceptable and must NOT be used in any glycol fluid system.
NOTICE
Risk of corrosion. Can cause equipment damage.
Read and follow individual unit installation instructions for precautions regarding fluid
system design, material selection and use of field-provided devices. Liebert systems contain
iron and copper alloys that require appropriate corrosion protection.
Contact a local water consultant regarding water quality, corrosion and freeze protection
requirements.
Water chemistry varies greatly by location, as do the required additives, called inhibitors,
that reduce the corrosive effect of the fluids on the piping systems and components. The
chemistry of the water used must be considered, because water from some sources may
contain corrosive elements that reduce the effectiveness of the inhibited formulation.
Sediment deposits prevent the formation of a protective oxide layer on the inside of the
coolant system components and piping. The water/coolant fluid must be treated and
circulating through the system continuously to prevent the buildup of sediment deposits and
or growth of sulfate reducing bacteria.
Preferably, surface waters that are classified as soft and are low in chloride and sulfate ion
content should be employed. Proper inhibitor maintenance must be performed in order to
prevent corrosion of the system. Consult glycol manufacturer for testing and maintenance of
inhibitors.
Commercial ethylene glycol (Union Carbide Ucartherm, Dow Chemical Dowtherm SR-1 and
Texaco E.G. Heat Transfer Fluid 100), when pure, is generally less corrosive to the common
metals of construction than water itself. It will, however, assume the corrosivity of the water