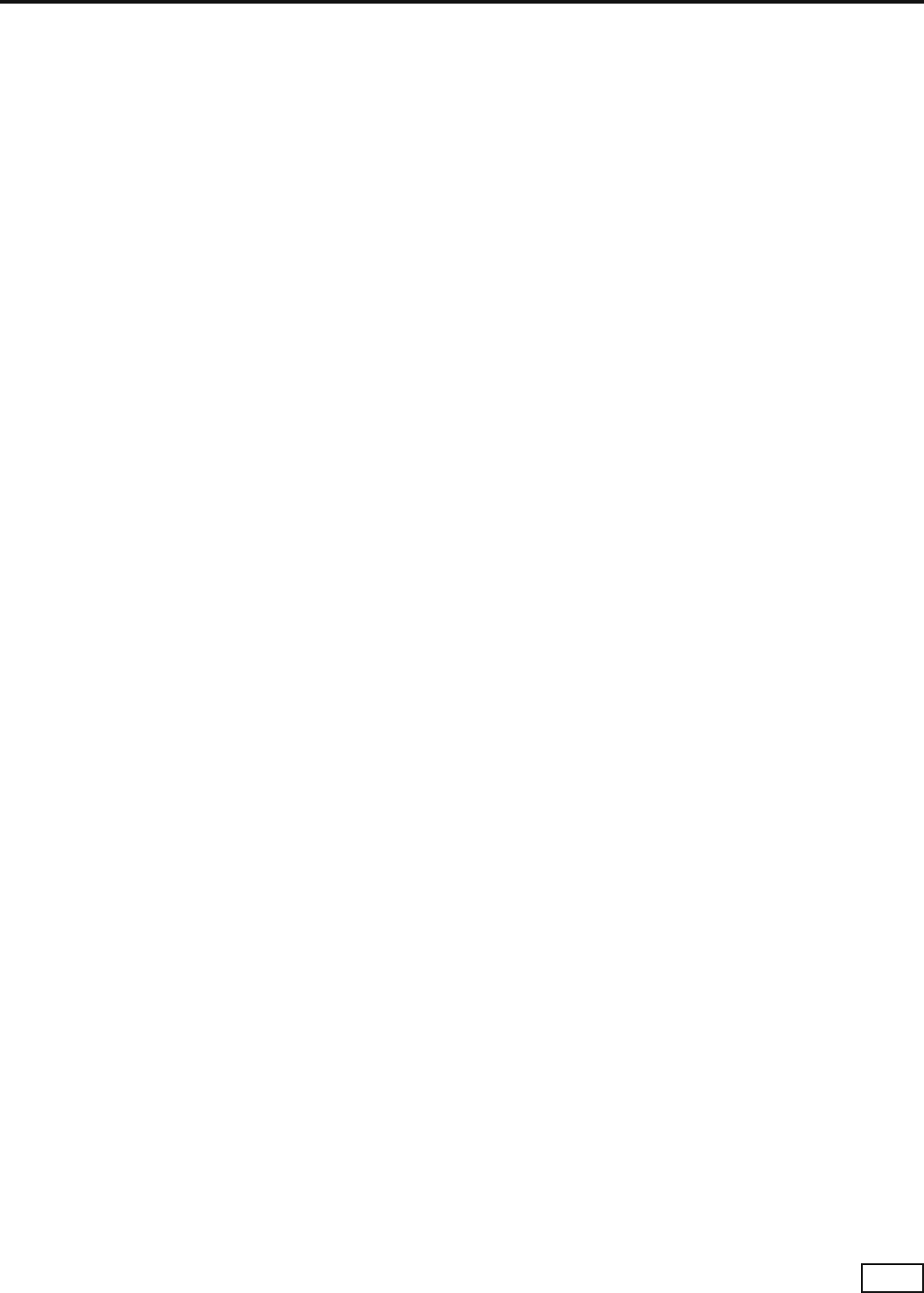
Single-Stage Outdoor Split
R22 Systems
51
Carrier Indoor & Outdoor Split Geothermal Heat Pumps - Rev.: 08/10/05
GT-S Outdoor Split (38WQS) Series
General
The liquid source heating/cooling split con dens ing units
shall be ARI/ASHRAE/ISO 13256-1 loop per for mance
certifi ed and listed by a nationally recognized safety-
testing laboratory or agency, such as Un der writ er’s
Lab o ra to ry (UL), or Canadian Stan dards Association
(CSA-US). Each unit shall be water run-tested at the
factory. Each unit shall be pallet mounted and shipped in
clear shrink wrap for visual shipping damage inspection.
The units shall be war rant ed by the man u fac tur er
against defects in materials and workmanship for a
period of fi ve years on all parts, and ten years on the
compressor and refrigerant circuit parts with a service
labor allowance during the fi rst 30 days. An optional
extended war ran ty is available for the GT-S
Split Series
units, which adds a labor allowance and trip charge.
The liquid source units shall be designed to operate with
entering liquid temperature between 20°F and 120°F.
Casing & Cabinet
The cabinet shall be weather resistant and designed
for outdoor installations. The cabinet shall be fabricated
from heavy-gauge galvanized steel painted with a epoxy
powder coat paint with a 1000 hr. salt spray test rating.
The interior shall be insulated with 1/2" thick, multi-density,
coated glass fi ber with edges sealed or tucked under
fl anges. Two compressor com part ment access panels
shall be provided and shall be removable with linesets
and water piping in place. The internal com po nent layout
shall provide for major service with the unit in-place for
restricted access installations. The cabinet shall provide
adequate space to house the one or two pump Flow
Controller pumping module within the cabinet.
Refrigerant Circuit
All units shall contain split refrigerant circuits employing
a hermetically sealed com pres sor, thermal expansion
valve, reversing valve, coaxial tube water-to-refrigerant
heat exchanger, service ports, and backseating service
valves. Compressors shall be high-effi ciency advanced
scroll or rotary type designed for heat pump duty and
mounted on vibration isolators. Compressor motors
shall be single phase PSC with internal overload
pro tec tion. A factory installed bidirectional fi lter drier
shall be provided. The coaxial water-to-refrigerant
heat exchanger shall be designed for close approach
temperatures and be con struct ed of a convoluted copper
(optional cupronickel) inner tube and a steel outer
tube. The thermal expansion valve shall provide proper
superheat over the entire liquid temperature range with
min i mal “hunting”. The valve shall operate only in the
heating mode with the use of an internal check valve.
The water-to-refrigerant heat exchanger and refrigerant
suction lines shall be insulated to prevent condensation
at low liquid temperatures. Air coil con nec tions shall
be made through brass backseating service valves
with built-in Schrader ports. Hot Water Generator
(desuperheater) connections shall be accomplished with
1/2” backseating service valves.
Electrical
CXM Control - A microprocessor-based compressor
controller (CXM) shall be provided to monitor and
control unit operation. The control shall provide high
and low pressure monitoring, fi eld selectable low water
temperature sensing, over/under voltage monitoring,
and unit performance sentinel (UPS). The control shall
also provide for water valve connection, a test mode,
short cycle protection, random start-up, as well as fault
LED, fault mem o ry, and intelligent fault retry.
The control shall employ quick attach harness
as sem blies for low voltage connections to the control
board to aid in troubleshooting or replacement. An
integral terminal block with screw ter mi nals shall
be provided on the control for all fi eld low voltage
connections. Line voltage lugs shall be provided for unit
wiring. Units shall have knockouts for entrance of low
and line voltage wiring. The control box shall be harness
plug-connected for easy removal.
Piping
Supply and return water connections shall be 1-1/4"
MPT fi ttings. All water piping shall be insulated to
prevent con den sa tion at low liquid temperatures.