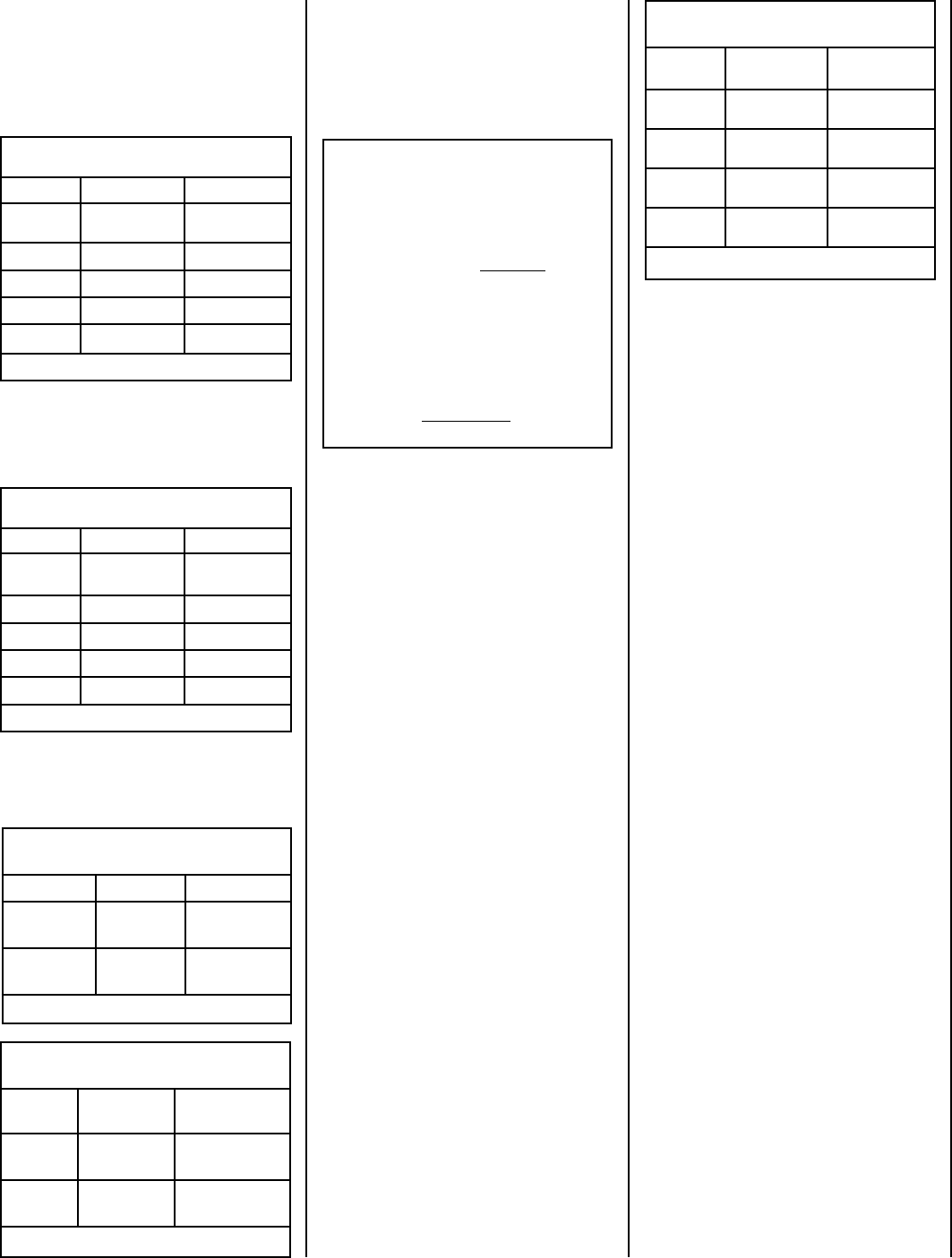
7
NOTE: DIAGRAMS & ILLUSTRATIONS ARE NOT TO SCALE.
Millivolt Models with
Manually-Modulated Gas Valve
Natural Gas Propane Gas
Model Input Rate
(BTU/HR)
Input Rate
(BTU/HR)
MPB3328
13,500 to 17,500 13,500 to 17,500
MPB3530
16,000 to 20,000 16,500 to 20,000
MPB4035
24,000 to 30,000 22,300 to 28,000
MPB4540
24,750 to 31,000 23,000 to 29,000
Table 1
Electronic Models with
Fixed-Rate Gas Valve
Natural Gas Propane Gas
Model Input Rate
(BTU/HR)
Input Rate
(BTU/HR)
MPB3328
17,500 17,500
MPB3530
20,000 20,000
MPB4035
30,000 28,000
MPB4540
31,000 29,000
Table 2
Test gauge connections are provided on the front
of the millivolt gas control valve (identified OUT
for the manifold side and IN for inlet pressure. A
1/8" NPT test gauge connection is provided on the
electronic gas control valve adjacent to the outlet
to the main burner.
Burner Orifice Sizes
Elevation 0-4500 feet ( 0-1372 meters)
Models
NaturalGas
drill size (inches)
Propane Gas
drill size (inches)
MPB-3328 #47 (.0785") *
39L66•
1.2mm (.048")*
99K78•
MPB-3530 #44 (.086")*
60J80•
#55 (.052")*
19L52•
MPB-4035 #37 (.104")*
24M10•
1/16"
(.0625")*
21L01•
MPB-4540 #36 (.1065")*
18L40•
#52 (.0635")*
37G00 •
Table 5
* Standard size installed at factory
• Part /Cat. Number
Millivolt Models - BTU Input
Millivolt models come standard with the
manually-modulated gas valve; flame appear-
ance and heat output can be controlled at the
gas valve. Input of for these models is shown
in Table 1.
Electronic Models -
Electronic models have a fixed rate gas valve.
Input of electronic models is shown in Table 2.
Manifold Gas Supply Pressure
(all models)
Fuel # Low
(millivolt only)
High
Natural
Gas
(Lo) 2.2" WC
(0.55 kPa)
(Hi) 3.5" WC
(0.87 kPa)
Propane
(Lo) 6.3" WC
(1.57 kPa)
(Hi) 10.0" WC
(2.49 kPa)
Table 4
Inlet Gas Supply Pressure
(all models)
Fuel # Minimum Maximum
Natural Gas
5.0" WC
(1.24 kPa)
10.5" WC
(2.61 kPa)
Propane
11.0" WC
(2.74 kPa)
13.0" WC
(3.23 kPa)
Table 3
Gas Pressure - All Models
Tables 3 and 4 show the appliances' inlet and
manifold gas pressure requirements:
These appliances must be isolated
from the gas supply piping system (by
closing their individual manual shut-off
valve) during any pressure testing of
the gas supply piping system at test
pressures equal to or less than 1/2 psig
(3.5 kPa).
These appliances and their individual
shut-off valves must be disconnected
from the gas supply piping system dur-
ing any pressure testing of that system
at pressures greater than 1/2 psig (3.5
kPa).
Orifice Sizes - Sea Level to High Altitude
(All Models)
These appliances are tested and approved for
installation at elevations of 0-4500 feet (0-1372
meters) above sea level using the standard
burner orifice sizes (marked with an "*" in Table
5). For elevations above 4500 feet, contact your
gas supplier or qualified service technician.
Deration - At higher elevations, the amount
of BTU fuel value delivered must be reduced
by either:
• Using gas that has been derated by the gas
company.
• Changing the burner orice to a smaller size
as regulated by the local authorities having
jurisdiction and by the (USA) National Fuel
Gas Code NFPA 54/ANSI Z223.1 - latest
edition or, in Canada, the CAN/CSA-B149.1
codes - latest edition.
Install the appliance according to the regulations
of the local authorities having jurisdiction and,
in the USA, the National Fuel Gas Code NFPA
54 / ANSI Z223.1 - latest edition or, in Canada,
the CAN/CSA-B149.1 - latest edition.
NOTE: Flame appearance will diminish 4% per
thousand feet.
Burn-in Period
During the first few fires of this appliance there
will be some odor due to the curing of the
paint and burning off of lubricants used in the
manufacturing process. Depending on your
use, the burn-in period may take a few hours
or a few days.
KEEP YOUR HOUSE WELL VENTILATED
DURING THE CURING PROCESS. THE ODOR
AND HAZE EMITTED DURING THE CURING
PROCESS CAN BE QUITE NOTICEABLE AND
MAY SET OFF A SMOKE DETECTOR.
A white film may develop on the glass front
during the first few fires as part of the curing
process. The glass should be kept clean during
the first two weeks of use to prevent the film from
baking on (making it very difficult to remove).
See Cleaning Glass on Page 11.